High Alumina Refractory Castable
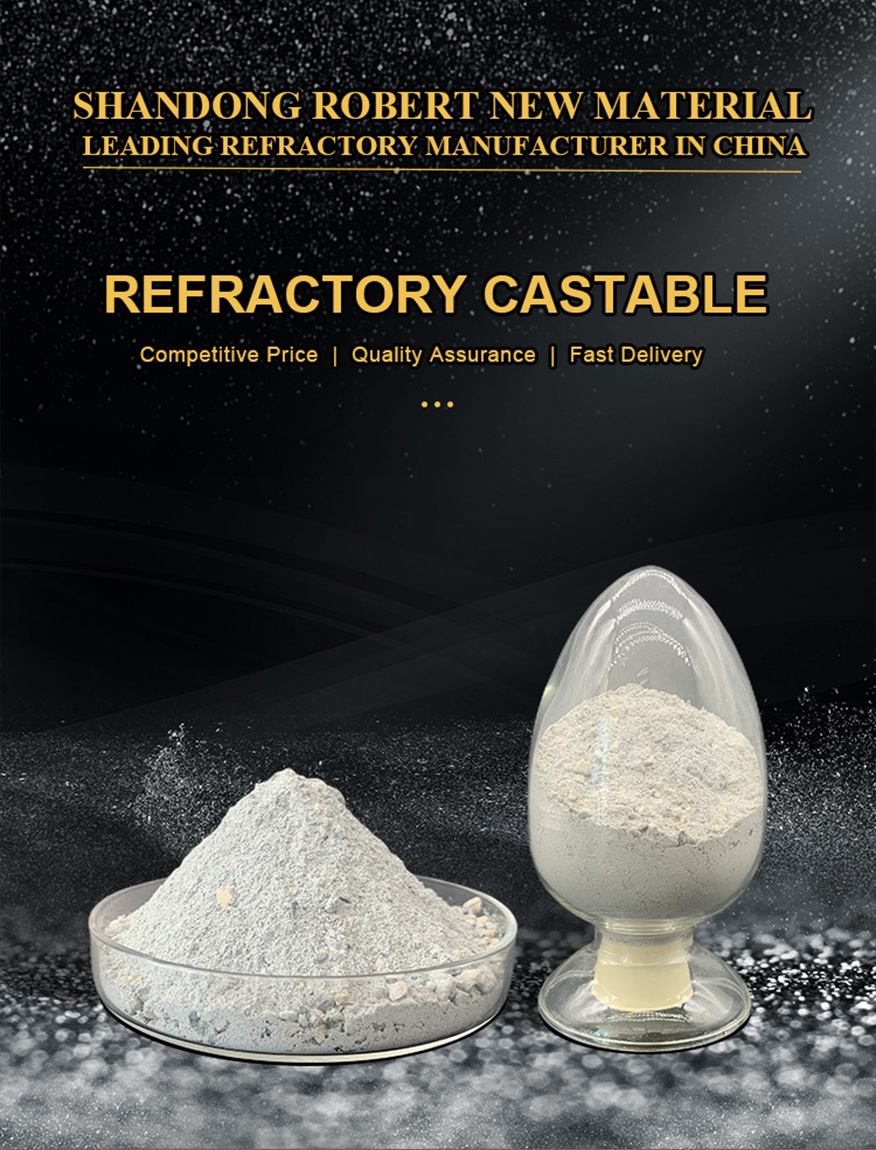
Product Information
Product Name
|
Refractory Castable
|
Categories
|
Low Cement Castable/High Strength Castable/High Alumina Castable/Lightweight Castable
|
Composition
|
Refractory aggregates, powders and binders
|
Features
|
1.Easy Construction,
2.Good Slag Resistance,
3.Good Corrosion Resistance,
4.Good Fire Resistance,
5.Energy Saving And Environmental Protection.
|
Applications
|
Widely Used In Various High Temperature Industrial Furnaces.
|
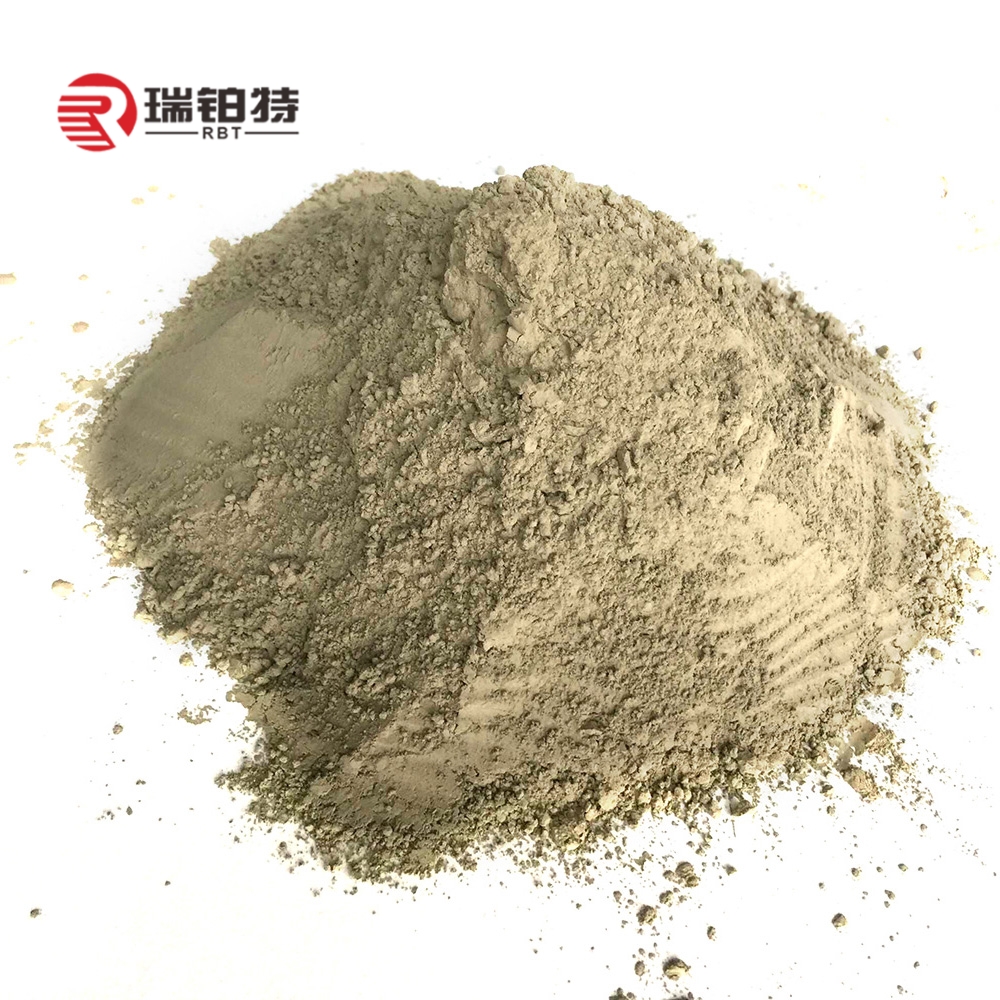
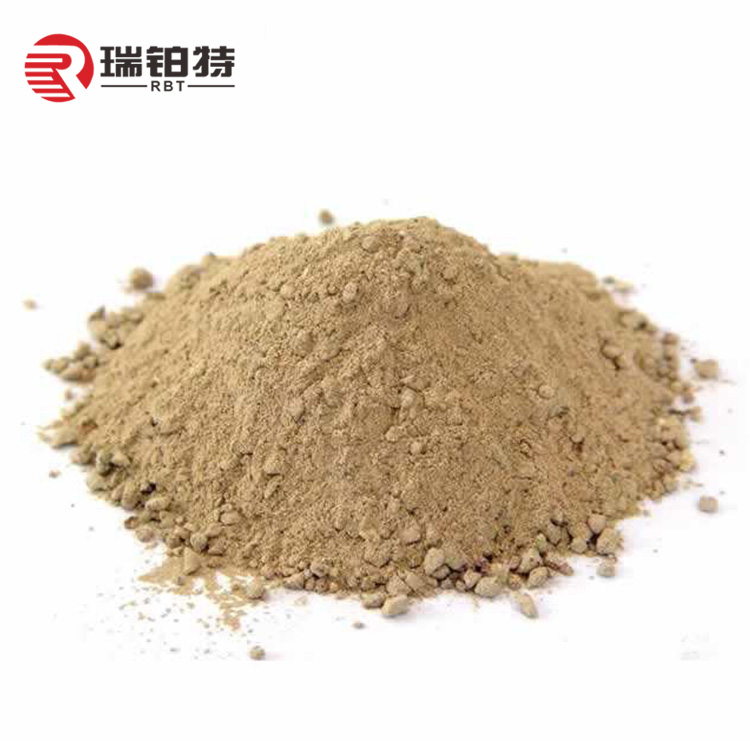
Products
|
Low Cement Castable
|
High Strength Castable
|
Description
|
Low cement castables refer to new castables with very little cement binder. The cement content of refractory castables is generally 15% to 20%, and the cement content of low cement castables is about 5%, and some are even reduced to 1% to 2%.
|
High strength wear-resistant castable is composed of high strength aggregate, mineral admixtures, high strength aggregate and anti crack and wear-resistant agent.
|
Features
|
Thermal shock resistance, slag resistance, and erosion resistance are significantly improved, surpassing similar refractory bricks.
|
High strength, high wear resistance, impact resistance, erosion resistance, anti-oil permeability, arbitrary shape control, strong integrity, simple construction, good construction performance, and long service.
|
Applications
|
1.Lining of various heat treatment furnaces, heating furnaces, shaft kilns, rotary kilns, electric furnace covers, blast furnace tapholes;
2.Self-flowing low-cement castables are suitable for high-temperature spray gun linings for spray metallurgy and petrochemical catalytic cracking reactors Wear-resistant lining, outer lining of heating furnace water-cooled pipe, etc.
|
Lining wear-resistant layer of slag sluice, ore trough, coal spout, hopper and silo in metallurgy, coal, thermal power, chemical, cement and other industries, and the blast furnace mixing silo, sintering silo, feeder, pelletizer, etc.
|
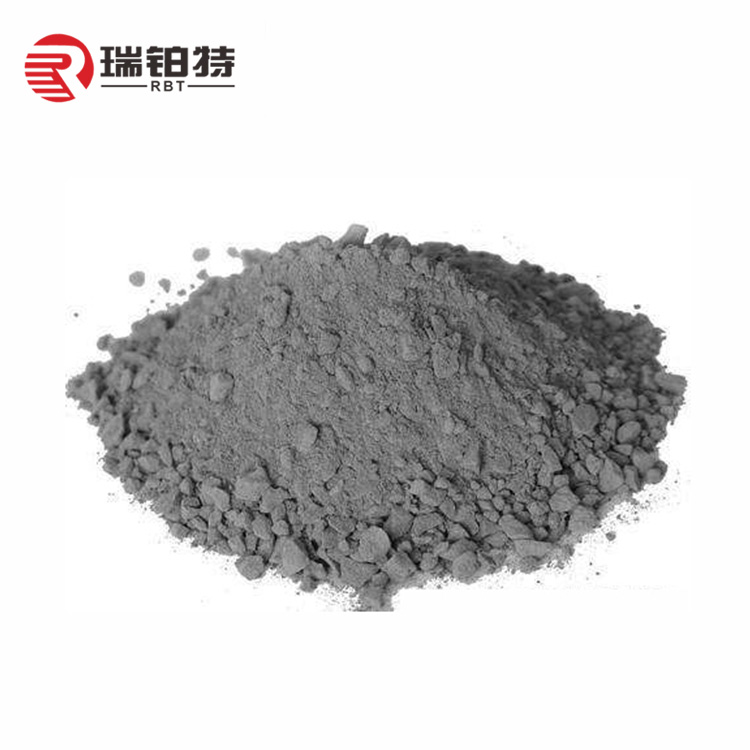
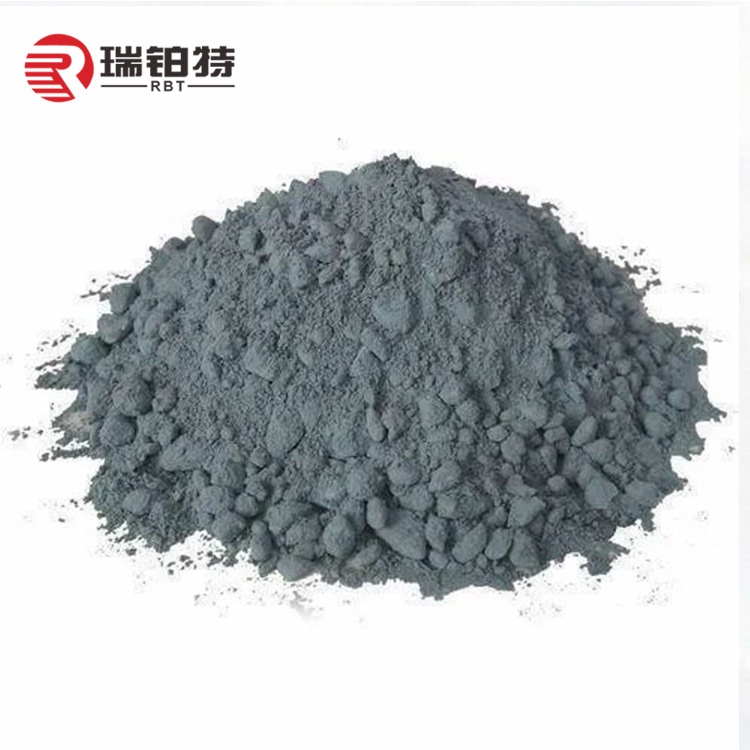
Products
|
High Alumina Castable
|
Lightweight Castable
|
Description
|
High-alumina castables are refractory castables made of high-alumina raw materials as aggregates and powders, and added with binders.
|
The lightweight castable with low bulk density is made of aluminate cement, high alumina fine material, ceramsite, and additives.
|
Features
|
Has high mechanical strength and good thermal shock resistance, abrasion resistance and other properties.
|
Low bulk density, small thermal conductivity, good thermal insulation effect, high compressive strength, acid and acid gas corrosion resistance, heat insulation, thermal insulation, and low water absorption.
|
Applications
|
It is mainly used as the inner lining of boilers, blast furnace hot blast stoves, heating furnaces, ceramic kilns and other kilns.
|
The lightweight castable can be used for the thermal insulation layer of high-temperature industrial furnace and equipment also used for the lining of various high-temperature gas pipe.
|
Product Index
Product Name
|
High Alumina Castable
|
||||||
INDEX
|
Al2O3(%)≥
|
CaO(%)≥
|
Refractoriness(℃)
|
CT℃×3h PLC ≤1%
|
110℃After Drying (MPa)
|
||
CCS
|
MOR
|
||||||
Clay Bonded
|
NL-45
|
45
|
―
|
1700
|
1350
|
8
|
1
|
NL-60
|
60
|
―
|
1720
|
1400
|
9
|
1.5
|
|
NL-70
|
70
|
―
|
1760
|
1450
|
10
|
2
|
|
Cement Bonded
|
GL-42
|
42
|
―
|
1640
|
1350
|
25
|
3.5
|
GL-50
|
50
|
―
|
1660
|
1400
|
30
|
4
|
|
GL-60
|
60
|
―
|
1700
|
1400
|
30
|
4
|
|
GL-70
|
70
|
―
|
1720
|
1450
|
35
|
5
|
|
GL-85
|
85
|
―
|
1780
|
1500
|
35
|
5
|
|
Low Cement Bonded
|
DL-60
|
60
|
2.5
|
1740
|
1500
|
30
|
5
|
DL-80
|
80
|
2.5
|
1780
|
1500
|
40
|
6
|
|
Phosphate Bonded
|
LL-45
|
45
|
―
|
1700
|
1350
|
20
|
3.5
|
LL-60
|
60
|
―
|
1740
|
1450
|
25
|
4
|
|
LL-75
|
75
|
―
|
1780
|
1500
|
30
|
5
|
|
Sodium Silicate Bonded
|
BL-40
|
40
|
―
|
―
|
1000
|
20
|
―
|
Application
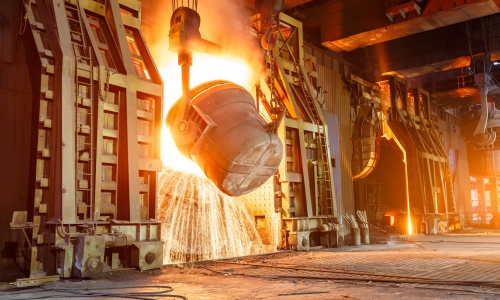
Iron and steel industry: Mainly used for maintenance and patching of electric arc furnaces, steelmaking furnaces, ladles and other equipment.
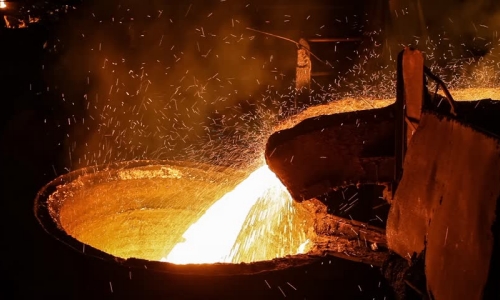
Non-ferrous metal industry: Used for patching and repairing of copper, aluminum, zinc, nickel and other non-ferrous metal smelting furnaces and converters.
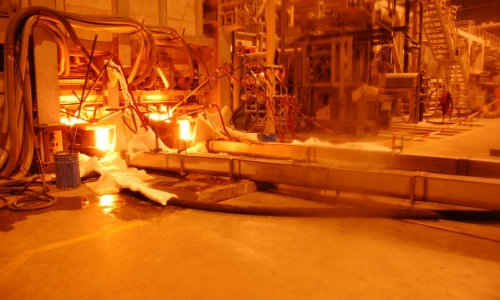
Glass industry: Used for maintenance and patch work of glass furnaces, annealing furnaces and other equipment.
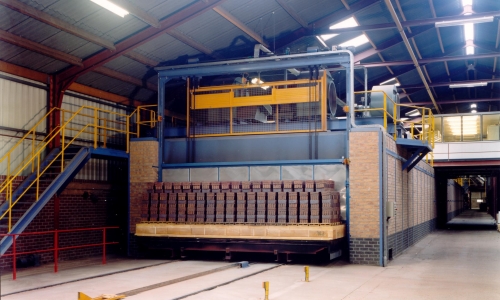
Building materials industry: Used for maintenance and patching of building materials production equipment such as cement rotary kiln and gypsum kiln.
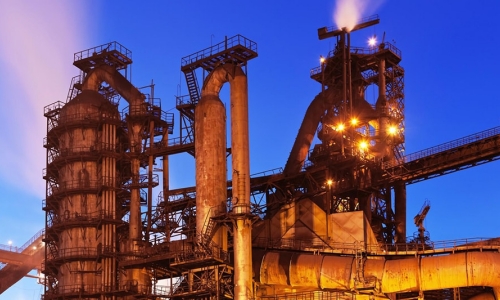
Chemical industry: Used for maintenance and patching of high-temperature chemical equipment such as catalytic cracking furnaces and gasifiers.
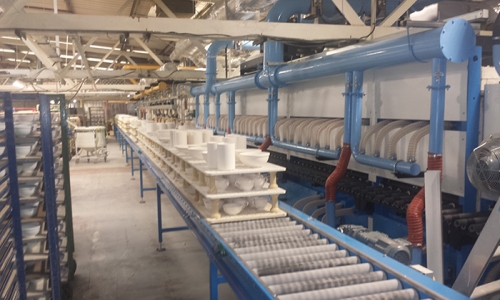
Ceramic industry: Used for maintenance and repair of ceramic production equipment such as tunnel kiln and shuttle kiln.
Package&Warehouse
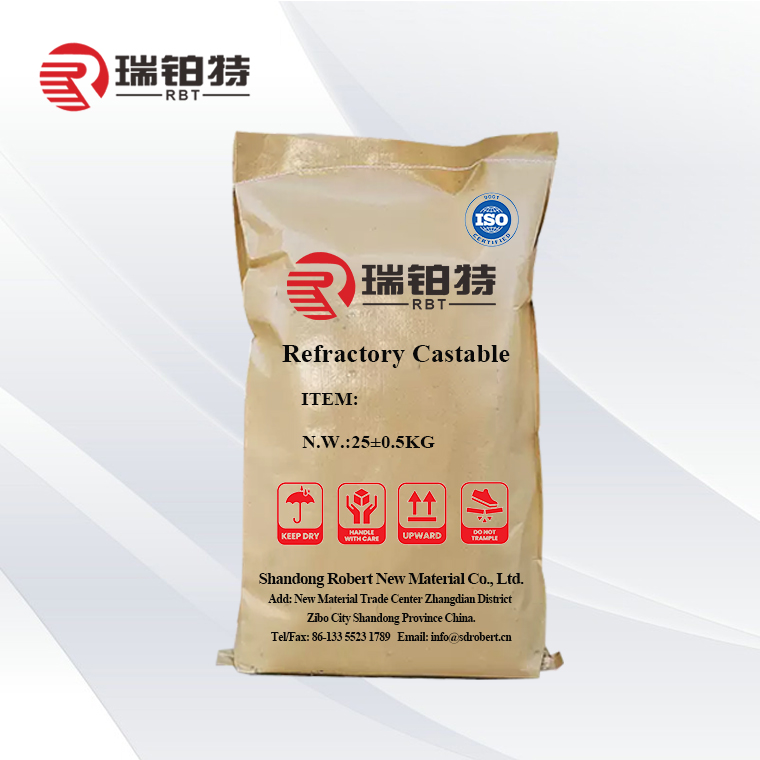
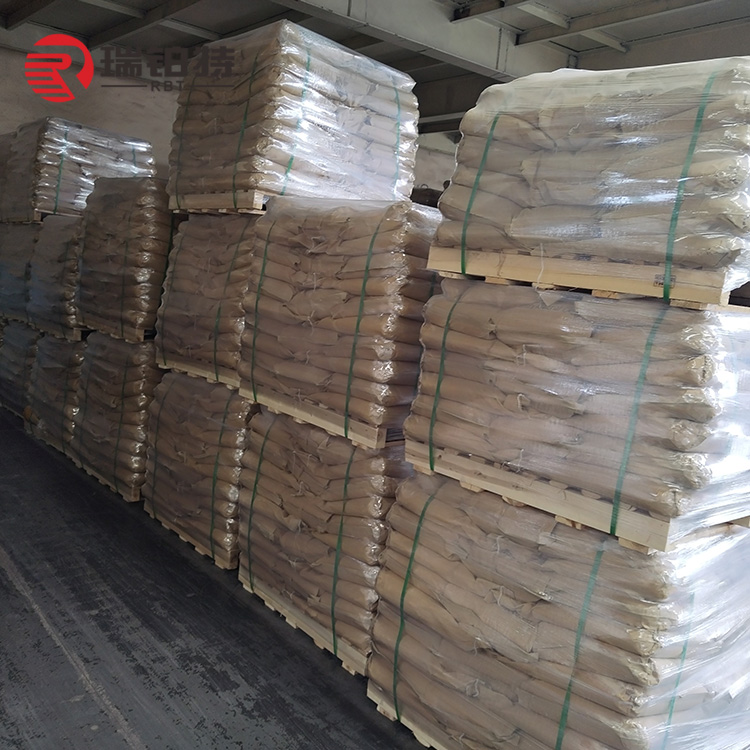
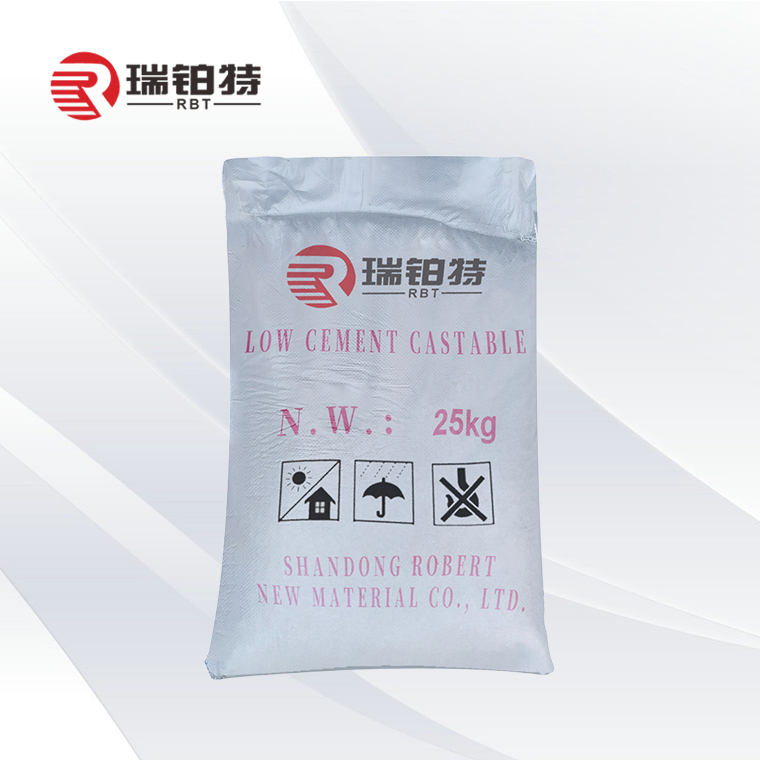
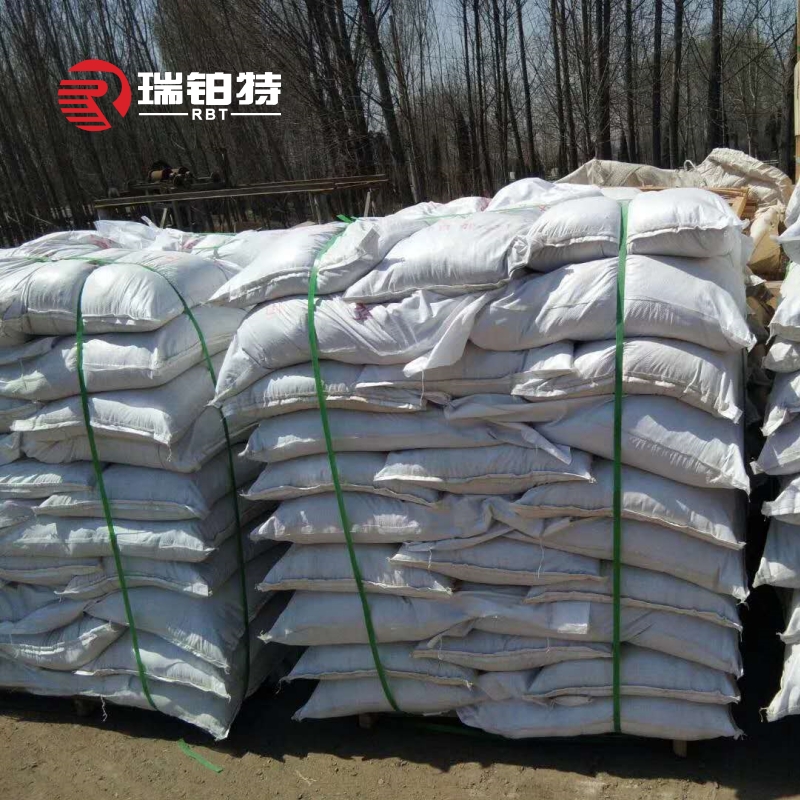