Product performance: It has strong high temperature volume stability, excellent thermal shock resistance, wear resistance, chemical corrosion resistance and other characteristics.
Main uses: Mainly used in transition zones of cement rotary kilns, decomposition furnaces, tertiary air ducts, and other thermal equipment that require thermal shock resistance.
Product features: As the basic material of the refractory industry, high alumina bricks have the characteristics of high refractoriness, relatively high load-softening temperature (around 1500°C), and good erosion resistance. They are widely used in industrial kilns in various industries. However, , due to the high corundum phase content of ordinary high alumina bricks, the corundum phase crystals in the sintered products are larger, and cracking and peeling are prone to occur when encountering rapid cooling and heating conditions. The thermal shock stability under 1100°C water cooling conditions is only Can reach 2-4 times. In the cement production system, due to sintering temperature limitations and performance requirements for refractory materials to adhere to the kiln skin, high alumina bricks can only be used in the transition zone of the rotary kiln, the kiln tail and the preheater of the decomposition furnace.
Anti-spalling high alumina bricks are high-aluminum bricks with anti-flaking properties produced based on high-aluminum clinker and added with ZrO2 or other materials. They can be divided into two categories, one is anti-flaking high-alumina bricks containing ZrO2, and the other is The first type is anti-flaking high alumina brick that does not contain ZrO2.
Anti-spalling high-alumina bricks can resist high-temperature heat loads, do not shrink in volume and have uniform expansion, do not creep or collapse, have very high normal temperature strength and high-temperature thermal strength, high load softening temperature, and have good heat resistance. It can withstand the impact of sudden temperature changes or uneven heating, and will not crack or peel off. The difference between anti-flaking high alumina bricks containing ZrO2 and anti-flaking high alumina bricks without ZrO2 lies in their different anti-flaking mechanisms. ZrO2-containing anti-flaking high alumina bricks use zircon materials to make use of excellent corrosion resistance. ZrO2 resists the erosion of sulfur-chlor-alkali. At the same time, at high temperatures, the SiO2 contained in zircon will undergo a crystal phase transformation from cristobalite to a quartz phase, resulting in a certain volume expansion effect, thus reducing the risk of sulfur-chlor-alkali prevention. At the same time, it prevents spalling during hot and cold processes; anti-flaking high alumina bricks that do not contain ZrO2 are produced by adding andalusite to the high alumina bricks. The andalusite in the product is used for secondary mulliteization in the cement kiln. It produces an irreversible micro-expansion effect so that the product will not shrink when it is cooled, offsetting the shrinkage stress and preventing structural peeling.
Compared with anti-spalling high-alumina bricks that do not contain ZrO2, anti-spalling high-alumina bricks containing ZrO2 have better resistance to the penetration and erosion of sulfur, chlorine and alkali components, so they have better anti-flaking properties. However, because ZrO2 is a rare material, it is expensive , so the cost and price are higher. Anti-flaking high-alumina bricks containing ZrO2 are only used in the transition zone of cement rotary kilns. Anti-flaking high-alumina bricks that do not contain ZrO2 are mostly used in decomposition furnaces of cement production lines.
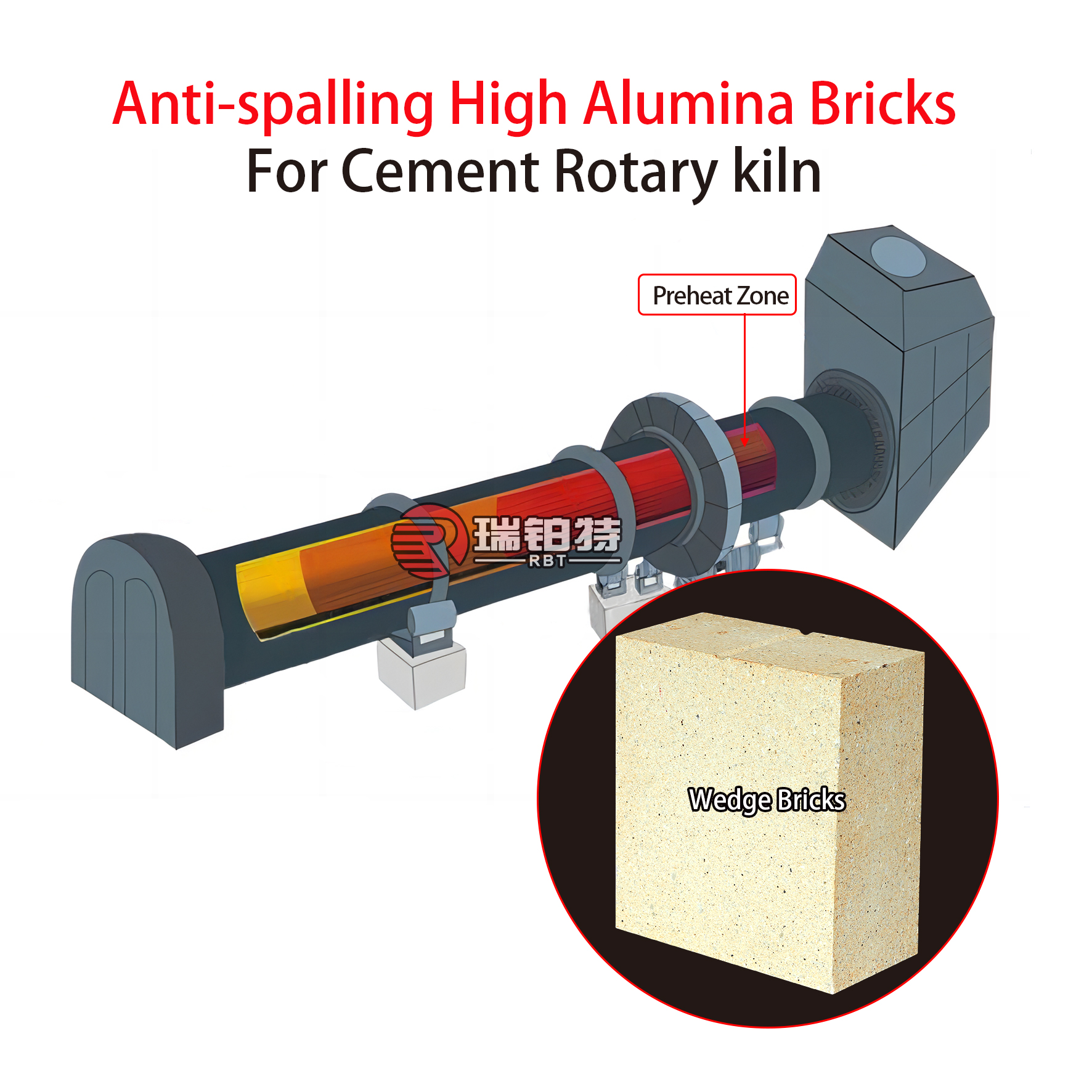
Post time: Mar-28-2024