Black Silicon Carbide
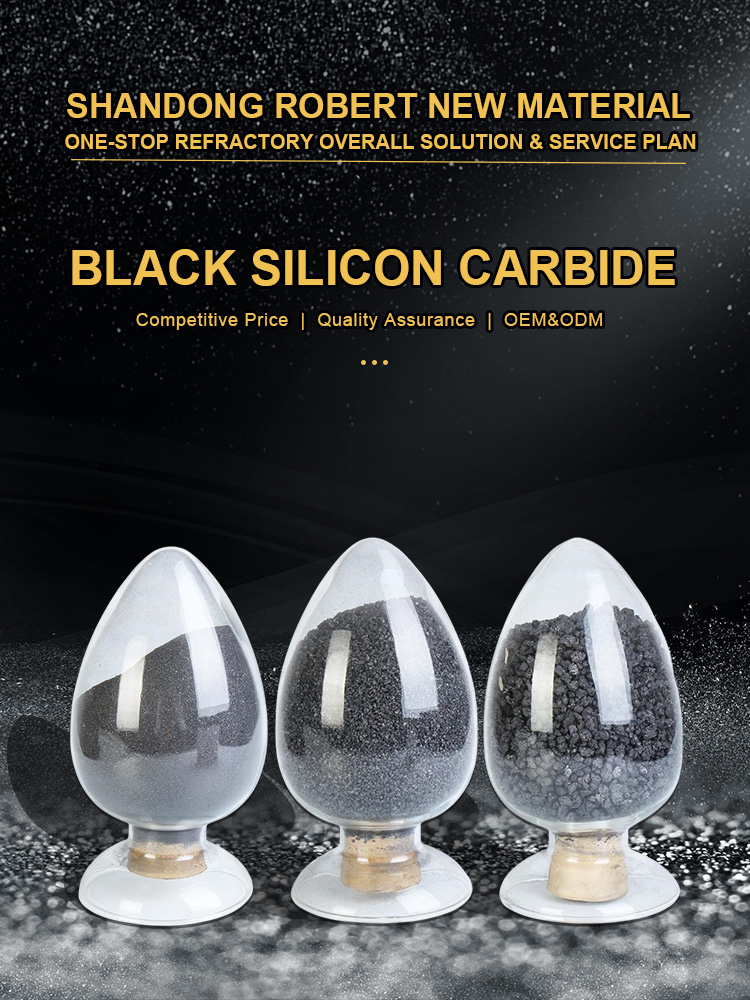
Product Information
Black Silicon Carbide(SiC) is an extremely hard (Mohs 9.1/ 2550 Knoop) man made mineral that possesses high thermal conductivity and high strength at elevated temperatures (at 1000°C, SiC is 7.5 times stronger than Al203 ). SiC has a modulus of elasticity of 410 GPa, with no decrease in strength up to 1600°C, and it does not melt at normal pressures but instead dissociates at 2600°C.
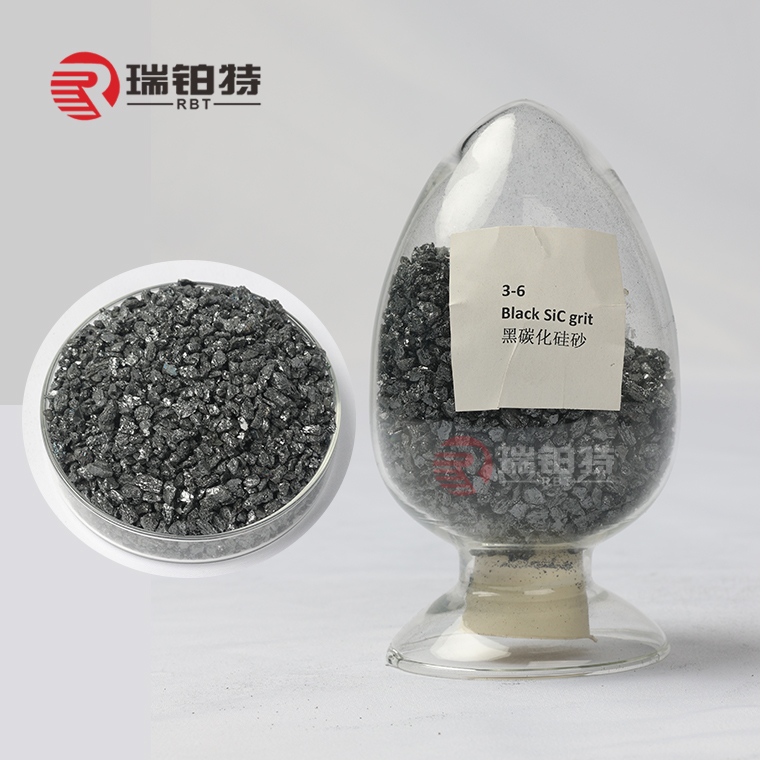
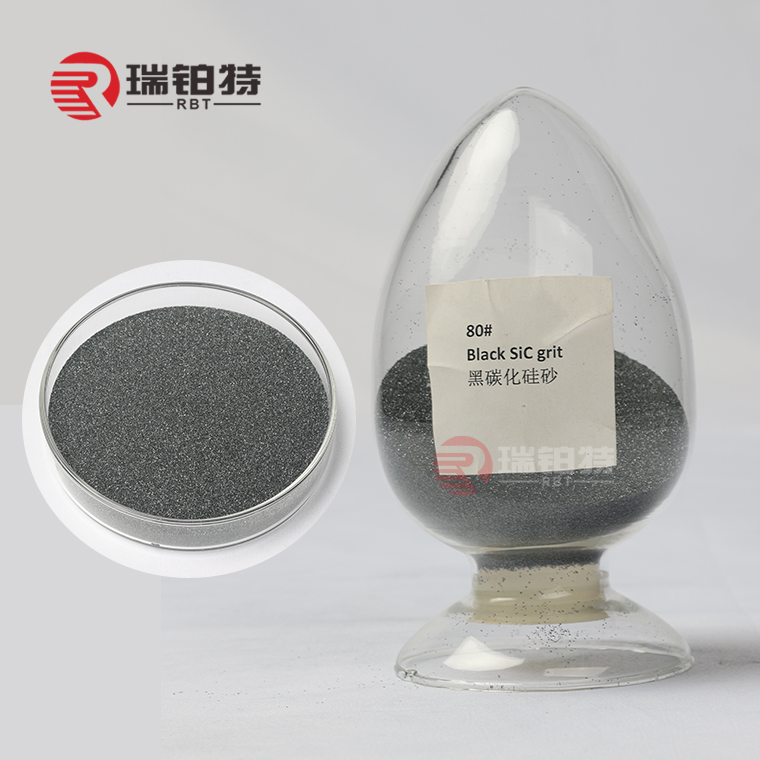
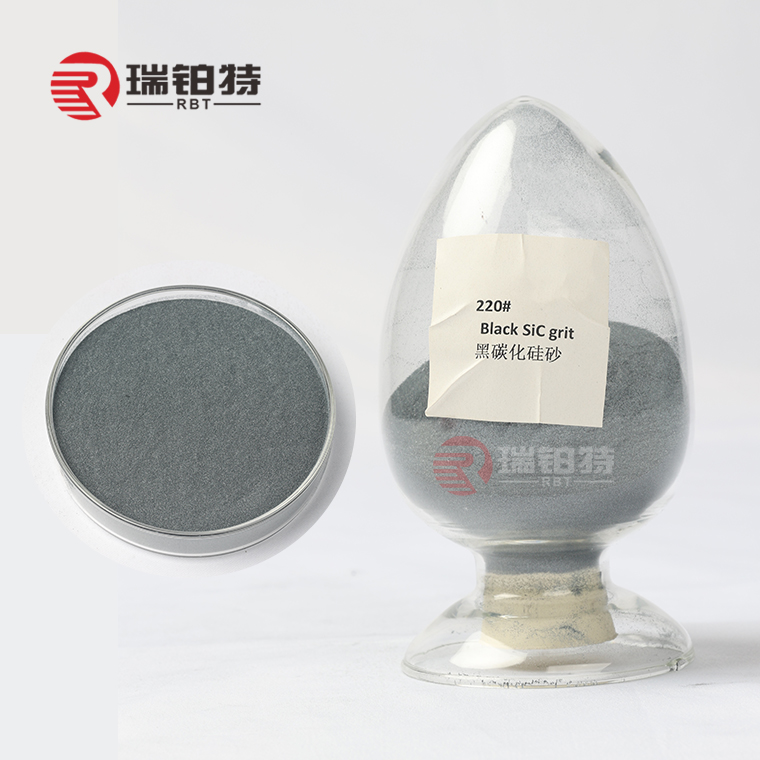
Grit Size Comparison Chart
Grit No. |
China GB2477-83 |
Japan JISR 6001-87 |
U.S.A ANSI(76) |
欧洲磨料协FEPA(84) |
国际ISO(86) |
4 |
5600-4750 |
|
5600-4750 |
5600-4750 |
5600-4750 |
5 |
4750-4000 |
|
4750-4000 |
4750-4000 |
4750-4000 |
6 |
4000-3350 |
|
4000-3350 |
4000-3350 |
4000-3350 |
7 |
3350-2800 |
|
3350-2800 |
3350-2800 |
3350-2800 |
8 |
2800-2360 |
2800-2360 |
2800-2360 |
2800-2360 |
2800-2360 |
10 |
2360-2000 |
2360-2000 |
2360-2000 |
2360-2000 |
2360-2000 |
12 |
2000-1700 |
2000-1700 |
2000-1700 |
2000-1700 |
2000-1700 |
14 |
1700-1400 |
1700-1400 |
1700-1400 |
1700-1400 |
1700-1400 |
16 |
1400-1180 |
1400-1180 |
1400-1180 |
1400-1180 |
1400-1180 |
20 |
1180-1000 |
1180-1100 |
1180-1000 |
1180-1000 |
1180-1000 |
22 |
1000-850 |
- |
- |
1000-850 |
1000-850 |
24 |
850-710 |
850-710 |
850-710 |
850-710 |
850-710 |
30 |
710-600 |
710-600 |
710-600 |
710-600 |
710-600 |
36 |
600-500 |
600-500 |
600-500 |
600-500 |
600-500 |
40 |
500-425 |
- |
- |
500-425 |
500-425 |
46 |
425-355 |
425-355 |
425-355 |
425-355 |
425-355 |
54 |
355-300 |
355-300 |
355-297 |
355-300 |
355-300 |
60 |
300-250 |
300-250 |
297-250 |
300-250 |
300-250 |
70 |
250-212 |
250-212 |
250-212 |
250-212 |
250-212 |
80 |
212-180 |
212-180 |
212-180 |
212-180 |
212-180 |
90 |
180-150 |
180-150 |
180-150 |
180-150 |
180-150 |
100 |
150-125 |
150-125 |
150-125 |
150-125 |
150-125 |
120 |
125-106 |
125-106 |
125-106 |
125-106 |
125-106 |
150 |
106-75 |
106-75 |
106-75 |
106-75 |
106-75 |
180 |
90-63 |
90-63 |
90-63 |
90-63 |
90-63 |
220 |
75-53 |
75-53 |
75-53 |
75-53 |
75-53 |
240 |
75-53 |
- |
75-53 |
- |
Details Images
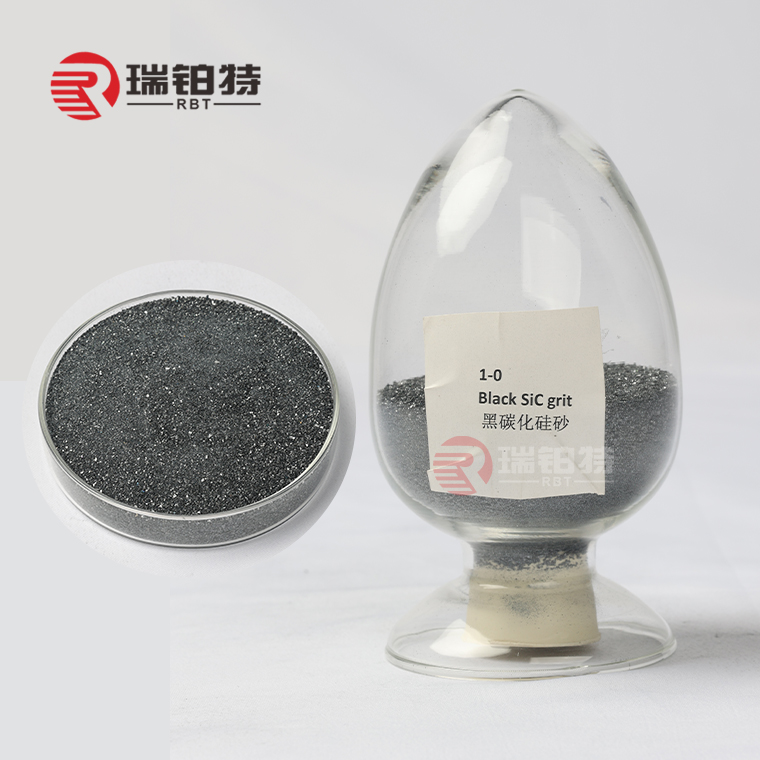
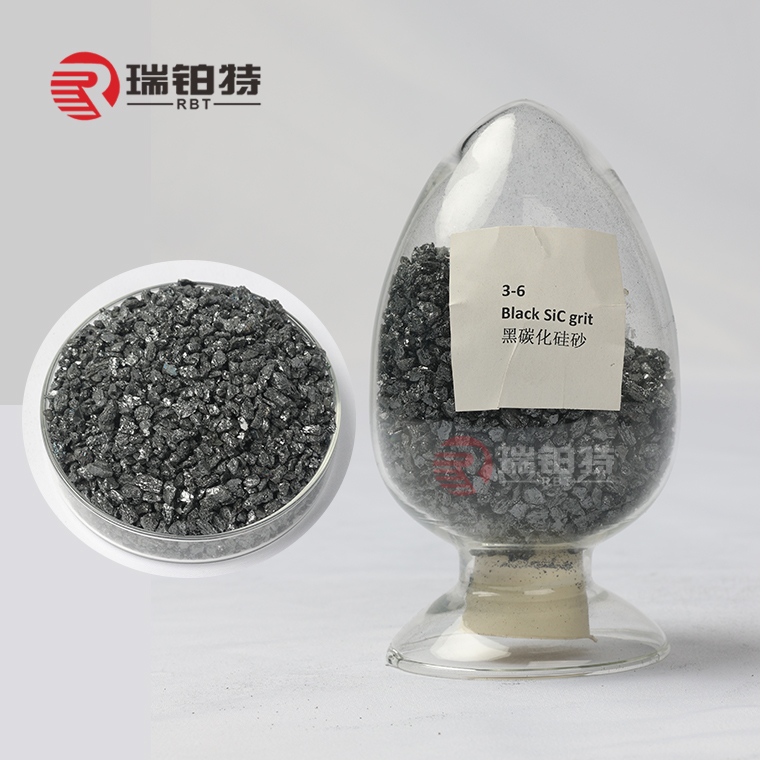
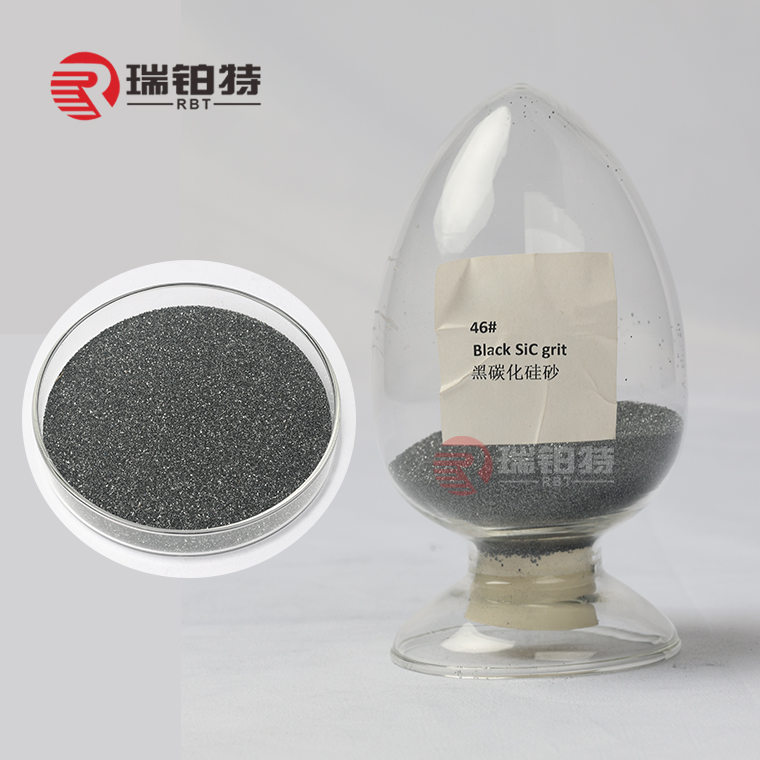
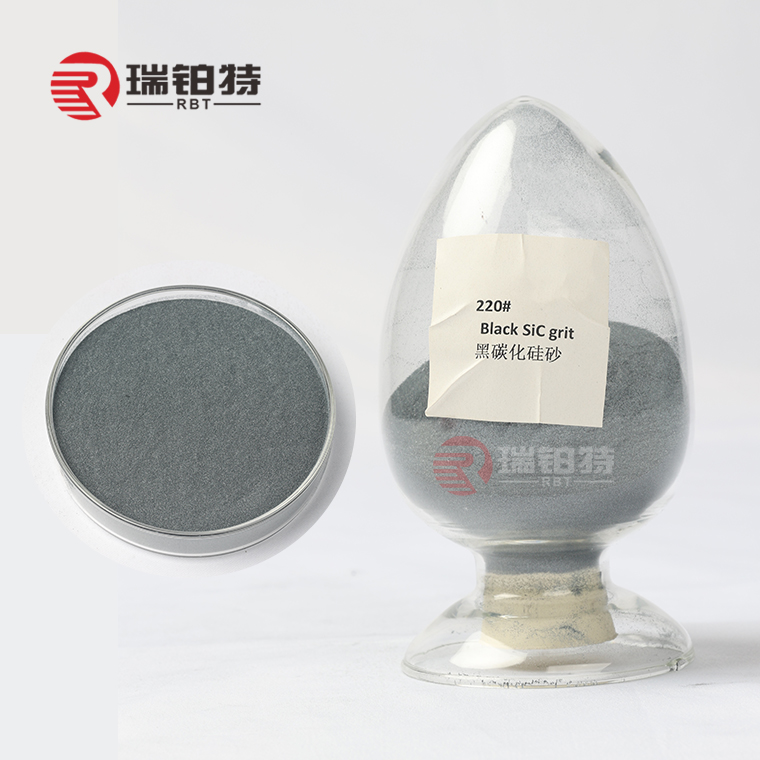
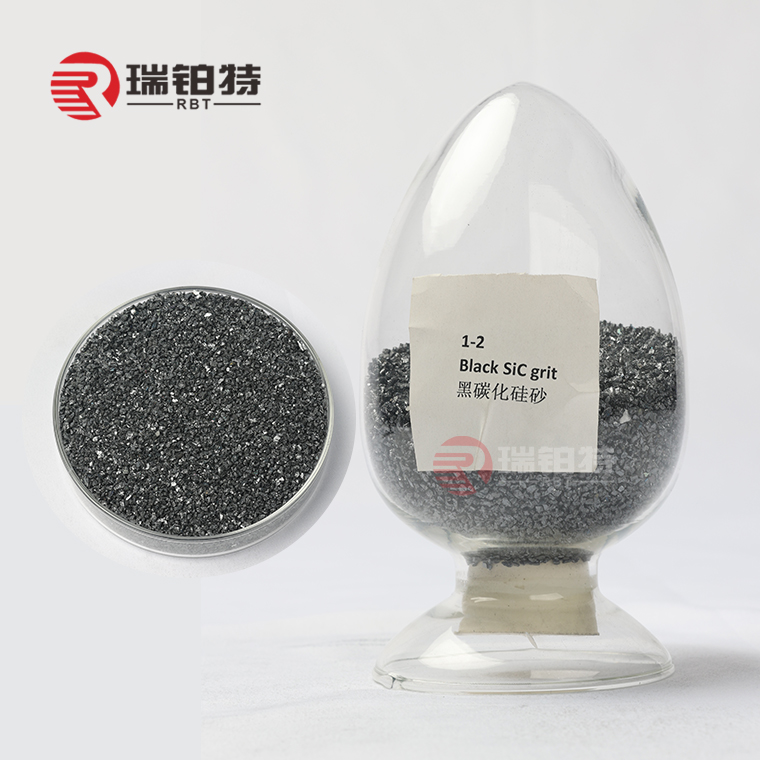
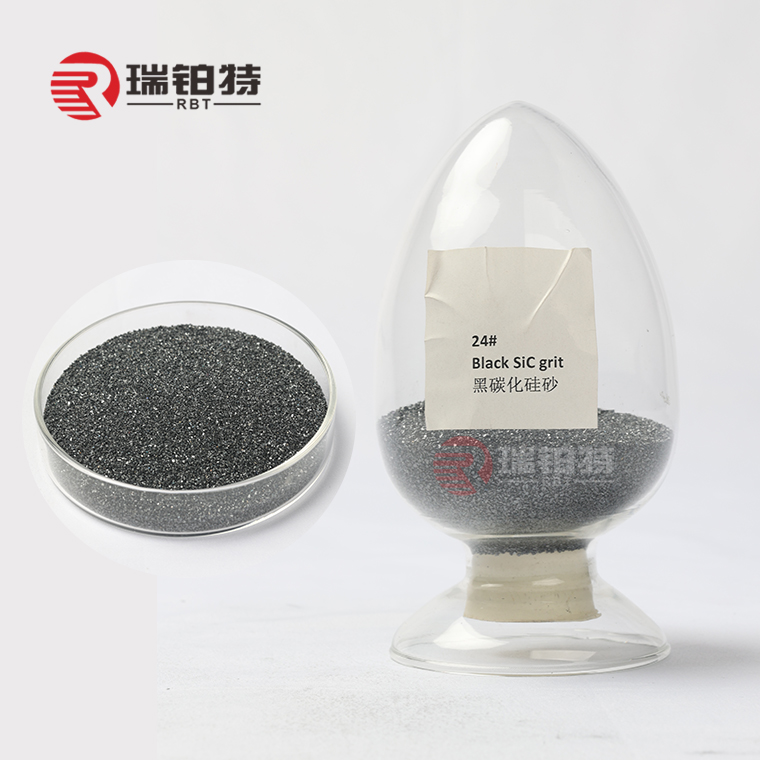
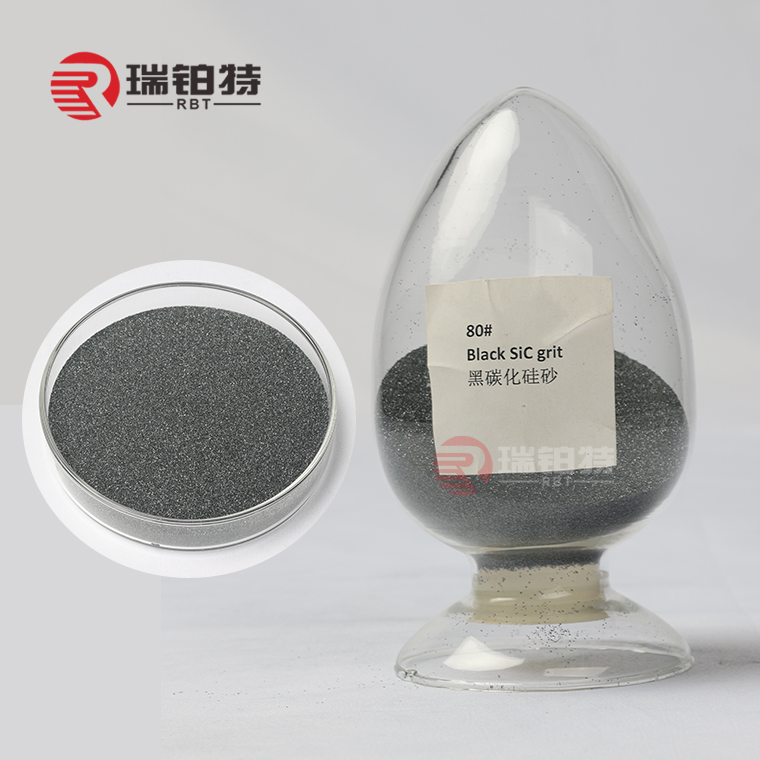
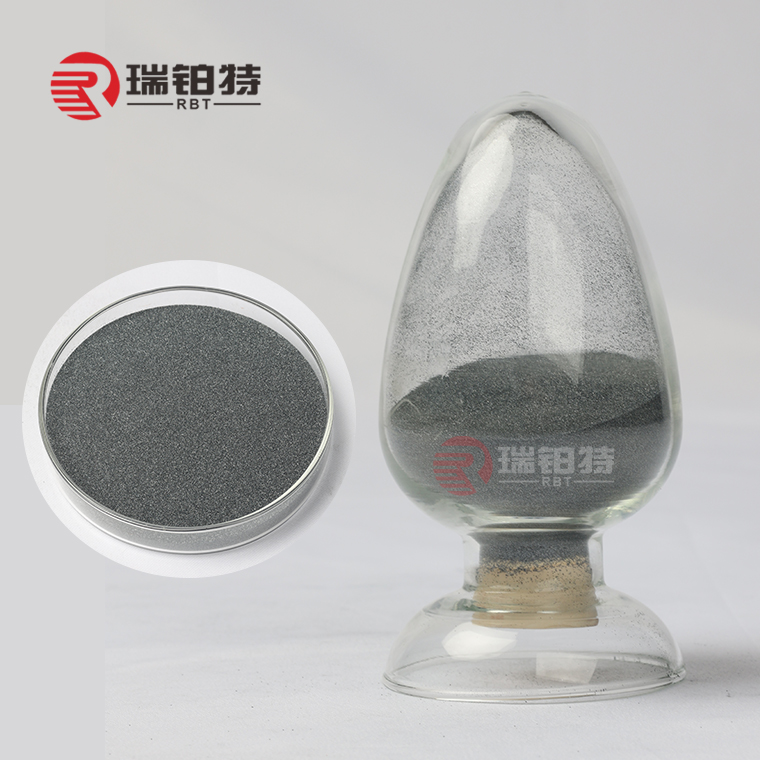
Product Index
Grit Size
|
Chemical Composition% (By Weight)
|
||
SIC
|
F·C
|
Fe2O3
|
|
12#-90#
|
≥98.50
|
≤0.20
|
≤0.60
|
100#-180#
|
≥98.00
|
≤0.30
|
≤0.80
|
220#-240#
|
≥97.00
|
≤0.30
|
≤1.20
|
W63-W20
|
≥96.00
|
≤0.40
|
≤1.50
|
W14-W5
|
≥93.00
|
≤0.40
|
≤1.70
|
Application
Abrasives and Grinding Tools: Due to its high hardness and certain toughness, black silicon carbide sand is widely used in the grinding and polishing of optical glass, cemented carbide, titanium alloy, bearing steel, and sharpening of high-speed steel tools. It is also suitable for cutting and grinding materials with low tensile strength, such as slicing of single crystal silicon and polycrystalline silicon rods, grinding of single crystal silicon wafers, etc.
Refractory Materials: In the metallurgical industry, black silicon carbide sand is often used as the lining, bottom and patch of high-temperature furnaces to ensure the normal operation of metallurgical equipment. It is also made into refractory materials, such as high-temperature furnace components and supports, which are resistant to thermal shock, small in size, light in weight and high in strength, and have good energy-saving effects.
Chemical Uses: In the chemical industry, black silicon carbide sand is used to manufacture corrosion-resistant chemical equipment, pipelines and valves to ensure the safe operation of equipment under corrosive media and high temperature conditions. In addition, it can also be used as a purifier for smelting steel, that is, a deoxidizer for steelmaking and a cast iron structure improver.
Electronics Industry: In the electronics industry, black silicon carbide sand is used to manufacture semiconductor materials and electronic components, such as high-power electronic devices, integrated circuit substrates, etc., to ensure the high performance and stability of electronic equipment.
Other Uses: Black silicon carbide sand is also used to make functional ceramics, electric heating elements, high-temperature semiconductor materials, far-infrared boards, lightning arrester valve materials, etc. It is also used to make non-stick pan coatings, wear-resistant coatings, anti-corrosion coatings, etc.
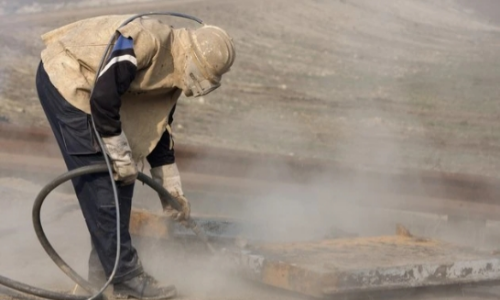
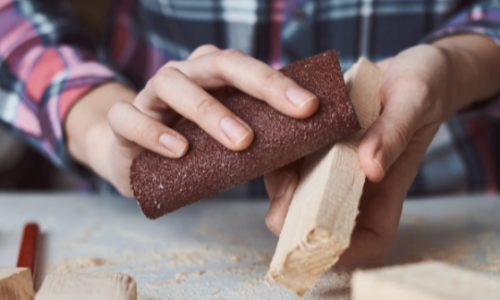
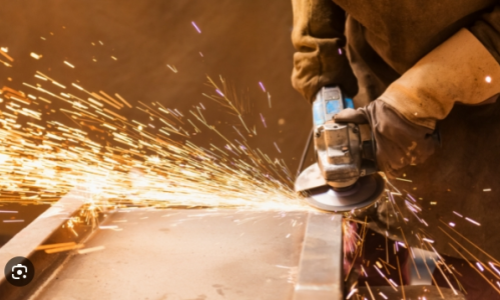
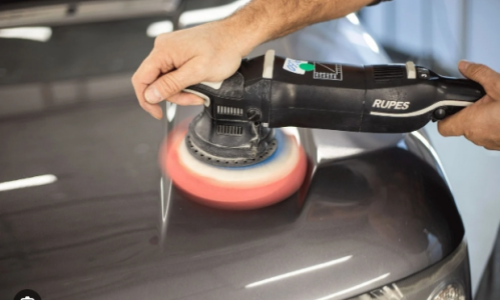
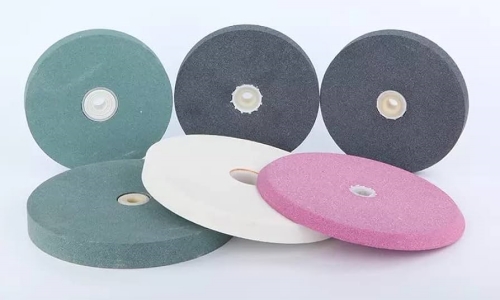
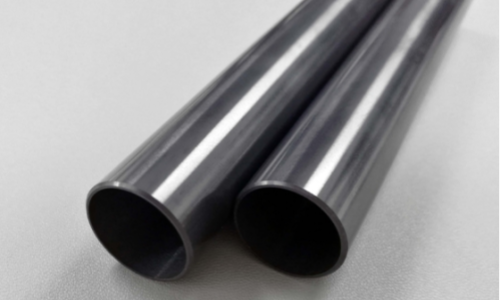
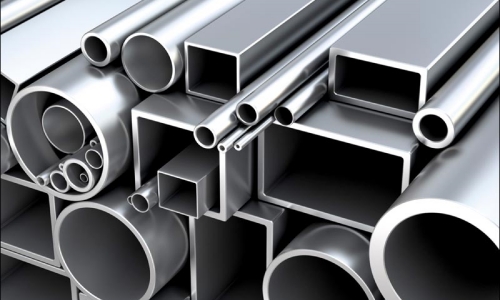
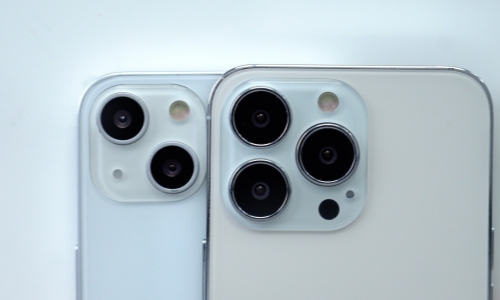
Package&Warehouse
Package
|
25KG Bag
|
1000KG Bag
|
Quantity
|
24-25 Tons
|
24 Tons
|
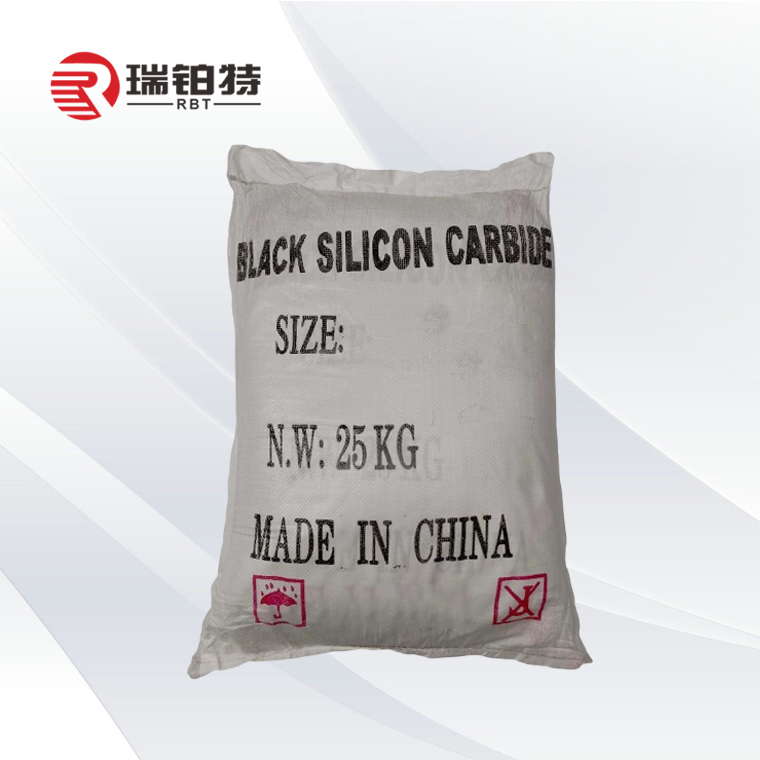
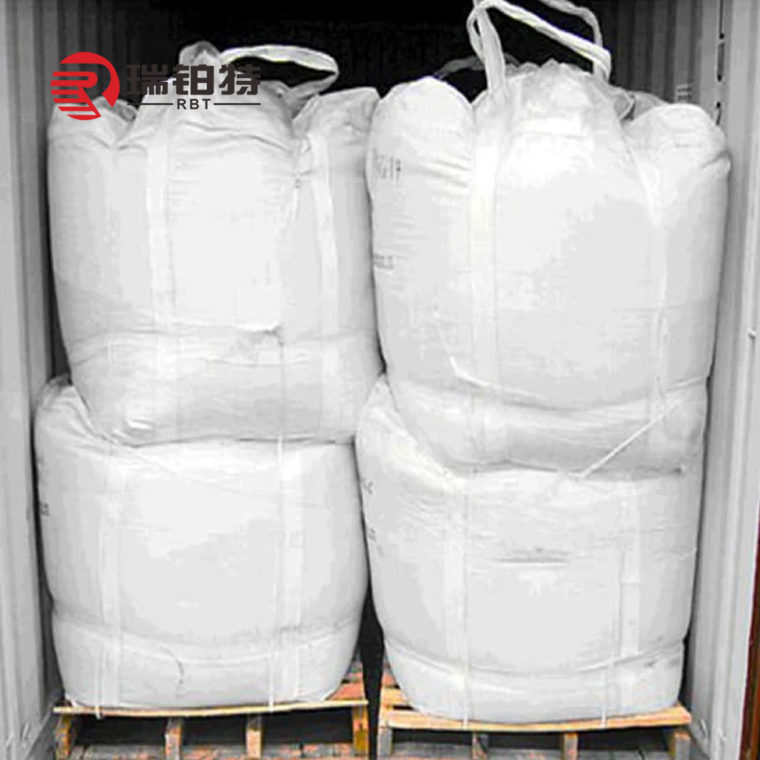
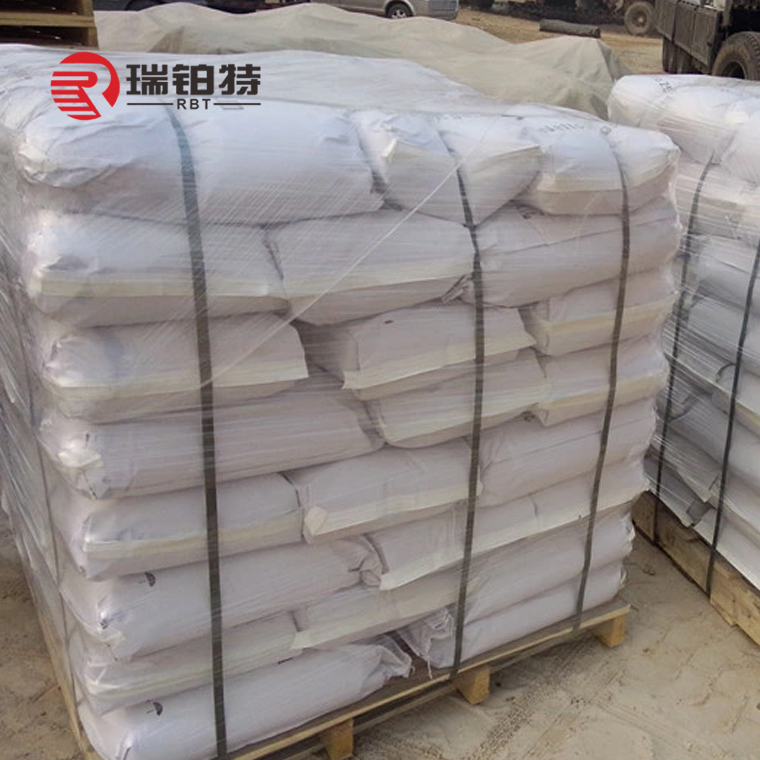
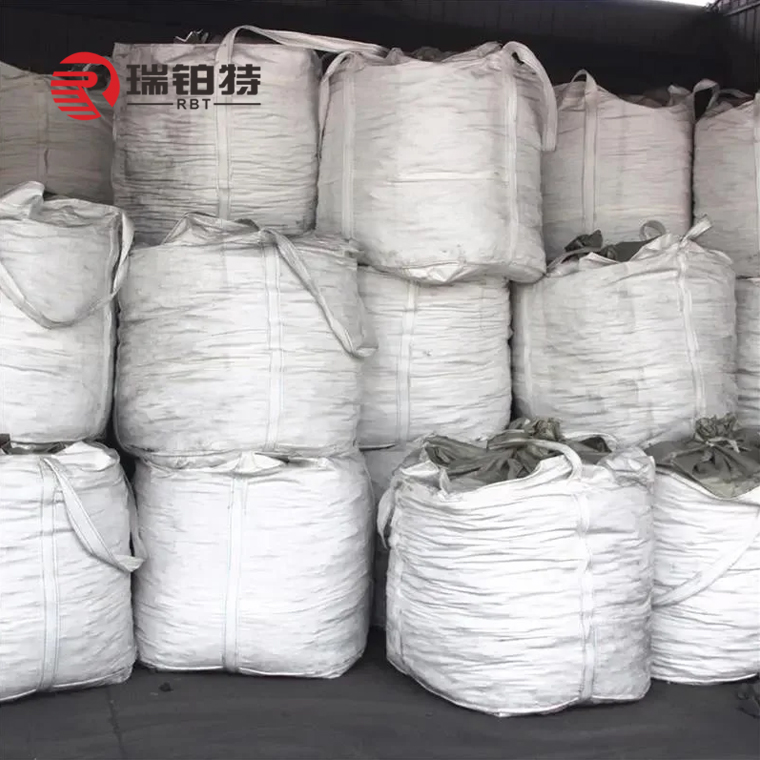
Company Profile
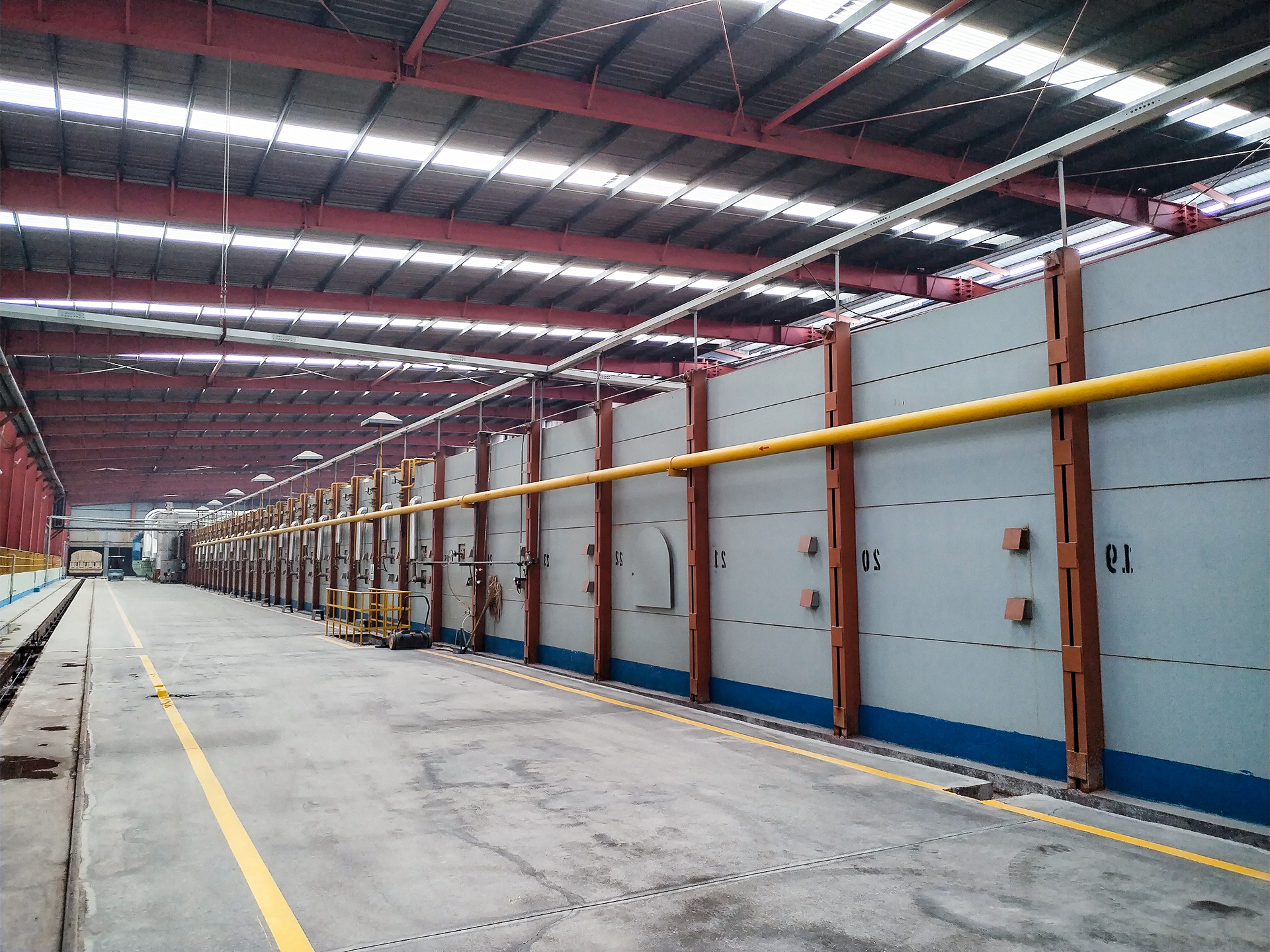
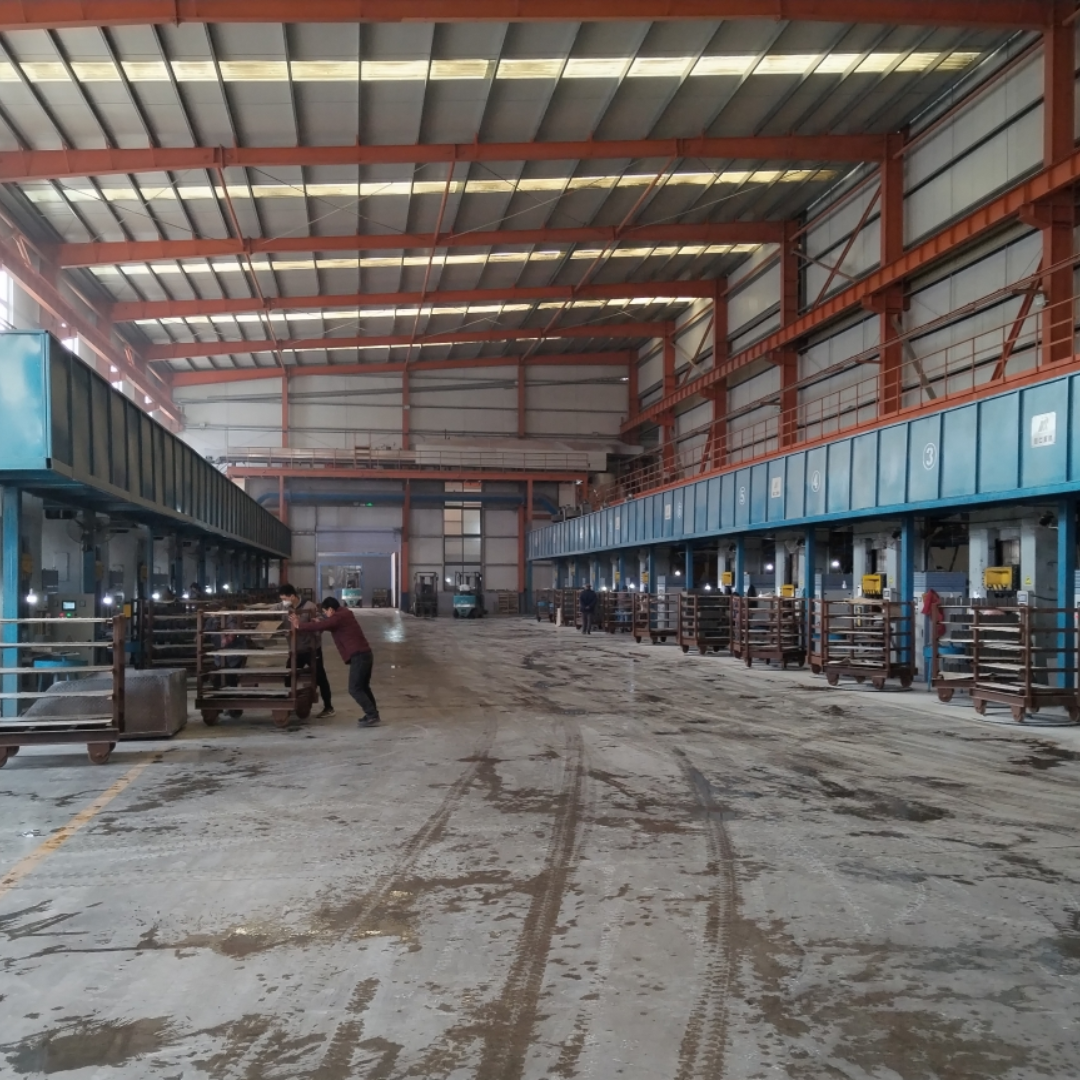
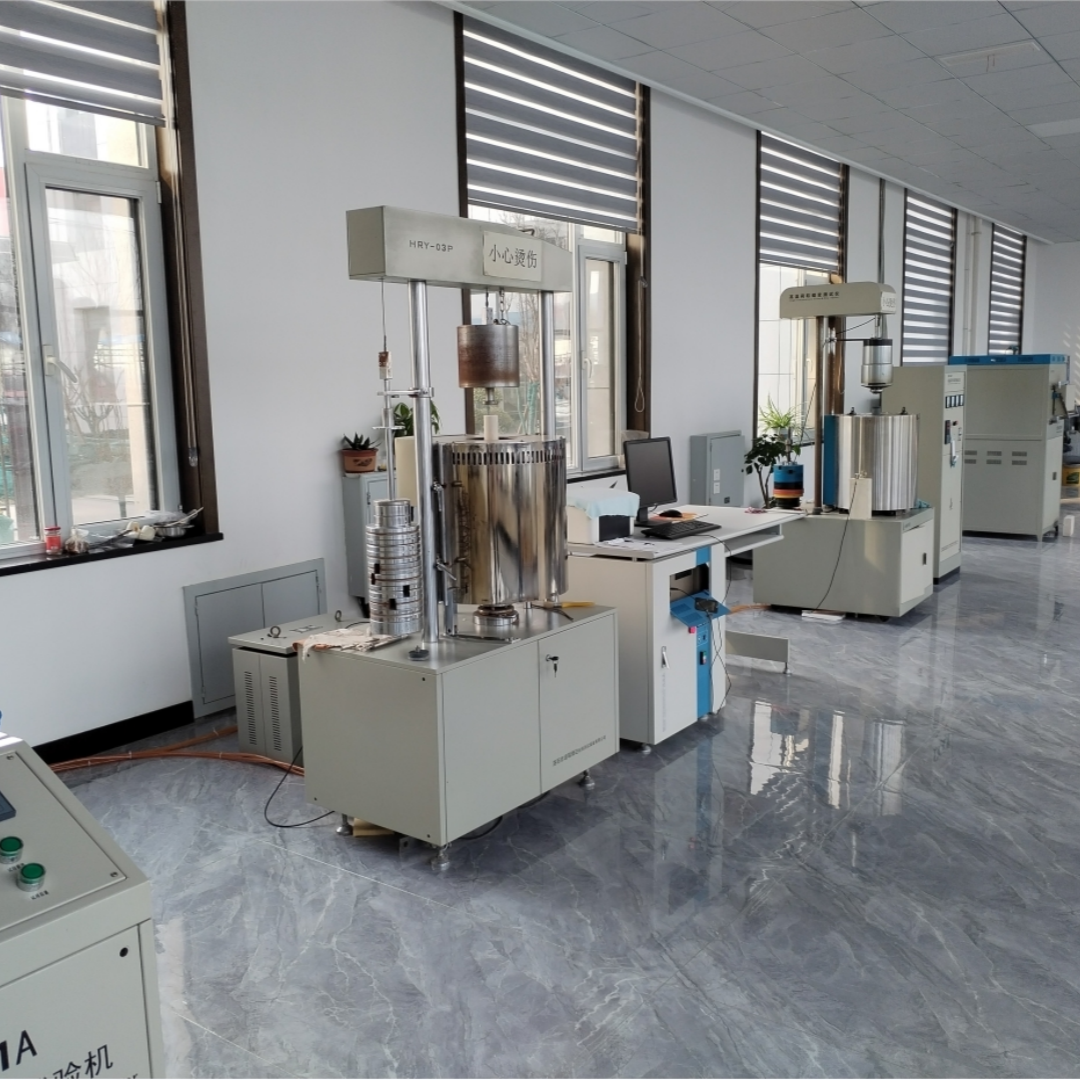
Shandong Robert New Material Co., Ltd. is located in Zibo City, Shandong Province, China, which is a refractory material production base. We are a modern enterprise that integrates the research and development, production, sales, kiln design and construction, technology, and export refractory materials. We have complete equipment, advanced technology, strong technical strength, excellent product quality, and good reputation. Our factory covers over 200 acres and an annual output of shaped refractory materials is approximately 30000 tons and unshaped refractory materials is 12000 tons.
Our main products of refractory materials include: alkaline refractory materials; aluminum silicon refractory materials; unshaped refractory materials; insulation thermal refractory materials; special refractory materials; functional refractory materials for continuous casting systems.
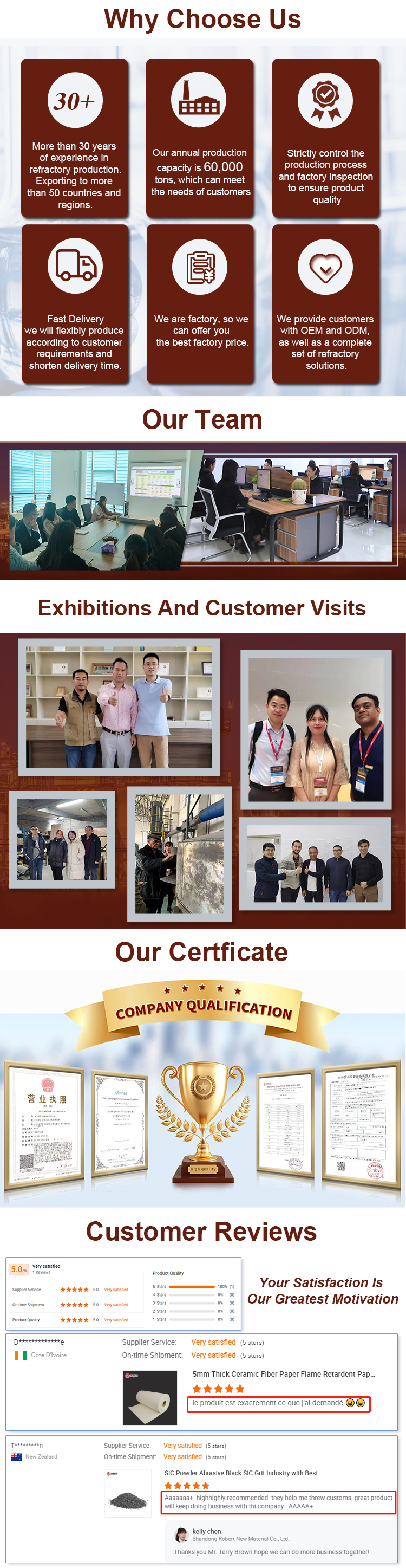
Frequently Asked Questions
Need help? Be sure to visit our support forums for answers to your questions!
We are a real manufacturer, our factory is specialized in producing refractory materials for more than 30 years. We promise to provide the best price, the best pre-sale and after-sale service.
For each production process, RBT has a complete QC system for chemical composition and physical properties. And we will test the goods, and the quality certificate will be shipped with the goods. If you have special requirements, we will try our best to accommodate them.
Depending on the quantity, our delivery time is different. But we promise to ship as soon as possible with guaranteed quality.
Of course, we provide free samples.
Yes, of course, you are welcome to visit RBT company and our products.
There is no limit, we can provide the best suggestion and solution according to your situation.
We have been making refractory materials for more than 30 years, we have strong technical support and rich experience, we can help customers design different kilns and provide one-stop service.