Alumina Ceramic Mosaic Tiles
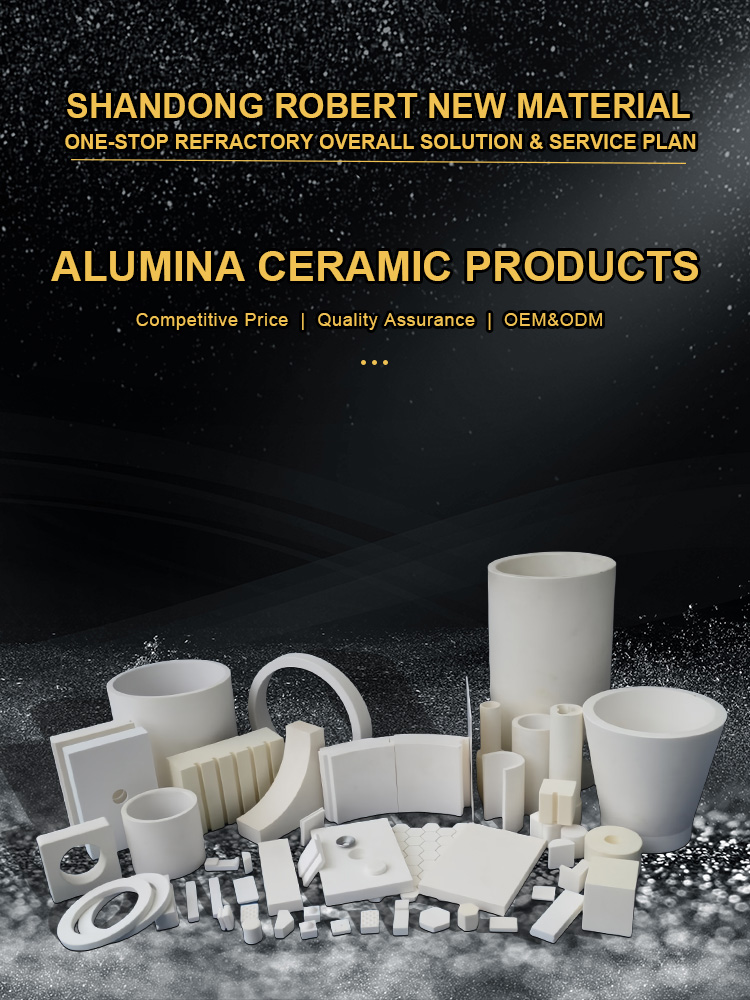
Product Catalog
1. Alumina Ball
(1) Alumina ceramic balls are a high-performance inorganic non-metallic material with aluminum oxide (Al2O3) as the main component.
Features:
High wear resistance; High temperature resistance; Corrosion resistance; High hardness; High compressive strength; Good thermal stability
Application:
Catalyst support and tower filler: In the reactor, alumina ceramic balls are used as catalyst covering support materials and tower fillers to increase the distribution points of gas or liquid to improve the reaction efficiency and protect the active catalyst with lower strength.
Grinding media: Widely used in fine grinding equipment such as ball mills and vibration mills to grind ores, slurries, wear-resistant materials, and powders such as coatings and paints. Its excellent wear resistance and roundness can avoid scratches during polishing and more fully contact with the polishing object.
Other applications: It is also widely used in many industries such as petrochemicals, building sanitary ceramics, non-metallic minerals, steel, and electronics.
(2) Alumina grinding ball is a kind of grinding medium made of bauxite, roller powder, industrial alumina powder, etc., through batching, grinding, powder making, molding, drying, sintering and other processes. Its main component is α-Al2O3, which has the characteristics of high hardness, high wear resistance and chemical stability, and is widely used in various grinding and polishing processes.
Application:
Ceramic and glass industry: used for grinding glaze and ceramic powder to improve the uniformity and finish of the product.
Coating industry: used for grinding and dispersing water-based and oil-based coatings to improve the fluidity and adhesion of coatings.
Electronic industry: used for grinding precision mechanical parts and optical components to ensure high precision and good surface quality.
New energy materials: used for grinding lithium battery materials to promote uniform distribution and performance improvement of materials. Environmental protection: used for wastewater treatment and sludge dehydration to remove impurities and pollutants in water.
Particle size range: 0.3-0.4, 0.4-0.6, 0.6-0.8, 0.8-1.0, 1.0-1.2, 1.2-1.4, 1.4-1.6, 1.8-2.0, 2.0-2.2, 2.2-2.4, 2.8-3.0, 3.0-3.2, 3.2-3.5, 4.5-5.0, 5.0-5.5, 6.0-6.5, 6.5-7.0, 8, 10, 12, 15, 20
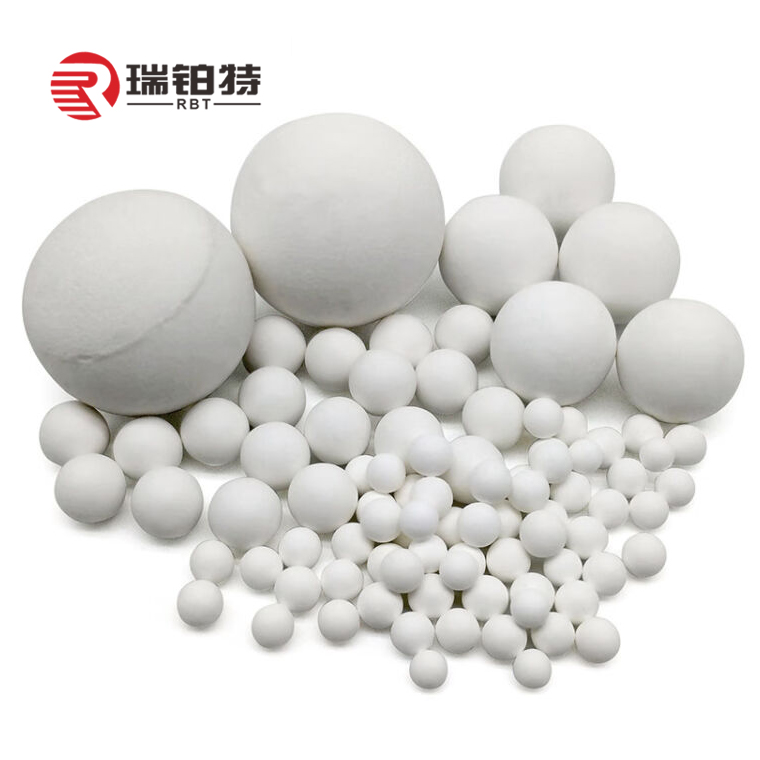
Alumina Grinding Balls
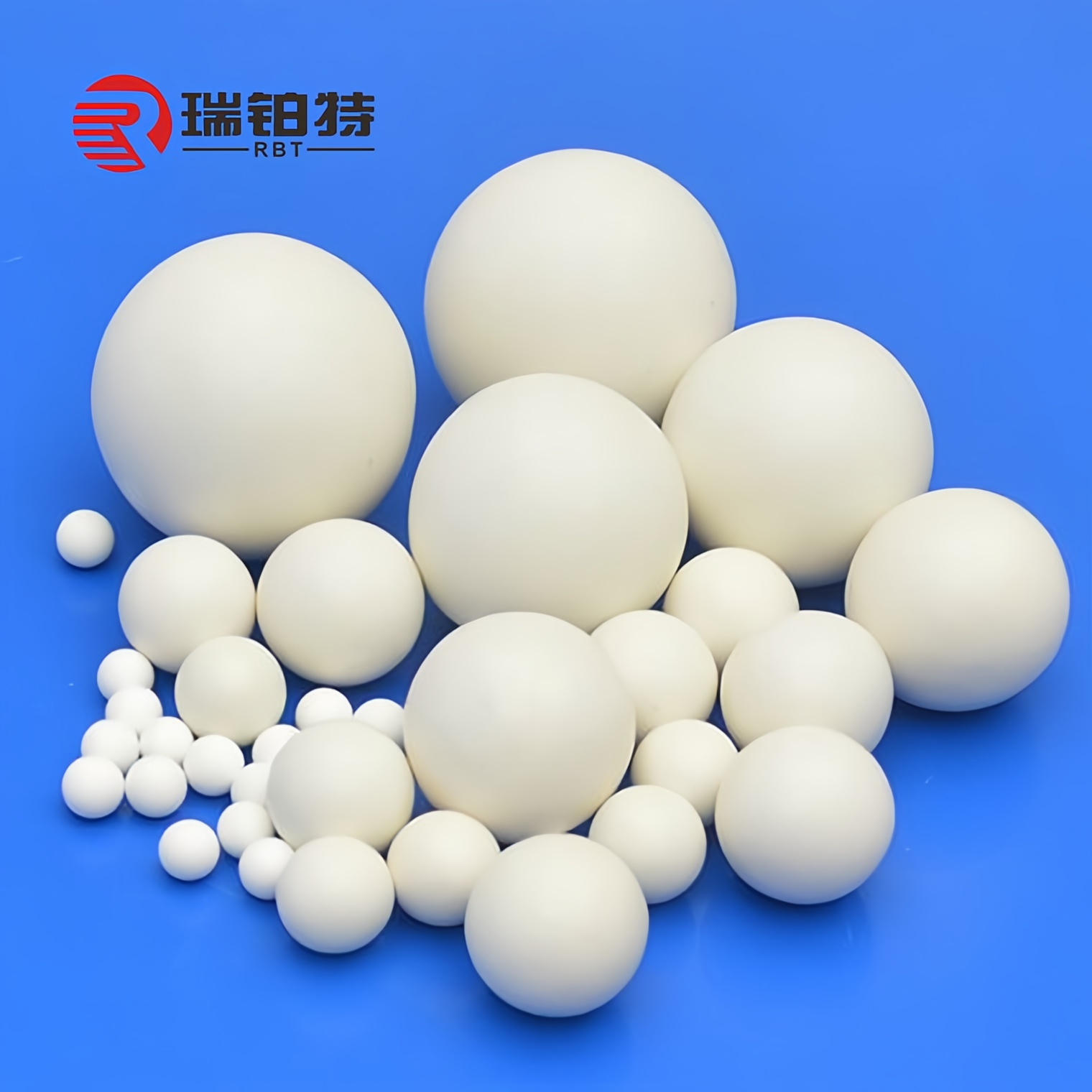
Alumina Ceramic Balls
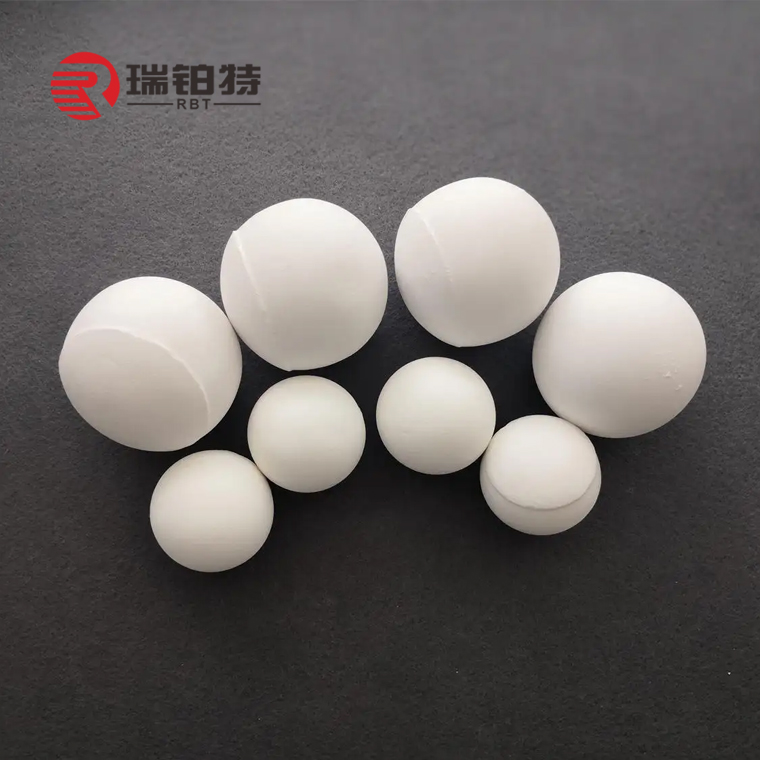
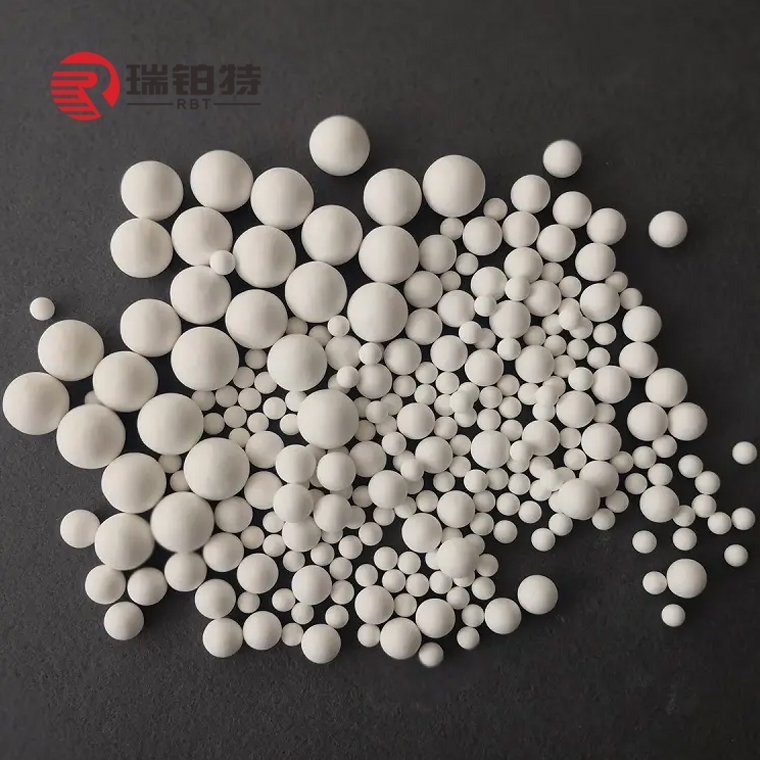
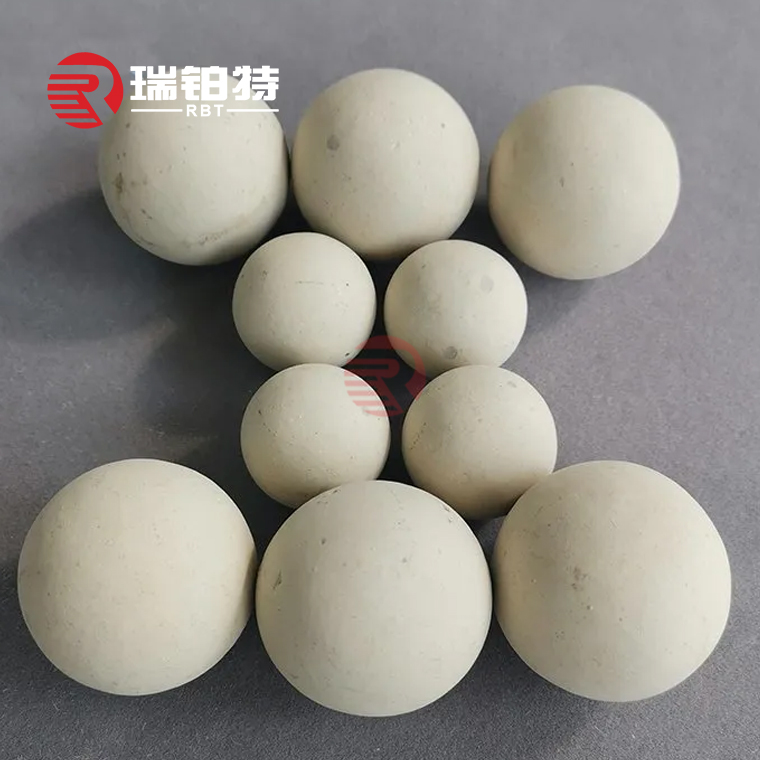
2. 92%, 95% Alumina Wear-resistant Ceramics(conventional, special-shaped, customized products)
(1) Wear-resistant ceramic mosaic tiles is a high-performance ceramic material, mainly made of high-strength ceramic materials such as alumina and silicon nitride. The surface is treated with special processes and has extremely high hardness and wear resistance. Its manufacturing process includes advanced technologies such as dry pressing and grouting, and the specifications are diverse to
meet the needs of different industrial applications.
Features:
1. High hardness: The Rockwell hardness of wear-resistant ceramic mosaic reaches HRA80-90, second only to diamond, and has extremely high hardness and wear resistance.
2. Wear resistance: Its wear resistance is equivalent to 266 times that of manganese steel and 171.5 times that of high chromium cast iron, showing wear resistance.
3. Light weight: The density is 3.6g/cm³, which is only half of that of steel, which can greatly reduce the equipment load and improve the equipment's operating efficiency.
4. Convenient construction: Wear-resistant ceramic mosaic is easy to install and maintain, reducing the difficulty and cost of construction.
Application:
Petrochemical industry: used as lining and wear-resistant parts in reactors, pipelines, pump bodies and other equipment, significantly extending the life of equipment and improving safety.
Mining and metallurgy: greatly improving wear resistance and production efficiency in wear parts of equipment such as ball mills, coal mills, and pulping machines.
Electric power industry: used in wear-resistant parts of coal-fired power generation, gas-fired power generation and other equipment, such as burners, coal mills, and dust collectors, effectively improving the service life and operating efficiency of equipment.
Machinery manufacturing: used to manufacture high-precision, high-wear-resistant parts, such as bearings, gears, and guide rails, significantly improving the performance and reliability of mechanical products.
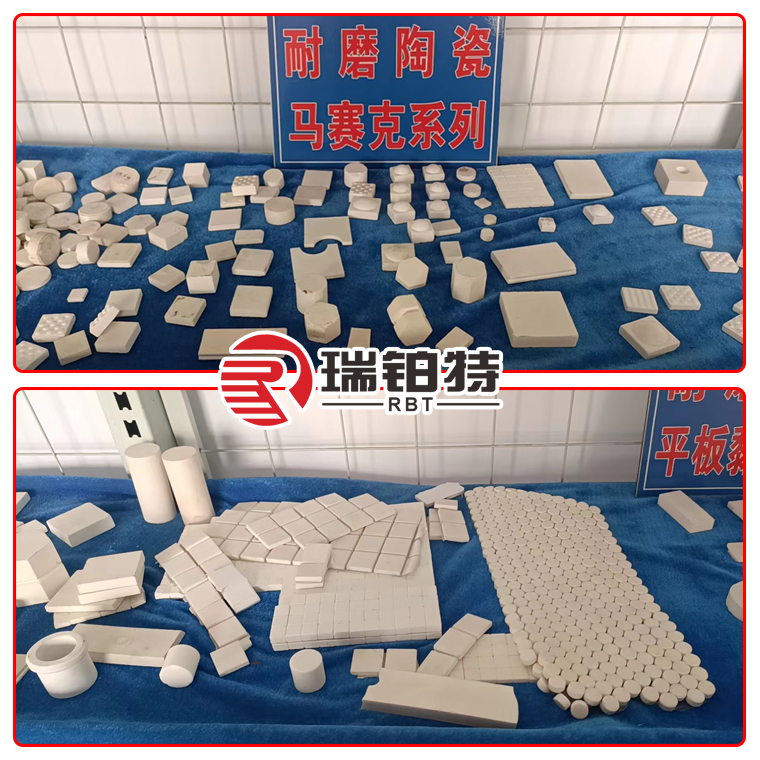
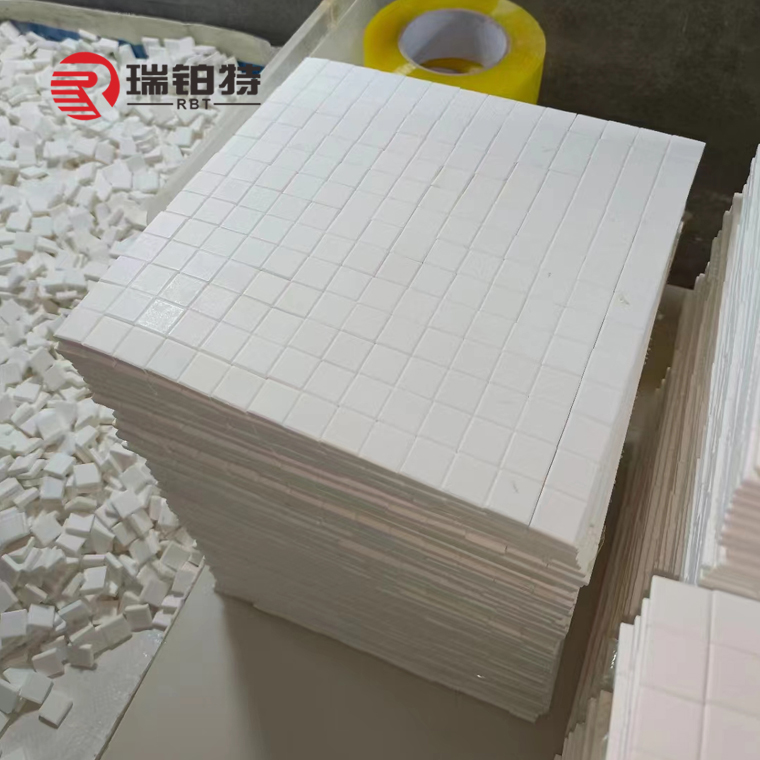
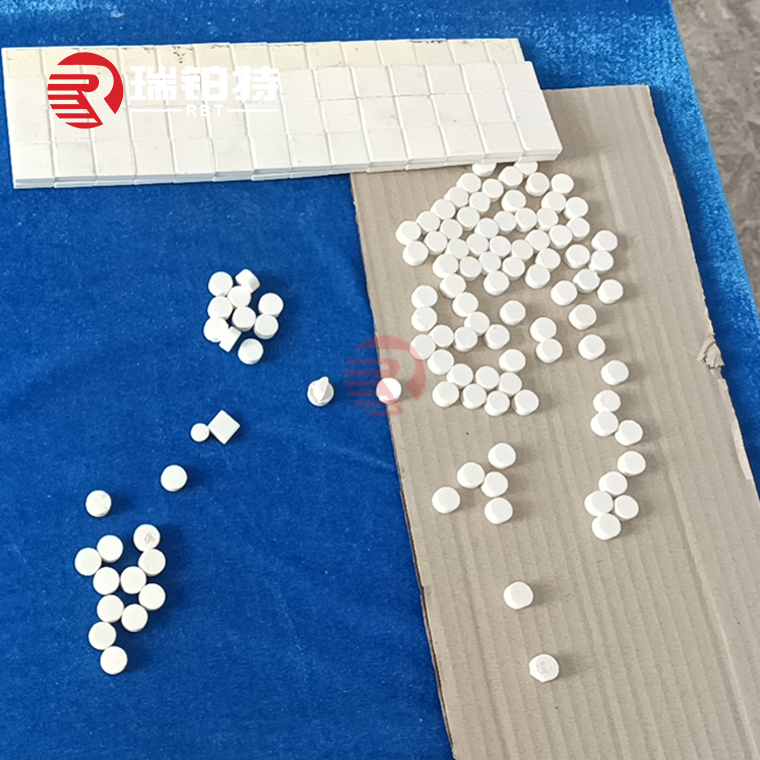
(2) Wear-resistant ceramic lining bricks are usually made of a composite of ceramic materials and matrix materials. Ceramic materials generally use high-alumina ceramics or zirconia ceramics, which have excellent wear resistance and compressive strength. The matrix material is usually steel or other metal materials, which provide the necessary support and toughness. By combining the ceramic layer with the metal matrix, a composite material that is both wear-resistant and sufficiently tough is formed.
Application:
Mining machinery: Protect crushing and screening equipment from ore impact.
Metallurgical industry: Used in high-temperature furnaces and casting equipment due to its excellent high temperature resistance and corrosion resistance.
Power industry: Used to protect coal powder conveying systems and boiler furnaces.
Cement production: Reduce direct contact between conveyor belts and materials and extend equipment life.
Chemical industry: Used in equipment such as ball mills to increase grinding output and fineness, reduce energy consumption and maintenance costs.
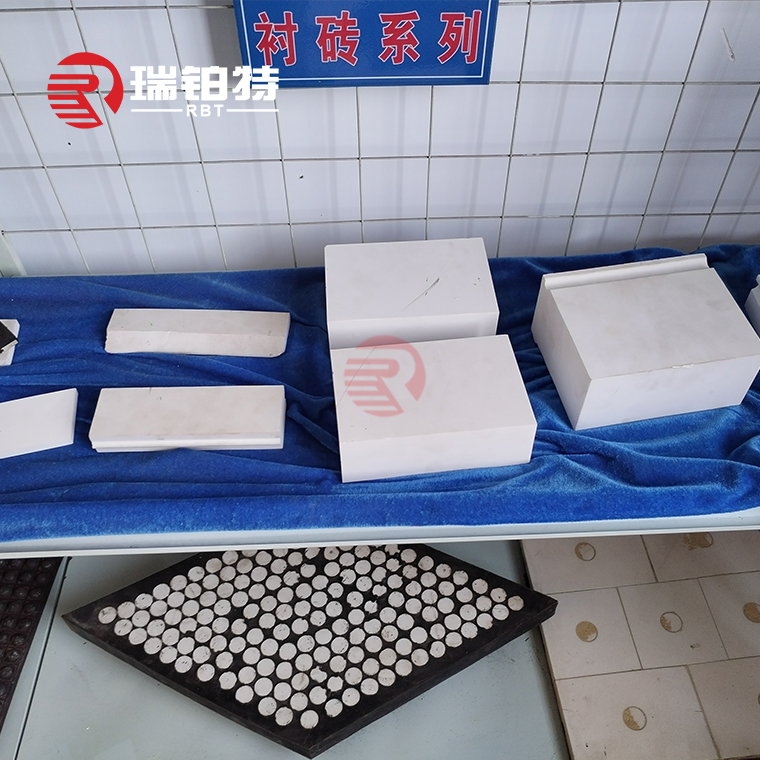

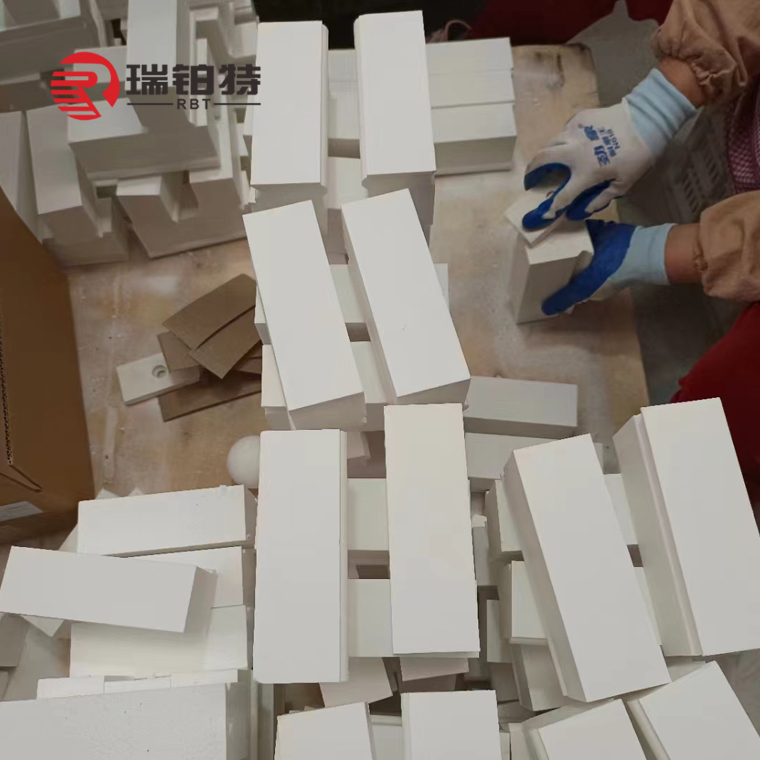
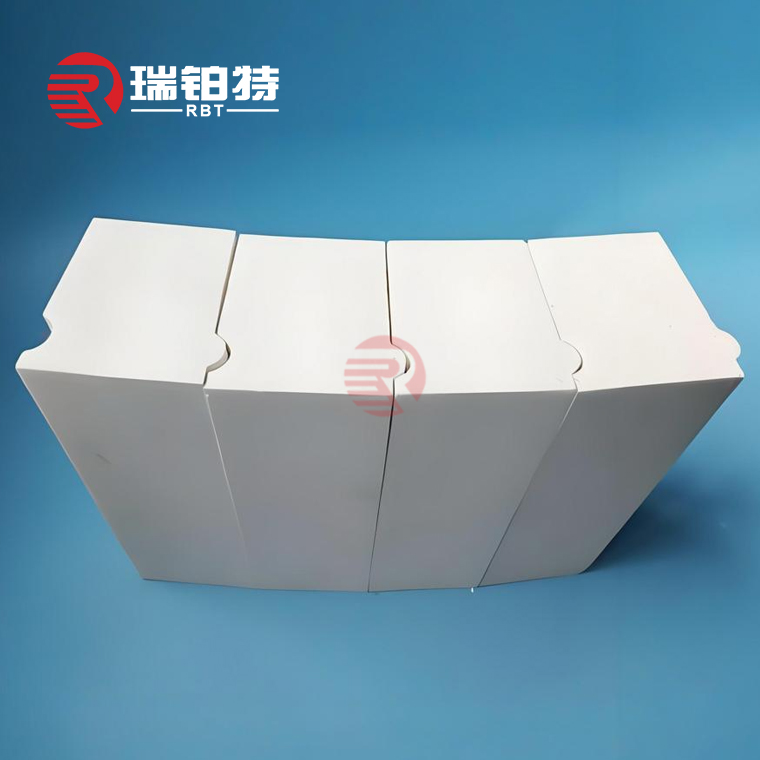
(3) Wear-resistant ceramic lining plates is a material with alumina (AL2O3) as the main body, supplemented with other ingredients, and sintered at a high temperature of 1700°C. It has excellent wear resistance, corrosion resistance and high temperature stability, and is widely used in coal conveying, material conveying systems, powder making systems, ash discharge, dust removal systems and other mechanical equipment with high wear in thermal power, steel, metallurgy, machinery, coal, mining, chemical, cement, port terminals and other enterprises.
Applications:
Mining industry: During mining, equipment is often affected by abrasives and impacts. The use of wear-resistant ceramic lining can effectively extend the service life of equipment and reduce maintenance costs.
Metallurgical industry: In metallurgical equipment, wear-resistant ceramic lining can resist the erosion of molten metal and ore to ensure the stable operation of equipment.
Chemical industry: In chemical production, equipment is often exposed to corrosive media. The use of wear-resistant ceramic lining can improve the durability of equipment and reduce failures caused by corrosion.
Power industry: In power equipment, wear-resistant ceramic linings can effectively reduce the wear of dust and other solid particles on equipment, ensuring the long-term stable operation of the equipment.
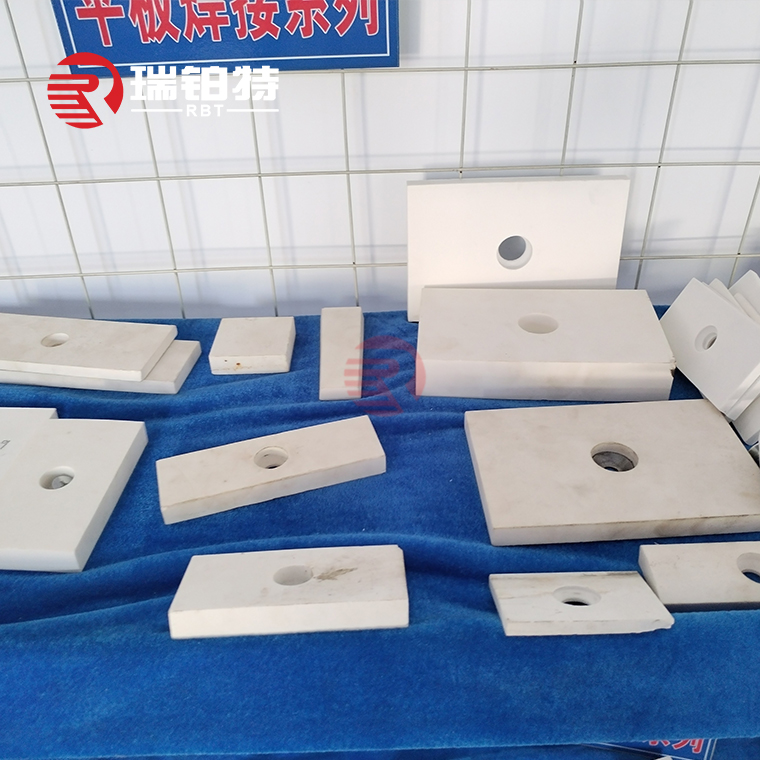
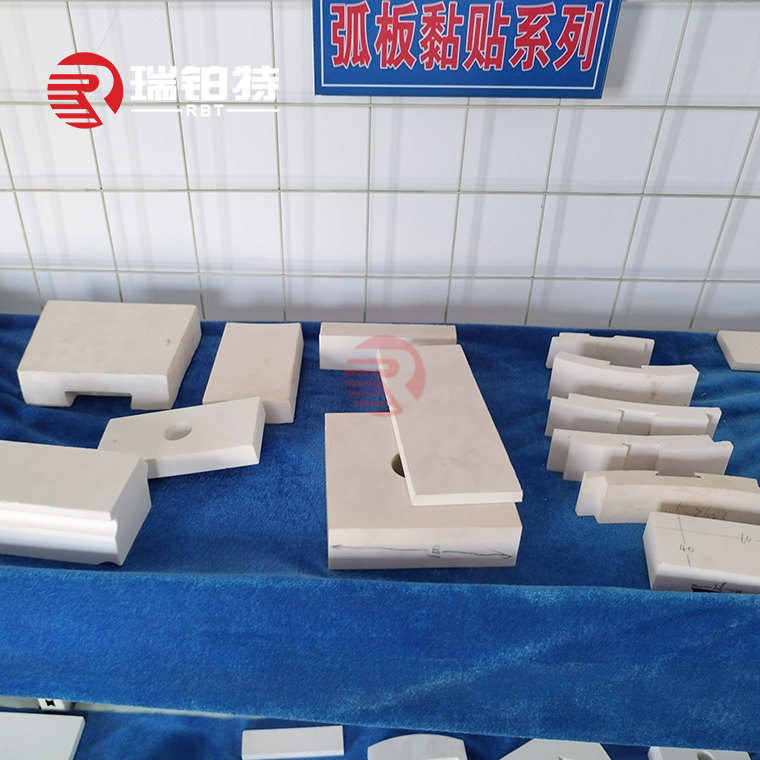
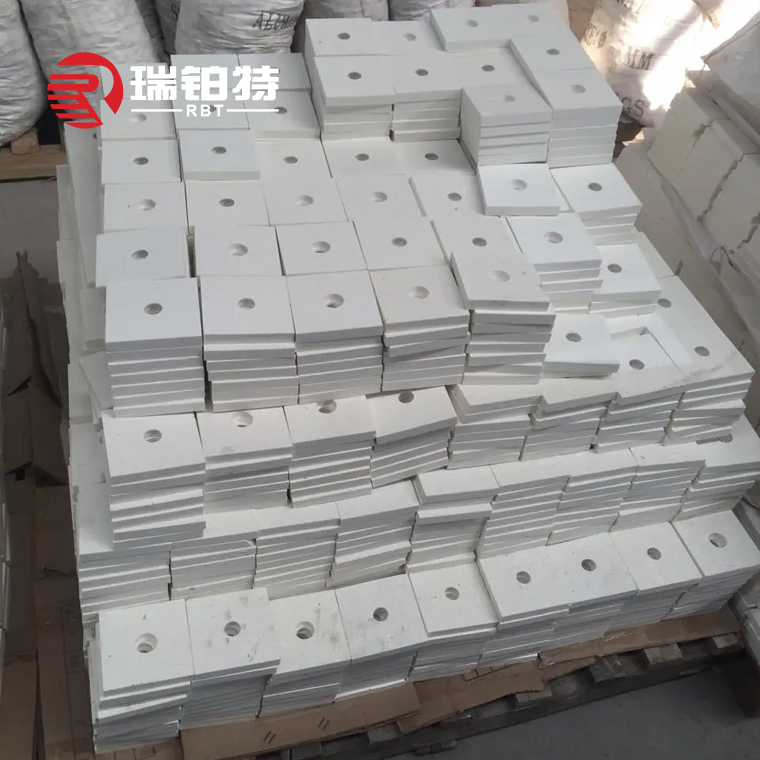
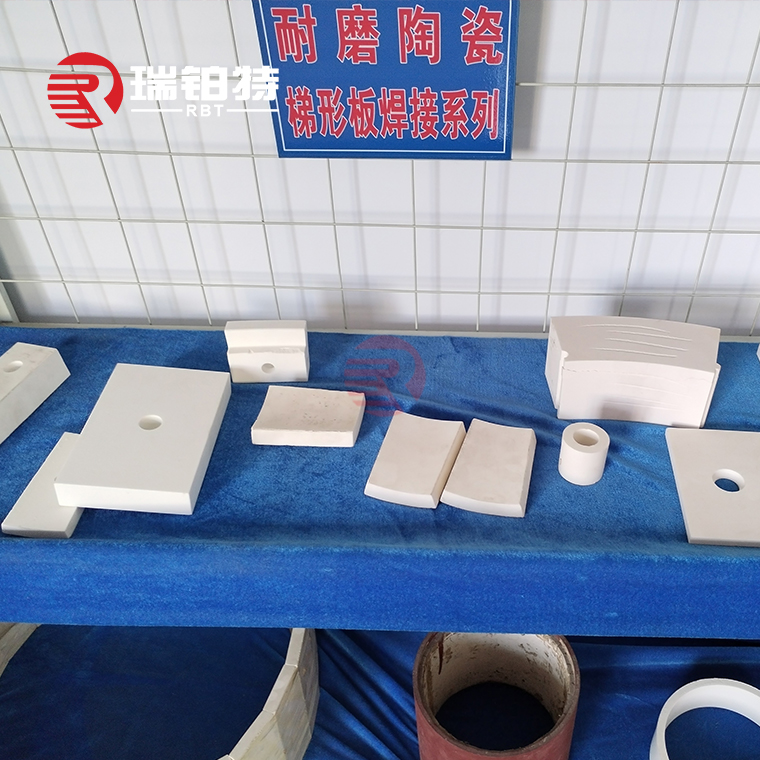
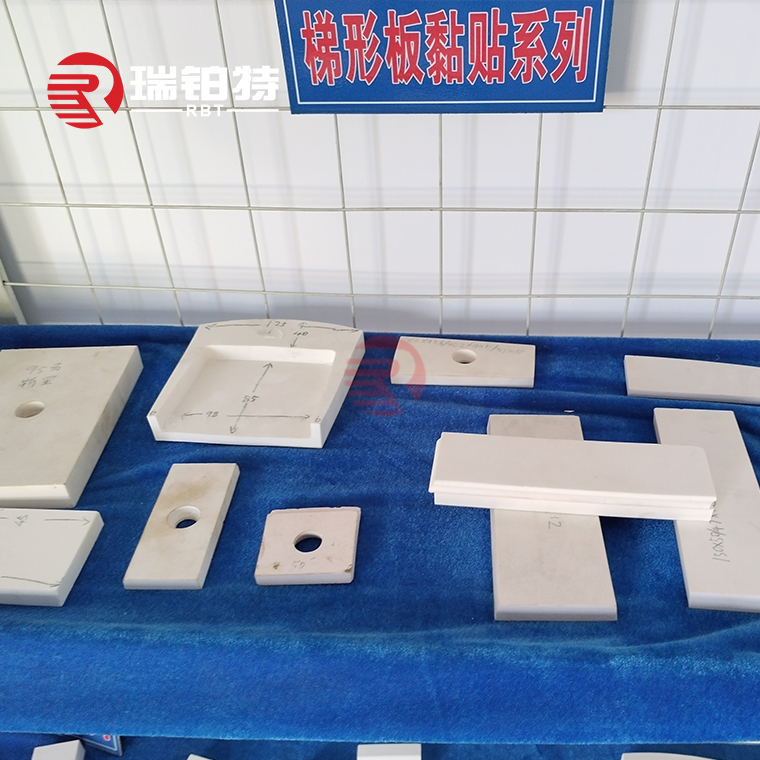
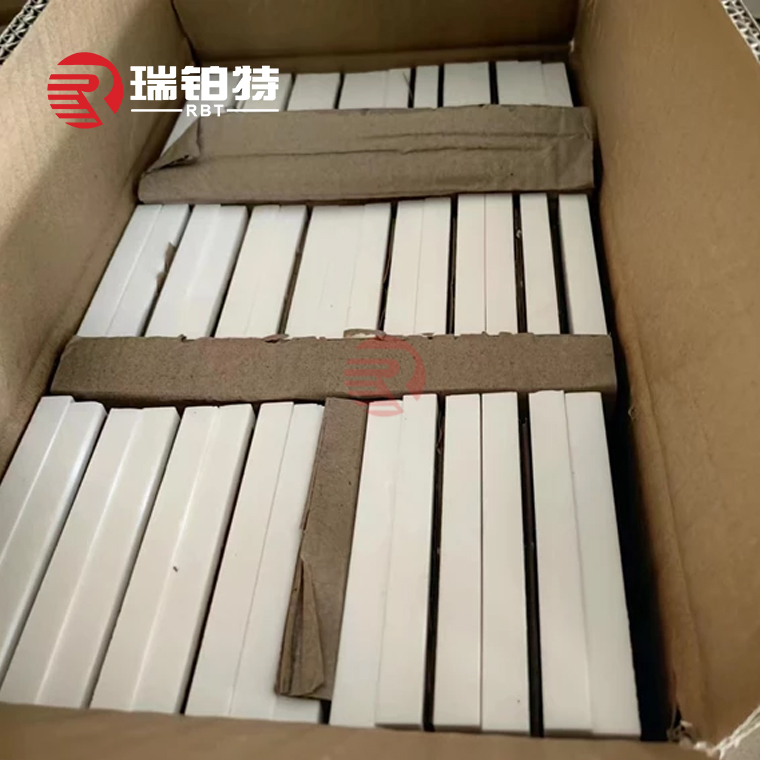
(4) Wear-resistant Ceramic Special-shaped Parts
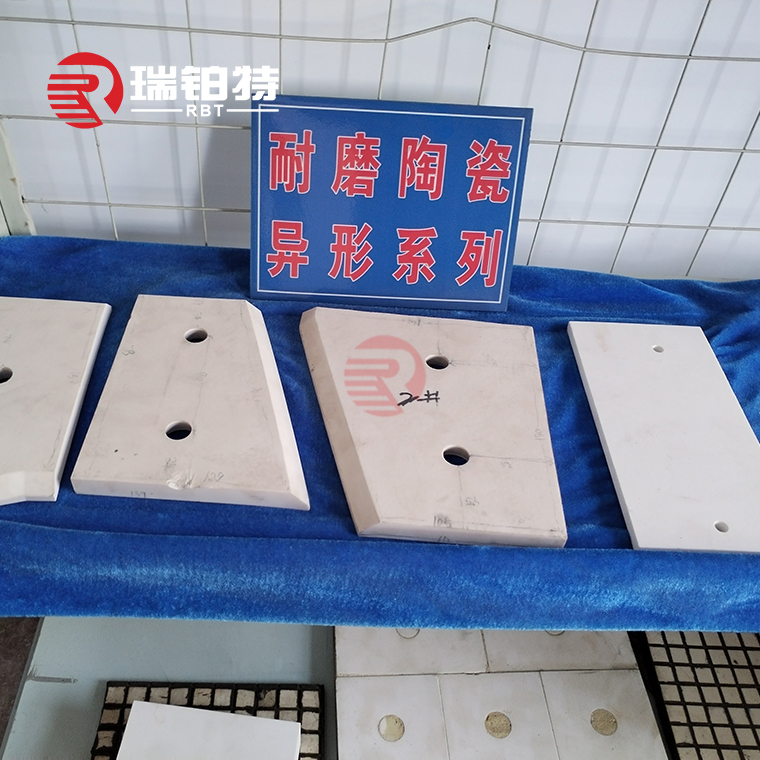
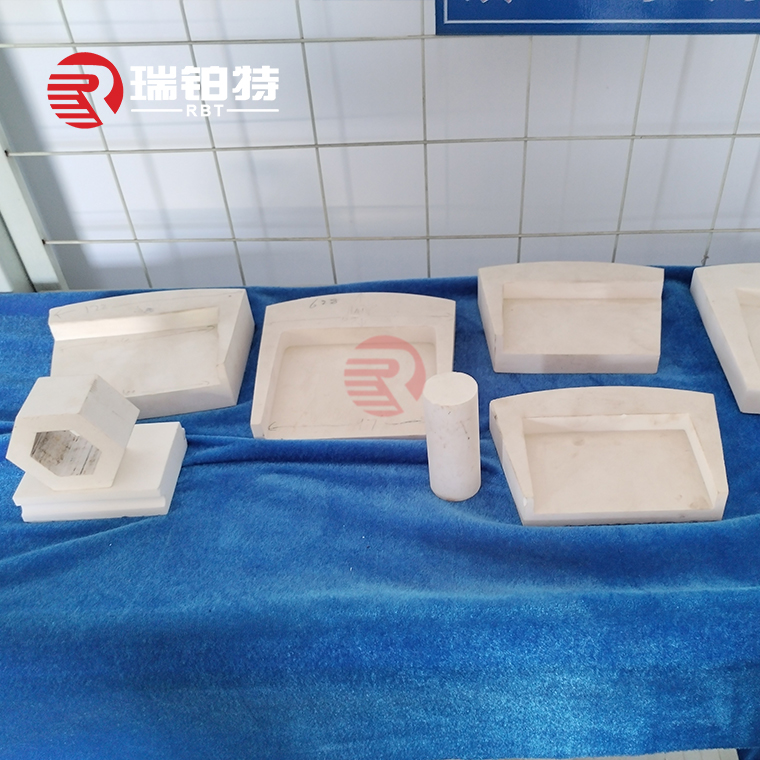
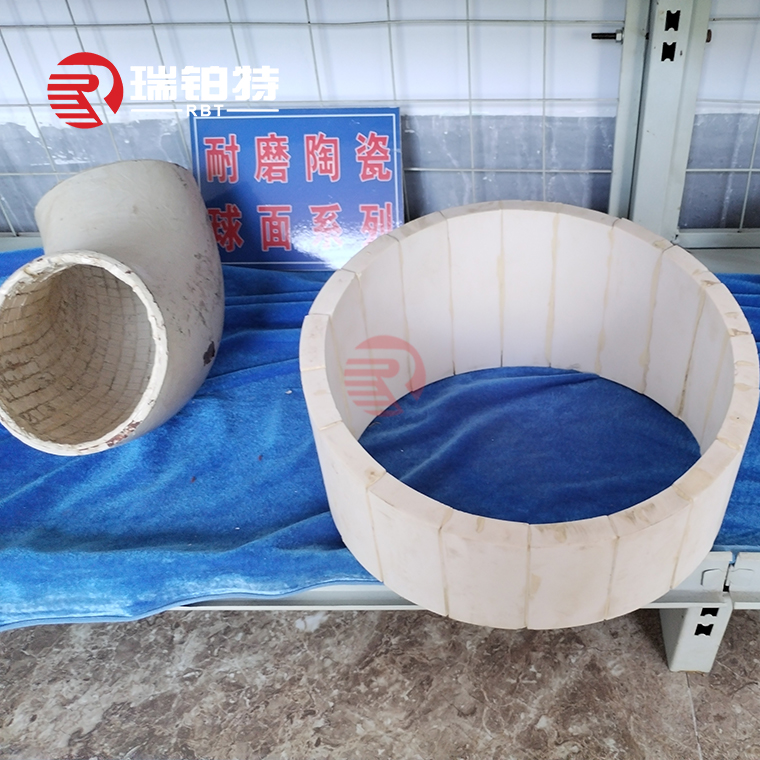
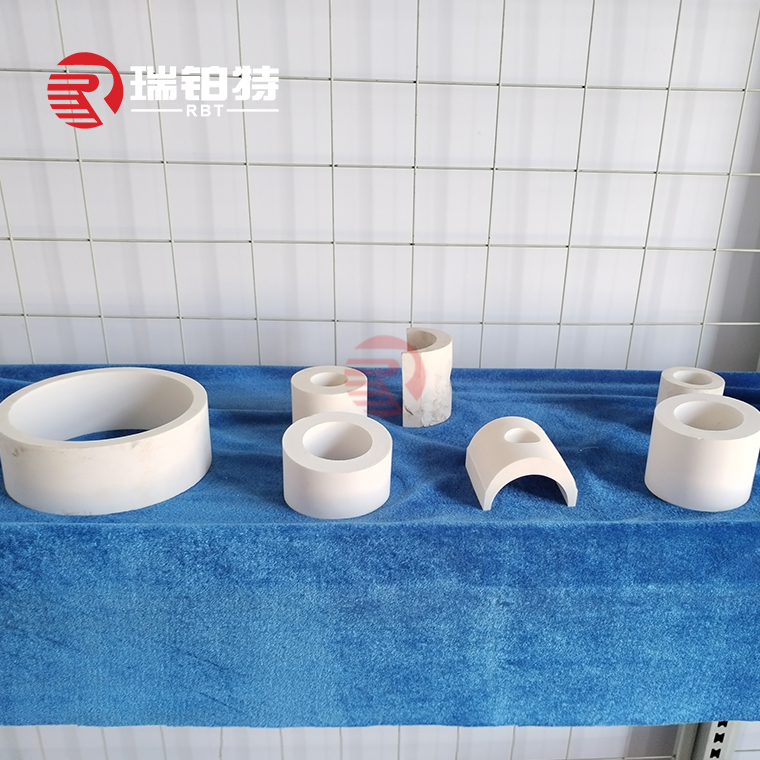
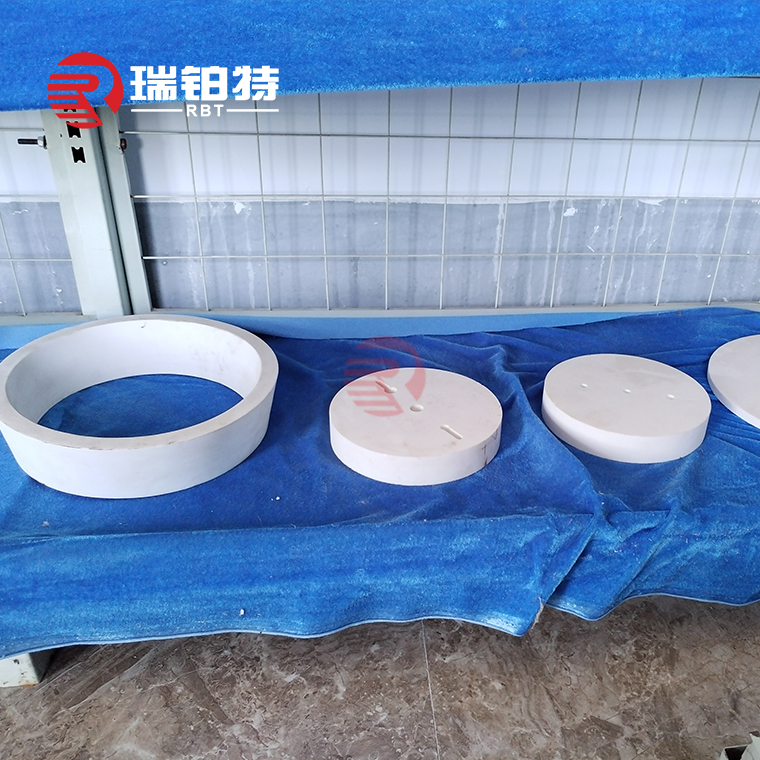
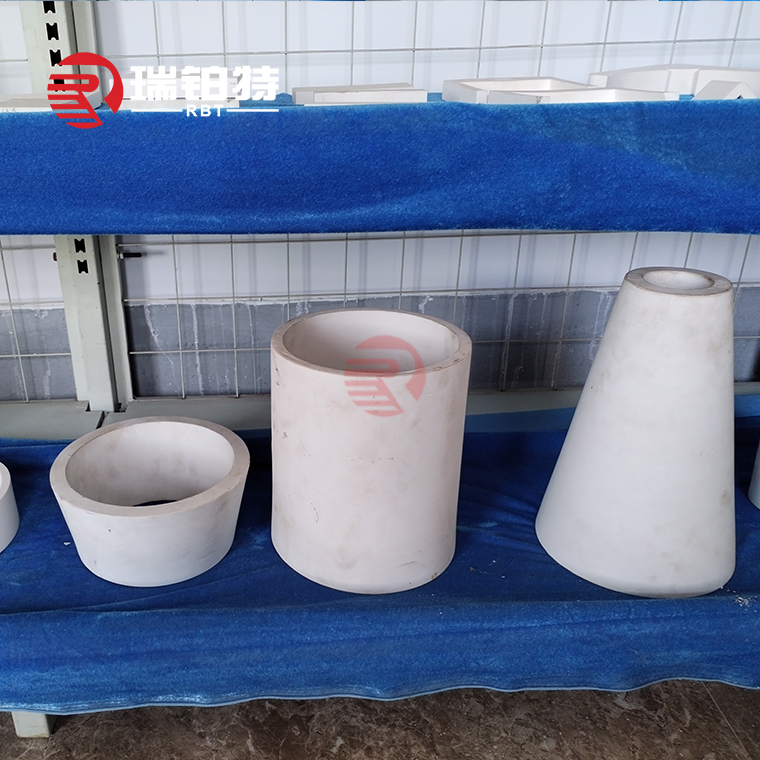
3. Wear-resistant ceramic composite pipe, full name ceramic lined composite steel pipe, is a pipe manufactured using a high-tech production process - self-propagating high-temperature clutch synthesis method.
Features:
High wear resistance: The Mohs hardness of the corundum ceramic lining can reach 9.0, which has extremely high wear resistance and is suitable for conveying abrasive media.
Corrosion resistance: Ceramic materials have good resistance to corrosive media such as acids, alkalis, and salts.
High temperature stability: The ceramic layer has high thermal stability and oxidation resistance, and is suitable for high temperature environments.
Lightweight and high strength: Among pipes of the same specifications and unit length, the wear-resistant ceramic composite pipe is lighter in weight, but has strong resistance to wear and fluid erosion.
Application:
Wear-resistant ceramic composite pipes are widely used in power, metallurgy, mining, coal, chemical and other industries for conveying abrasive granular materials and corrosive media such as sand, stone, coal powder, ash, aluminum liquid, etc. Its excellent wear resistance, corrosion resistance and heat resistance make it an ideal wear-resistant pipeline.
Manufacturing process
Centrifugal casting composite ceramic pipe: It is manufactured using "self-propagating high temperature synthesis-high-speed centrifugal technology". The process is simple and the cost is low. It is suitable for long-distance powder transportation.
Patch wear-resistant ceramic pipe: The alumina ceramic sheet is pasted on the inner wall of the pipe through high-temperature resistant strong adhesive. The manufacturing process is relatively simple and the cost is low.
Self-propagating composite pipe: By mixing ceramic powder and metal powder, it is sintered on the inner wall of the pipe using high-temperature synthesis and centrifugal methods. Integrally calcined ceramic pipe: The ceramic powder is sintered into a ceramic pipe according to the mold and then combined with the steel pipe.
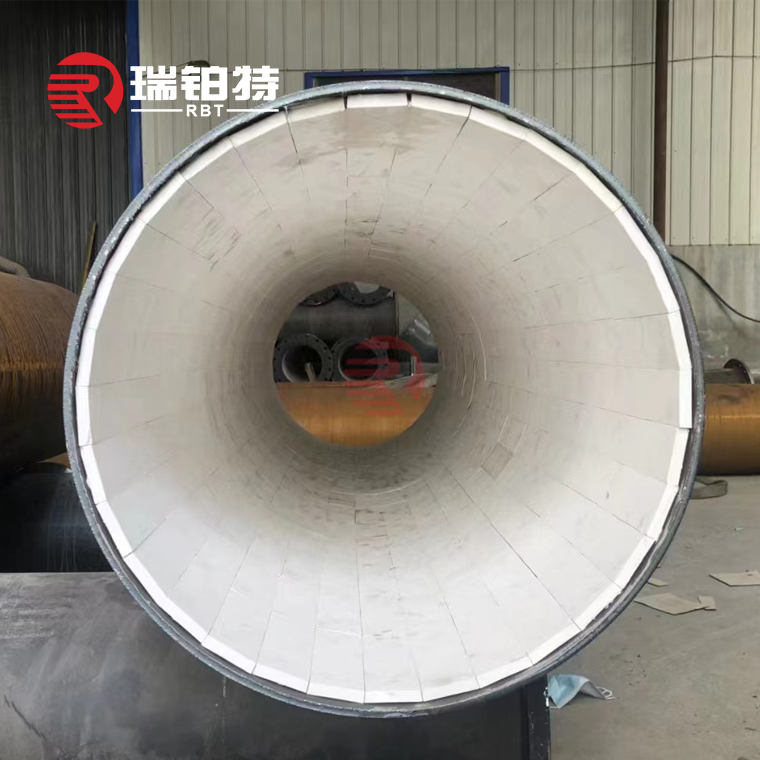
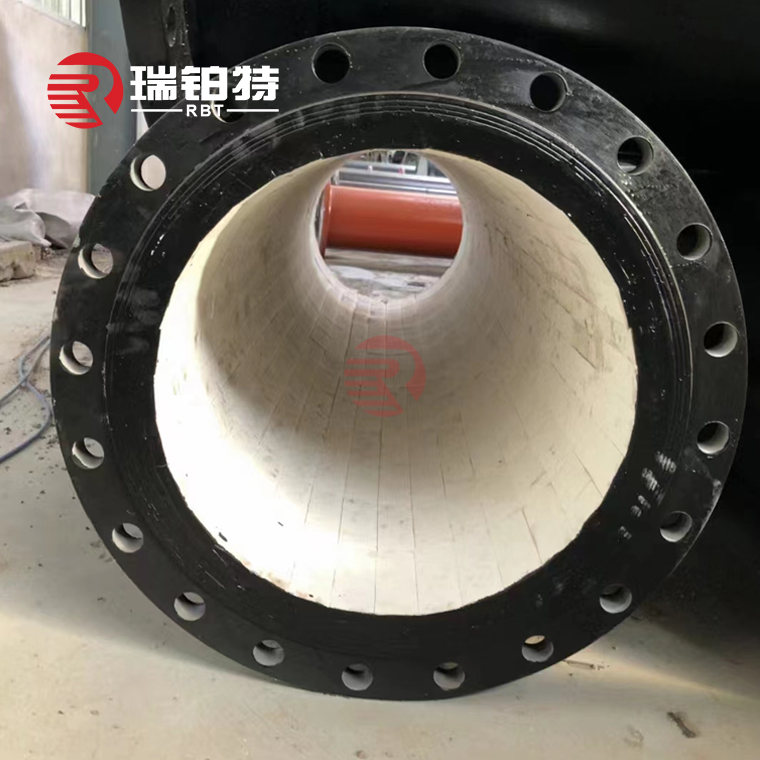
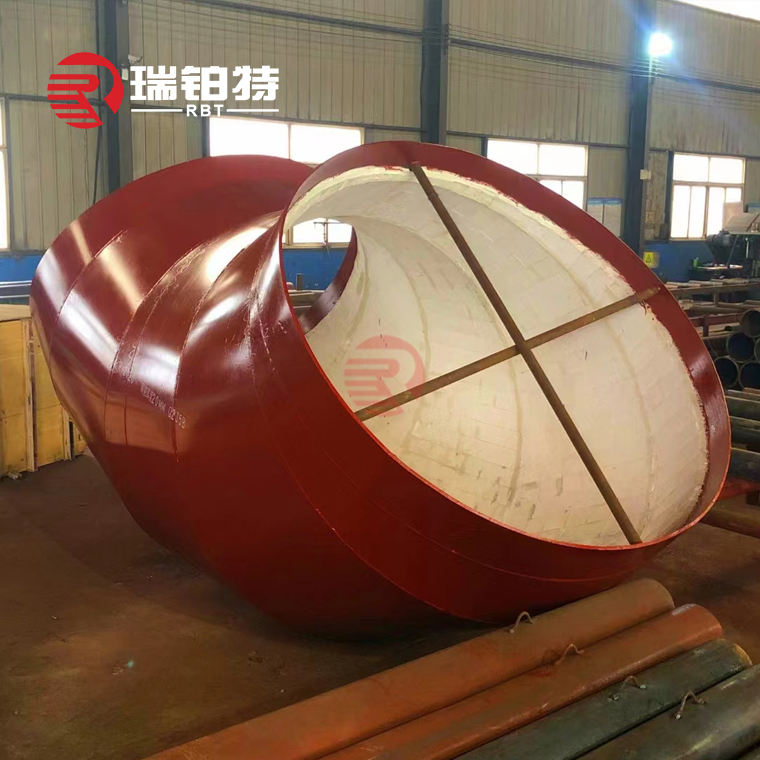
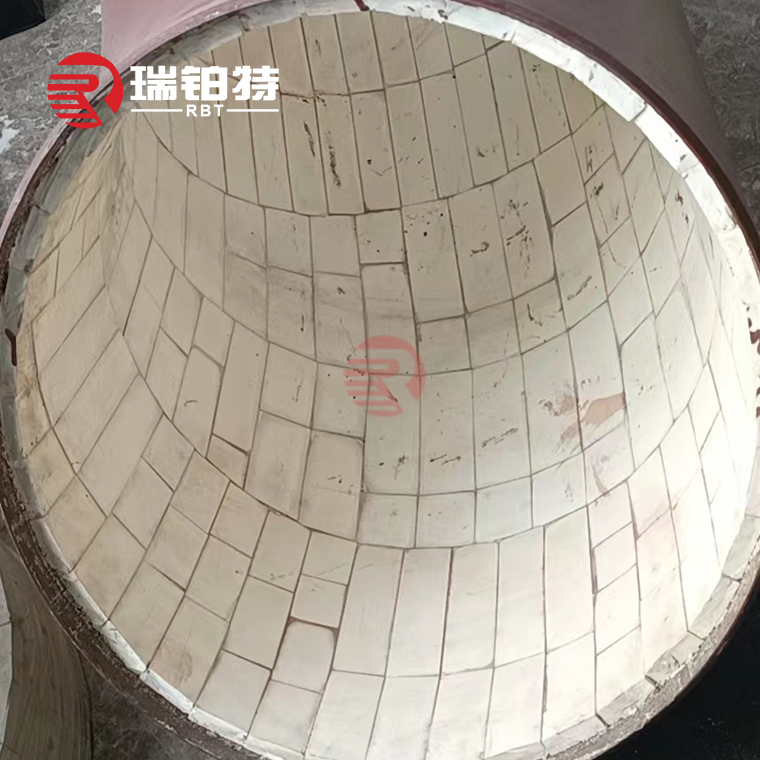
4. Two-in-one and three-in-one ceramic composite plates are a composite material that combines ceramic and rubber materials, with excellent wear resistance, corrosion resistance and impact resistance.
Manufacturing process
Two-in-one ceramic rubber composite plates: Through rubber vulcanization technology, high-hardness alumina ceramics are vulcanized and embedded in special rubber to form a ceramic rubber composite. This composite has good cushioning performance and can effectively cushion the impact of ore and other materials falling from high altitude.
Three-in-one wear-resistant ceramic composite plates: On the basis of two-in-one, a steel plate layer is added. Through rubber vulcanization technology, the ceramic rubber composite is vulcanized together with a steel plate with countersunk bolts to form a composite lining with a three-in-one structure. This structure ensures a close bond between ceramics, rubber and steel plates, while providing additional fixing effects.
Performance characteristics
Wear resistance: The ceramic layer has extremely high hardness, which can effectively resist wear and extend the service life of the equipment.
Impact resistance: The rubber layer has good elasticity and impact resistance, can absorb the impact and vibration generated during the operation of the equipment, and protect the ceramic layer from damage.
Corrosion resistance: Both ceramics and rubber have good corrosion resistance and can operate stably for a long time in harsh environments.
Lightweight: The lining plate in the three-in-one structure is more than 60% lighter than the wear-resistant steel plate, and it is very convenient to install and replace.
Application:
Mining: Used for wear-resistant parts of equipment such as ball mills, coal mills, bucket elevators, scraper conveyors, etc. to improve the operating efficiency and stability of the equipment.
Metallurgy: In various equipment in the metallurgical industry, wear-resistant ceramic composite plates can effectively resist the wear of high temperature, high pressure and corrosive materials.
Electricity: In the coal transportation system, dust removal equipment and other parts of the power industry, reduce equipment wear and reduce maintenance costs.
Chemical industry: In the reactors, storage tanks and other equipment in the chemical industry, resist the erosion of various chemical media and extend the service life of the equipment.
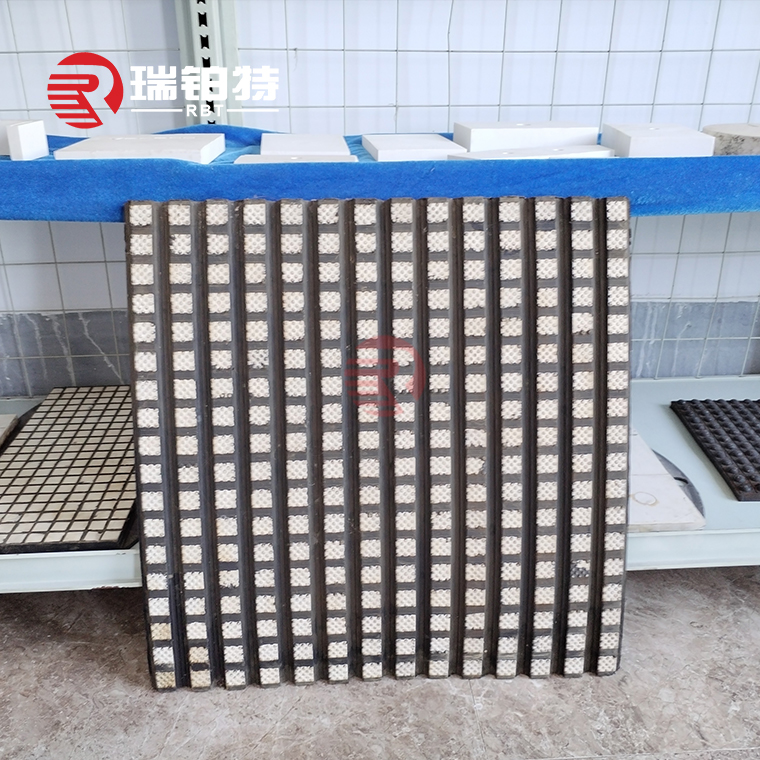
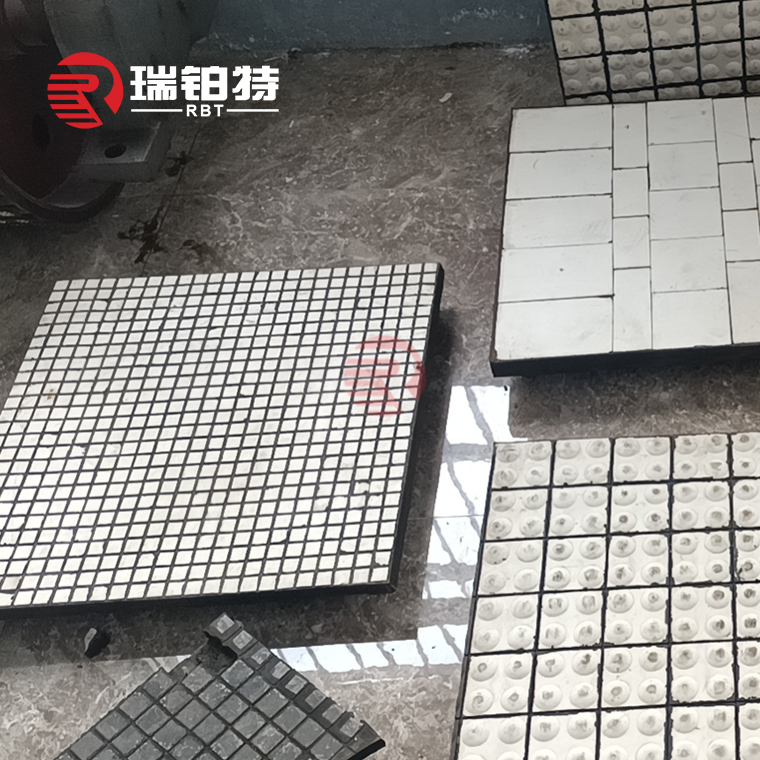
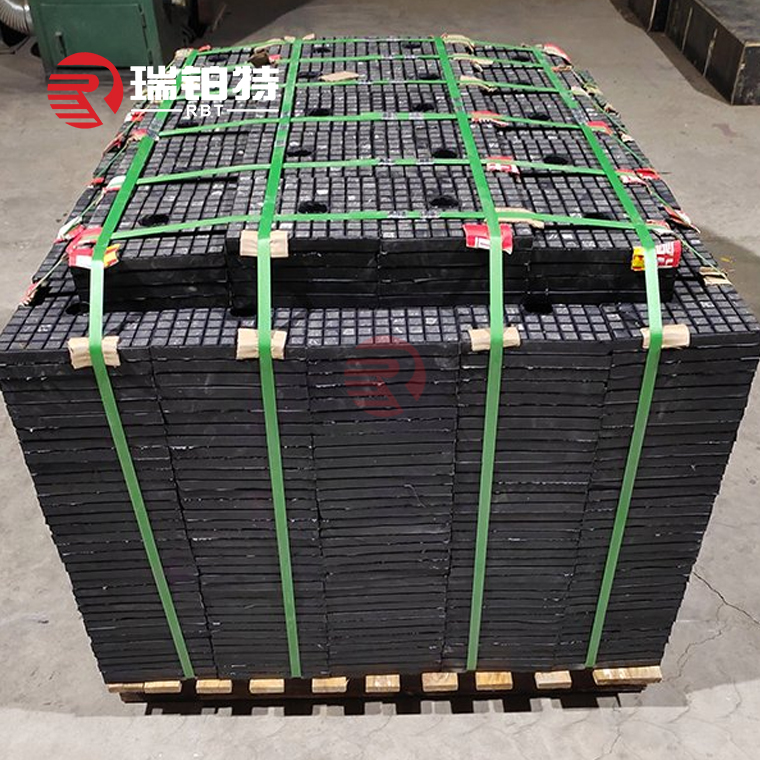
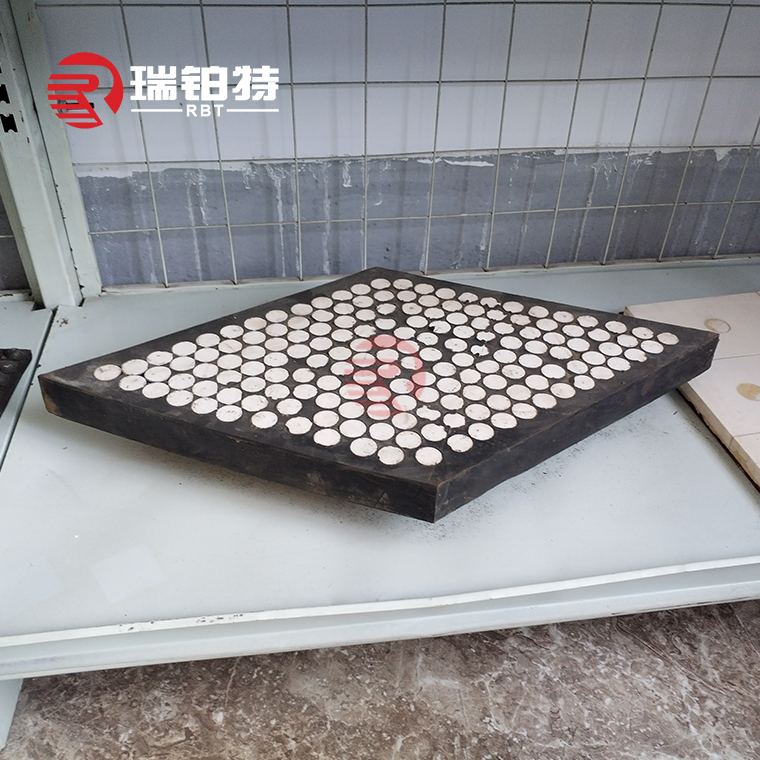
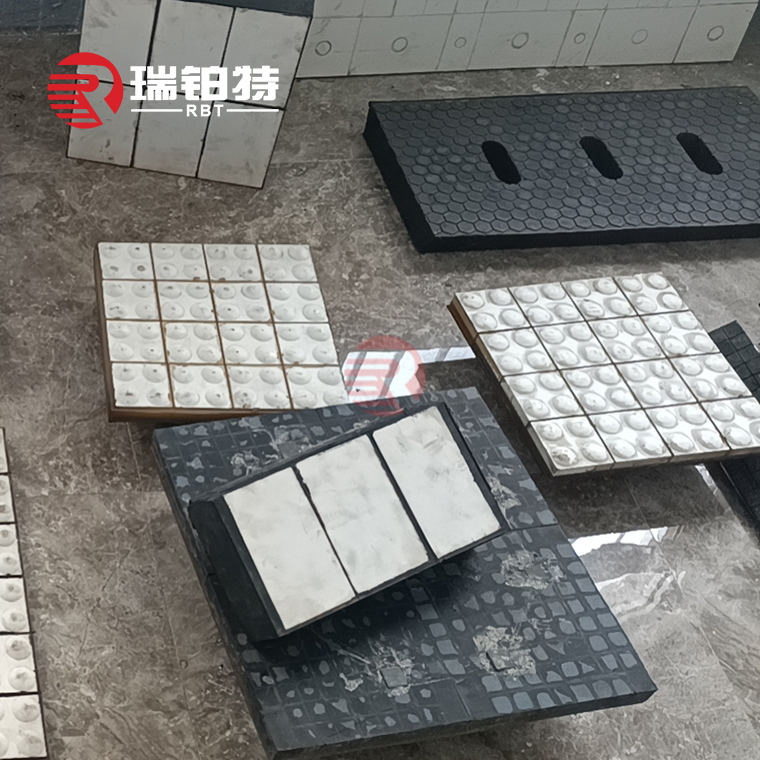
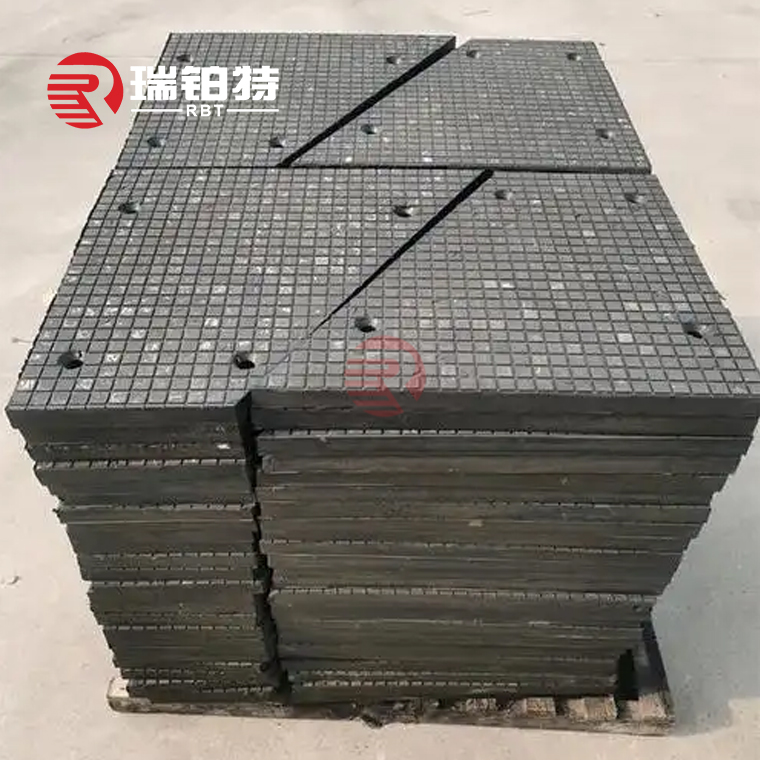
Product Index
Item
|
Al2O3 >92%
|
>95%
|
>99%
|
>99.5%
|
>99.7%
|
Color
|
White
|
White
|
White
|
Cream Color
|
Cream Color
|
Theoretical Density(g/cm3)
|
3.45
|
3.50
|
3.75
|
3.90
|
3.92
|
Bending Strength(Mpa)
|
340
|
300
|
330
|
390
|
390
|
Compressive Strength(Mpa)
|
3600
|
3400
|
2800
|
3900
|
3900
|
Elastic Modulus(Gpa)
|
350
|
350
|
370
|
390
|
390
|
Impact Resistance(Mpam1/2)
|
4.2
|
4
|
4.4
|
5.2
|
5.5
|
Weibull Coefficient(m)
|
11
|
10
|
10
|
12
|
12
|
Vickers Hardness(HV 0.5)
|
1700
|
1800
|
1800
|
2000
|
2000
|
Thermal Expansion Coefficient
|
5.0-8.3
|
5.0-8.3
|
5.1-8.3
|
5.5-8.4
|
5.5-8.5
|
Thermal Conductivity(W/mk)
|
18
|
24
|
25
|
28
|
30
|
Thermal Shock Stability
|
220
|
250
|
250
|
280
|
280
|
Maximum Operating Temperature℃
|
1500
|
1600
|
1600
|
1700
|
1700
|
20℃ Volume Resistance
|
>10^14
|
>10^14
|
>10^14
|
>10^15
|
>10^15
|
Dielectric Strength(kv/mm)
|
20
|
20
|
20
|
30
|
30
|
Dielectric Constant
|
10
|
10
|
10
|
10
|
10
|
Factory Show
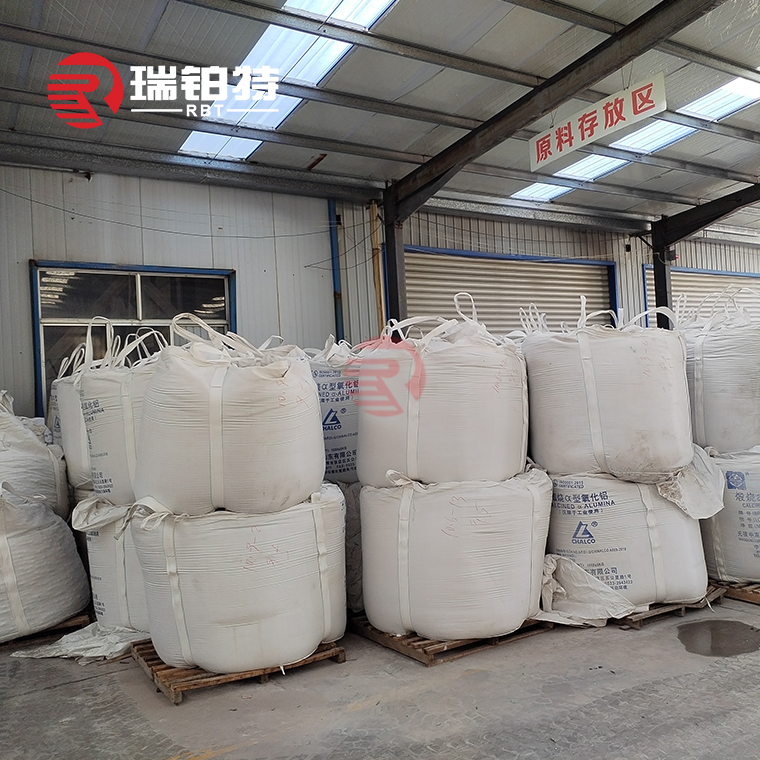
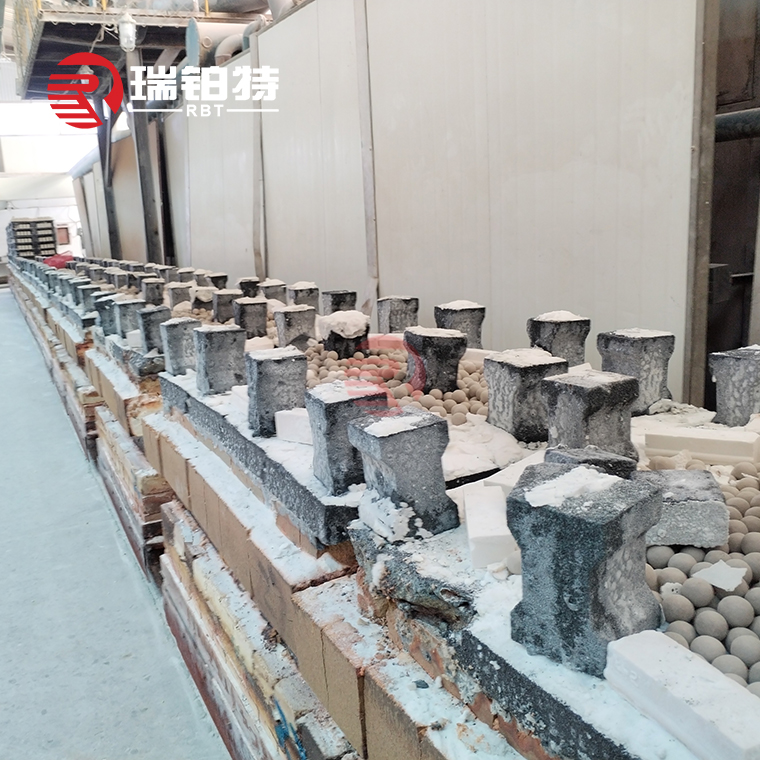
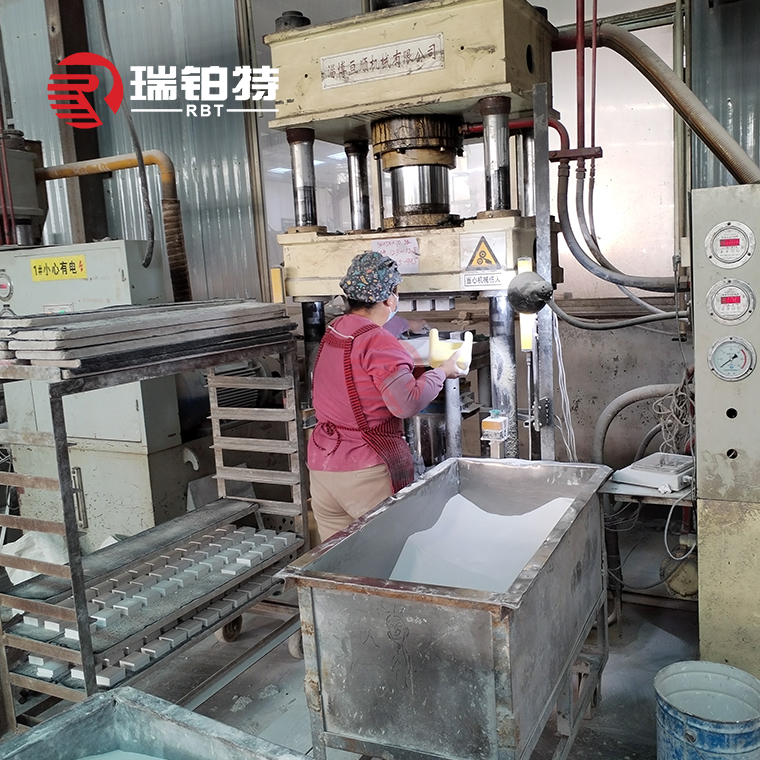
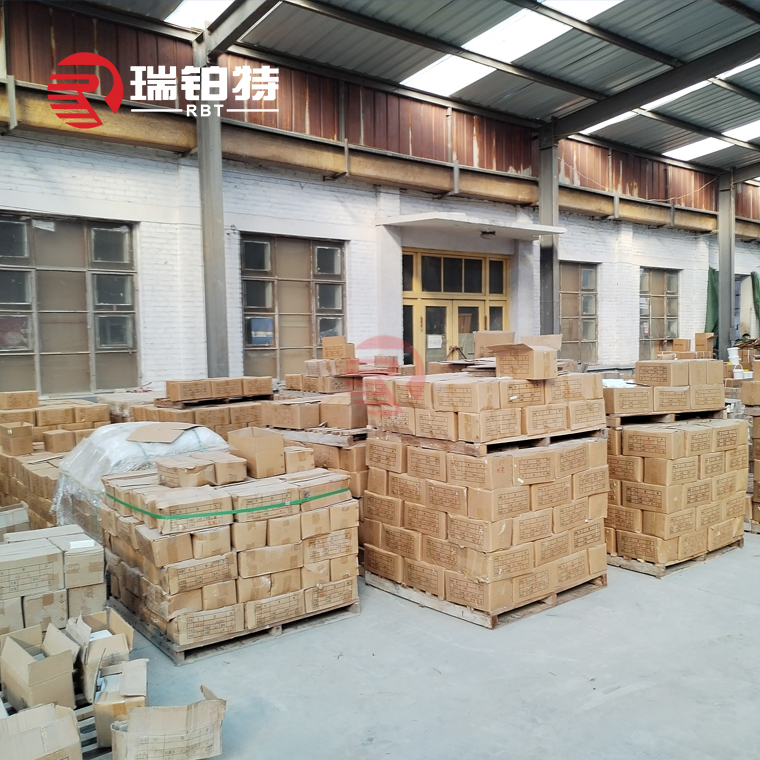
Company Profile
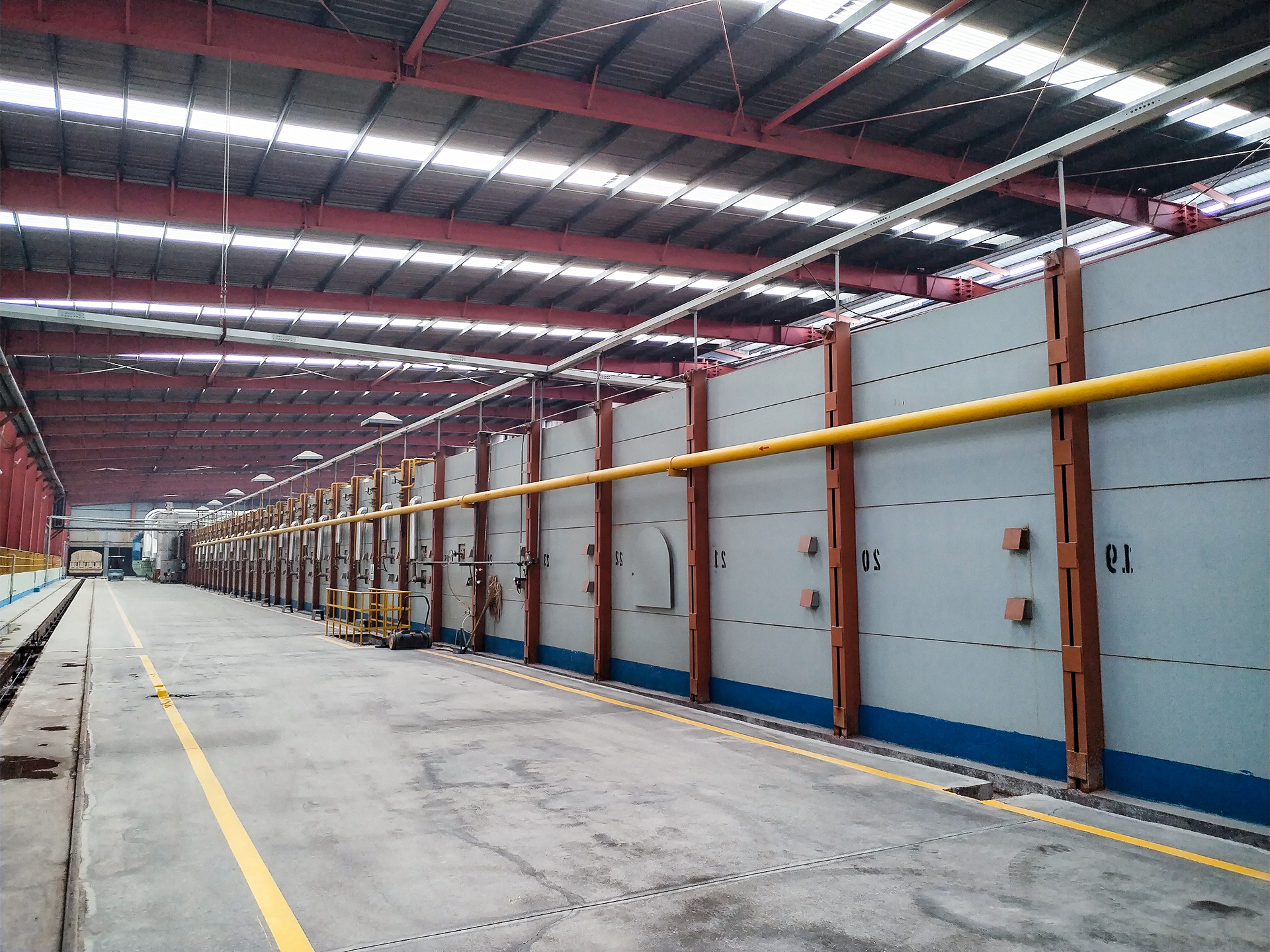
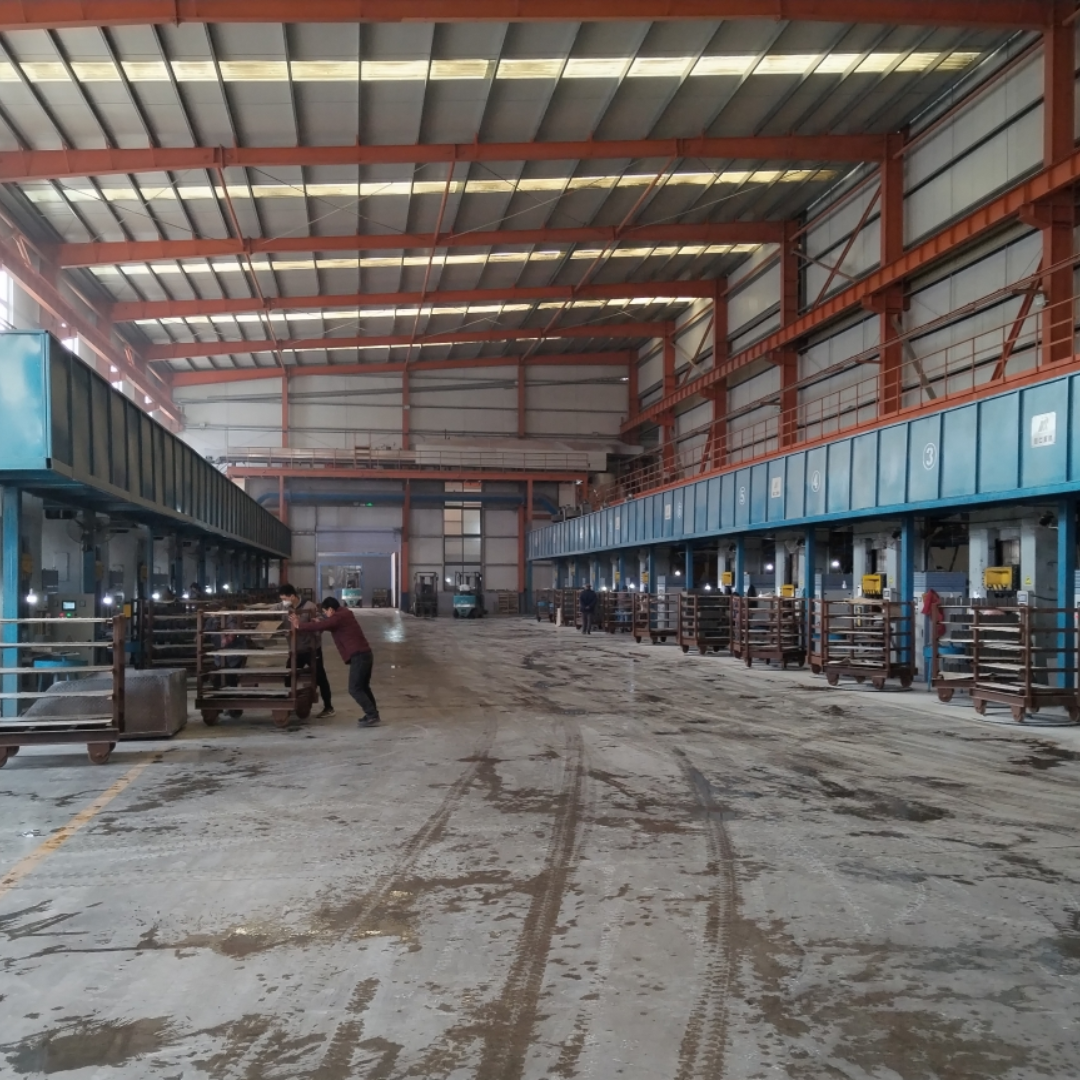
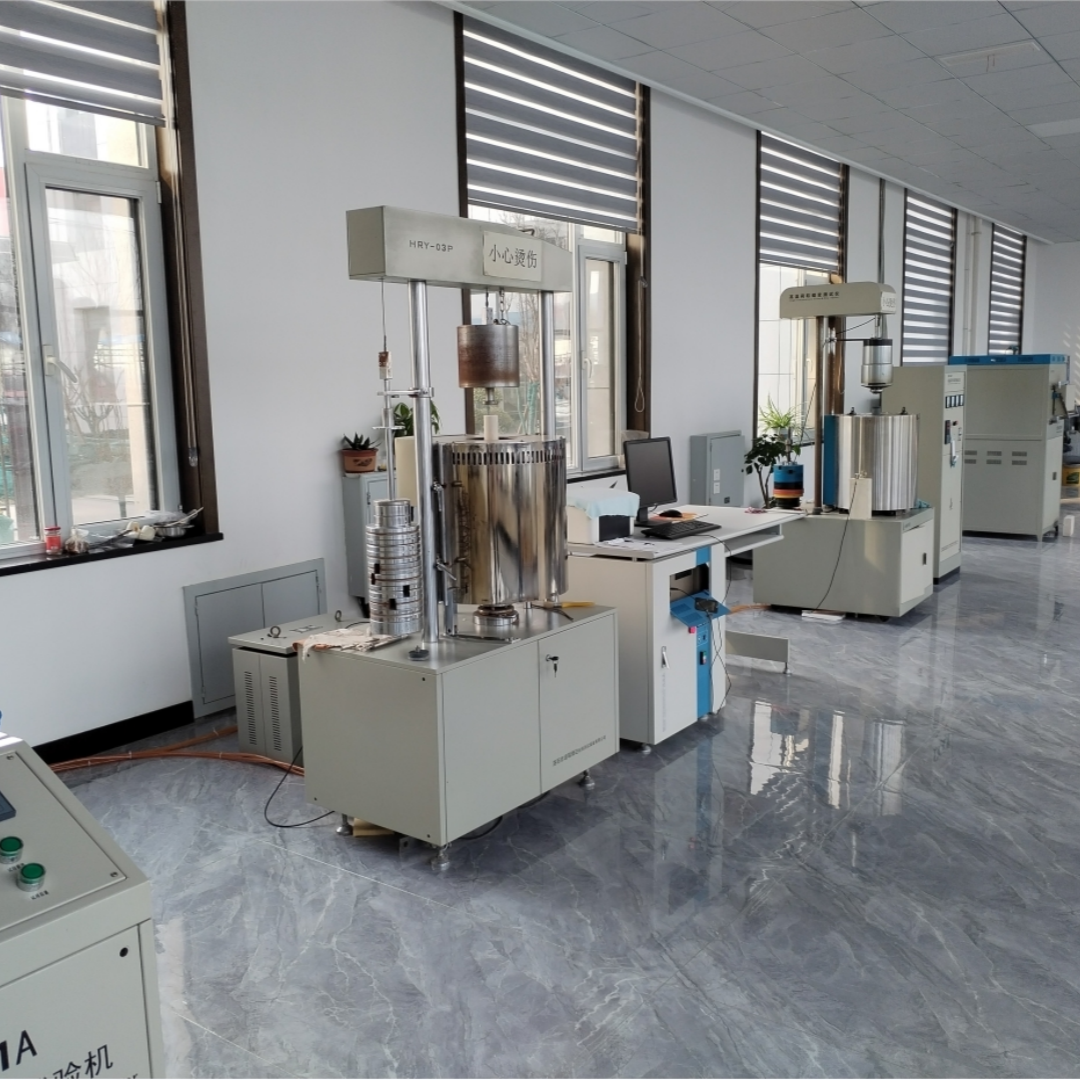
Shandong Robert New Material Co., Ltd. is located in Zibo City, Shandong Province, China, which is a refractory material production base. We are a modern enterprise that integrates the research and development, production, sales, kiln design and construction, technology, and export refractory materials. We have complete equipment, advanced technology, strong technical strength, excellent product quality, and good reputation. Our factory covers over 200 acres and an annual output of shaped refractory materials is approximately 30000 tons and unshaped refractory materials is 12000 tons.
Our main products of refractory materials include: alkaline refractory materials; aluminum silicon refractory materials; unshaped refractory materials; insulation thermal refractory materials; special refractory materials; functional refractory materials for continuous casting systems.
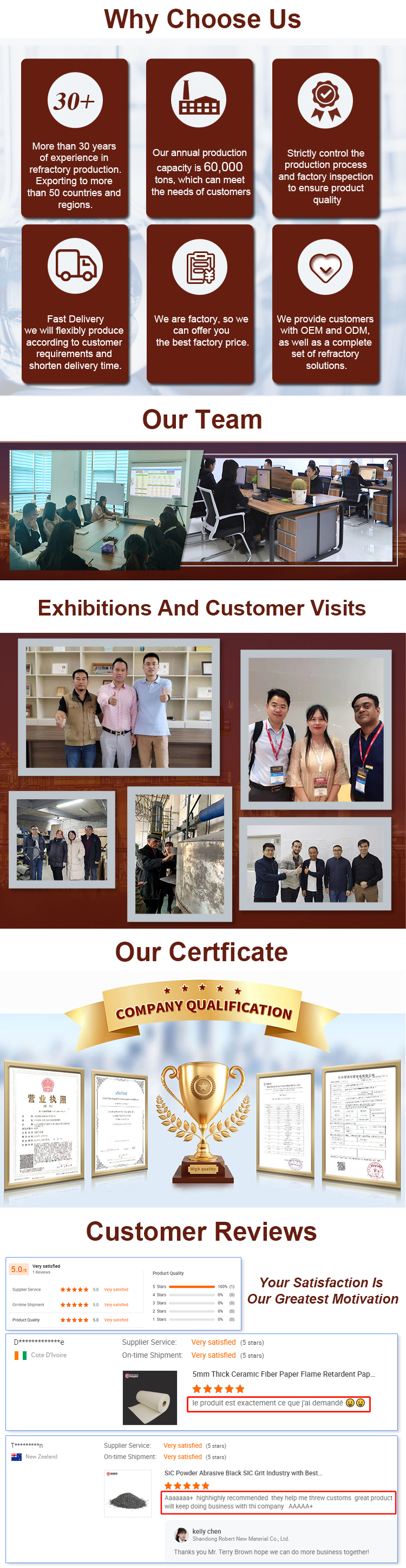
Frequently Asked Questions
Need help? Be sure to visit our support forums for answers to your questions!
We are a real manufacturer, our factory is specialized in producing refractory materials for more than 30 years. We promise to provide the best price, the best pre-sale and after-sale service.
For each production process, RBT has a complete QC system for chemical composition and physical properties. And we will test the goods, and the quality certificate will be shipped with the goods. If you have special requirements, we will try our best to accommodate them.
Depending on the quantity, our delivery time is different. But we promise to ship as soon as possible with guaranteed quality.
Of course, we provide free samples.
Yes, of course, you are welcome to visit RBT company and our products.
There is no limit, we can provide the best suggestion and solution according to your situation.
We have been making refractory materials for more than 30 years, we have strong technical support and rich experience, we can help customers design different kilns and provide one-stop service.