01 Sintered Corundum
Sintered corundum, also known as sintered alumina or semi-molten alumina, is a refractory clinker made from calcined alumina or industrial alumina as raw material, ground into balls or green bodies, and sintered at a high temperature of 1750~1900°C.
Sintered alumina containing more than 99% of aluminum oxide is mostly made of uniform fine-grained corundum directly combined. The gas emission rate is below 3.0%, the volume density reaches 3.60%/cubic meter, the refractoriness is close to the melting point of corundum, it has good volume stability and chemical stability at high temperatures, and is not eroded by reducing atmosphere, molten glass and molten metal. , good mechanical strength and wear resistance at normal temperature and high temperature.
02 Fused Corundum
Fused corundum is artificial corundum made by melting pure alumina powder in a high-temperature electric furnace. It has the characteristics of high melting point, high mechanical strength, good thermal shock resistance, strong corrosion resistance and small linear expansion coefficient. Fused corundum is a raw material for manufacturing high-grade special refractory materials. Mainly include fused white corundum, fused brown corundum, sub-white corundum, etc.
03 Fused White Corundum
Fused white corundum is made from pure alumina powder and smelted at high temperature. It is white in color. The smelting process of white corundum is basically a process of melting and recrystallization of industrial alumina powder, and there is no reduction process. The Al2O3 content is not less than 9%, and the impurity content is very small. The hardness is slightly smaller than brown corundum and the toughness is slightly lower. Often used to make abrasive tools, special ceramics and advanced refractory materials.
04 Fused Brown Corundum
Fused brown corundum is made from high-alumina bauxite as the main raw material and mixed with coke (anthracite), and is smelted in a high-temperature electric furnace at temperatures above 2000°C. Fused brown corundum has a dense texture and high hardness and is often used in ceramics, precision castings and advanced refractory materials.
05 Sub-white Corundum
Subwhite corundum is produced by electromelting special grade or first grade bauxite under reducing atmosphere and controlled conditions. When melting, add reducing agent (carbon), settling agent (iron filings) and decarburizing agent (iron scale). Because its chemical composition and physical properties are close to white corundum, it is called sub-white corundum. Its bulk density is above 3.80g/cm3 and its apparent porosity is less than 4%. It is an ideal material for manufacturing advanced refractory materials and wear-resistant materials.
06 Chrome corundum
On the basis of white corundum, 22% chromium is added, and it is made by smelting in an electric arc furnace. The color is purple-red. The hardness is slightly higher than brown corundum, similar to white corundum, and the microhardness can be 2200-2300Kg/mm2. The toughness is higher than that of white corundum and slightly lower than that of brown corundum.
07 Zirconium Corundum
Zirconium corundum is a kind of artificial corundum made by smelting alumina and zirconium oxide at high temperature in an electric arc furnace, crystallizing, cooling, crushing and screening. The main crystal phase of zirconium corundum is α-Al2O3, the secondary crystal phase is baddeleyite, and there is also a small amount of glass phase. The crystal morphology and structure of zirconium corundum are important factors affecting its quality. Zirconium corundum has the characteristics of high hardness, good toughness, high strength, dense texture, strong grinding force, stable chemical properties, and good thermal shock resistance. It is widely used in abrasives and refractory materials industries. According to its zirconium oxide content, it can be divided into two product levels: ZA25 and ZA40.
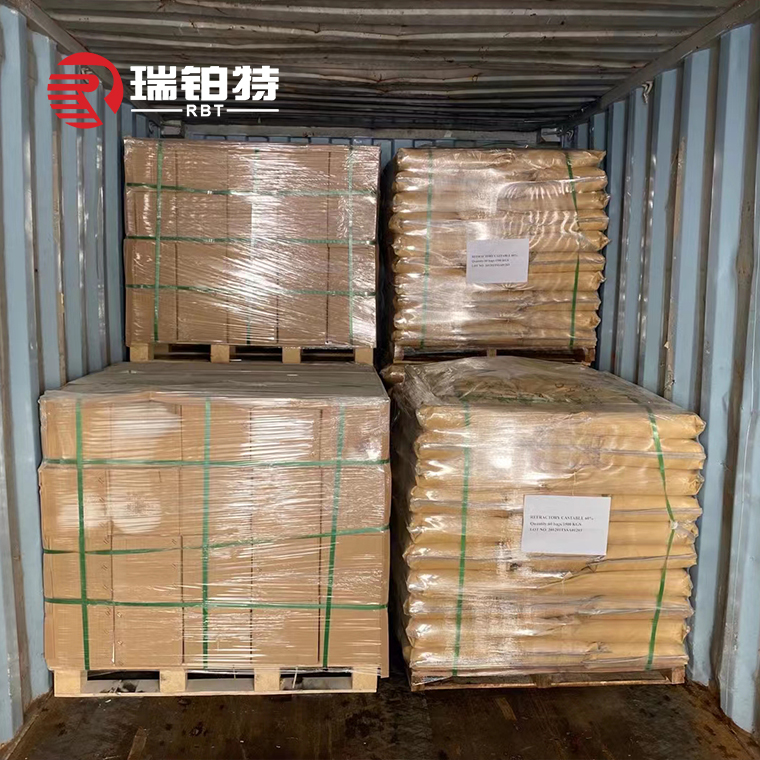
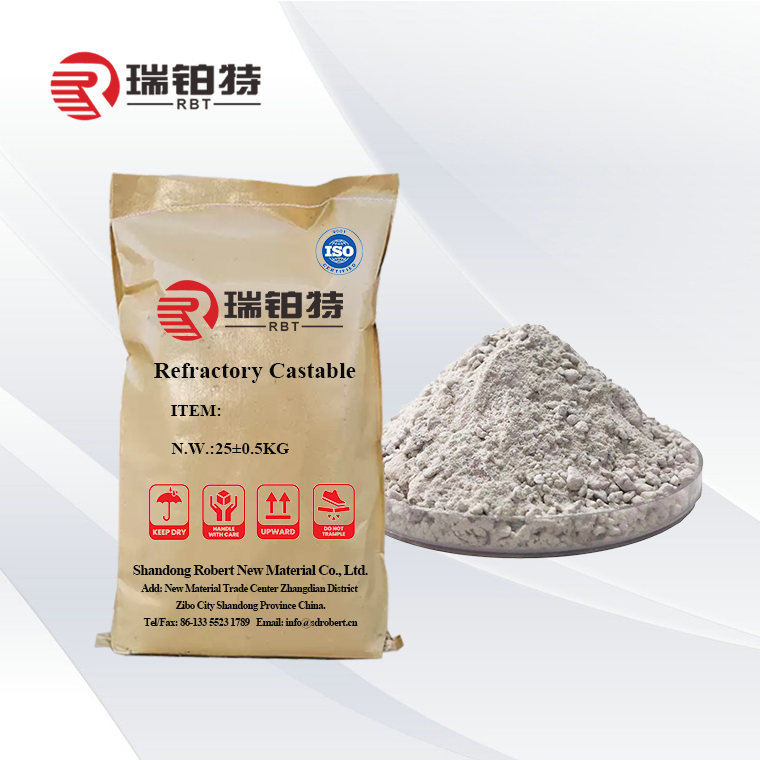
Post time: Feb-20-2024