There are many types of refractory materials used in coke ovens, and each material has its specific application scenarios and performance requirements. The following are the commonly used refractory materials in coke ovens and their precautions:
1. Commonly used refractory materials in coke ovens
Silicon bricks
Features: high temperature resistance (above 1650℃), acid corrosion resistance, and good thermal stability.
Application: Mainly used in high-temperature areas such as the combustion chamber, carbonization chamber, and furnace top of the coke oven.
Precautions:
Silicon bricks are prone to crystal transformation below 600℃, resulting in volume changes, so they should be avoided in low-temperature areas.
During construction, the brick joints must be strictly controlled to prevent the expansion of the brick joints at high temperatures.
High-alumina bricks
Features: high refractoriness (above 1750℃), good thermal shock resistance, and strong corrosion resistance.
Application: Used in the furnace wall, furnace bottom, heat storage chamber and other parts of the coke oven.
Precautions:
High-alumina bricks have weak resistance to alkaline corrosion and need to avoid direct contact with alkaline substances.
During construction, attention should be paid to the drying and baking of the brick body to prevent cracking.
Fire Clay brick
Features: good heat resistance, low cost, good thermal shock resistance.
Application: used in low-temperature areas such as the flue of the coke oven and the lower part of the heat storage chamber.
Notes:
The refractoriness of clay bricks is low and is not suitable for high-temperature areas.
Pay attention to moisture-proof to avoid strength loss after water absorption.
Magnesium brick
Features: high refractoriness and strong resistance to alkaline erosion.
Application: used in the bottom and furnace of the coke oven and other parts that come into contact with alkaline substances.
Notes:
Magnesium bricks are easy to absorb water and need to be properly stored to avoid moisture.
The thermal expansion coefficient of magnesium bricks is large, and attention should be paid to thermal shock problems.
Silicon carbide bricks
Features: high thermal conductivity, wear resistance, and excellent thermal shock resistance.
Application: used in the furnace door, furnace cover, burner and other parts of the coke oven that require rapid heat dissipation.
Notes:
Silicon carbide bricks are expensive and need to be selected reasonably.
Avoid contact with strong oxidizing gases to prevent oxidation.
Refractory castables
Features: easy construction, good integrity, and excellent thermal shock resistance.
Application: Used for coke oven repairs, complex shape parts and integral casting.
Notes:
The amount of water added during construction must be strictly controlled to avoid affecting the strength.
The temperature must be raised slowly during baking to prevent cracking.
Refractory fiber
Features: light weight, good thermal insulation, and excellent thermal shock resistance.
Application: Used for the insulation layer of coke ovens to reduce heat loss.
Notes:
Refractory fibers are not resistant to mechanical impact and need to be avoided from external damage.
Shrinkage may occur under long-term high temperatures and requires regular inspection.
Corundum bricks
Features: extremely high refractoriness (above 1800°C) and strong corrosion resistance.
Application: Used in high-temperature and high-erosion areas of coke ovens, such as around burners.
Precautions:
Corundum bricks are expensive and need to be selected reasonably.
Pay attention to the compactness of brick joints during construction.
2. Precautions for the use of coke oven refractory materials
Material selection
Select refractory materials reasonably according to the temperature of different parts of the coke oven, corrosive media (acidic or alkaline) and mechanical load.
Avoid using low-temperature refractory materials in high-temperature areas to prevent material failure.
Construction quality
Strictly control the size of brick joints and use appropriate refractory mud to ensure the density of masonry.
For refractory castables, construction must be carried out according to the ratio to avoid excessive water addition affecting the strength.
Oven baking operation
Newly built or repaired coke ovens need to be baked. The temperature should be raised slowly during baking to avoid cracking or peeling of refractory materials due to sudden temperature changes.
Daily maintenance
Regularly check the wear, erosion and cracking of coke oven refractory materials and repair them in time.
Avoid over-temperature operation of coke ovens to prevent premature damage to refractory materials.
Storage and preservation
Refractory materials should be stored in a dry environment to avoid moisture (especially magnesia bricks and refractory castables).
Refractory materials of different materials should be stored separately to prevent confusion.
Summary
The commonly used refractory materials in coke ovens include silica bricks, high alumina bricks, clay bricks, magnesia bricks, silicon carbide bricks, refractory castables, refractory fibers and corundum bricks. When using, materials should be selected according to specific working conditions, and attention should be paid to construction quality, oven operation and daily maintenance to extend the service life of the coke oven.
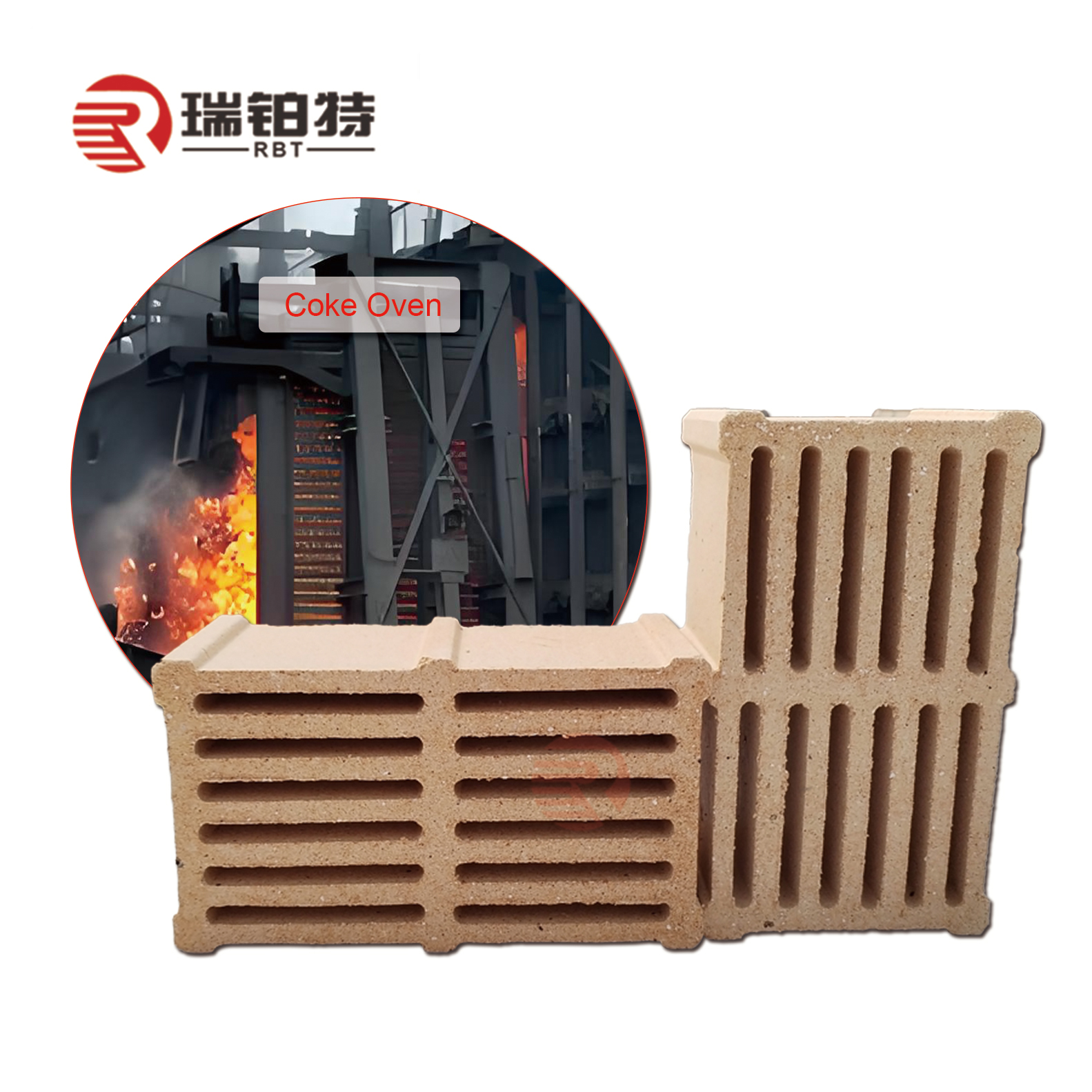
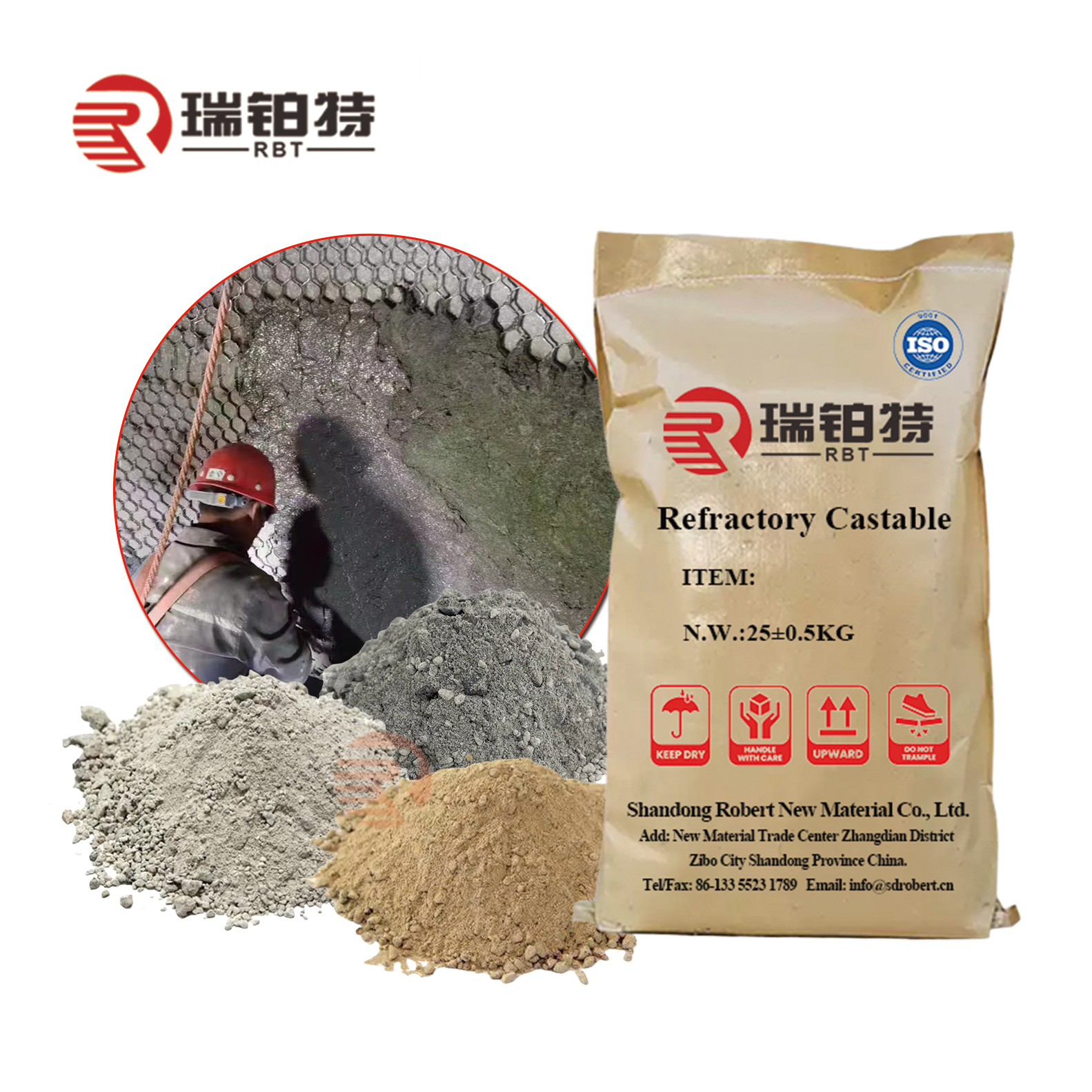
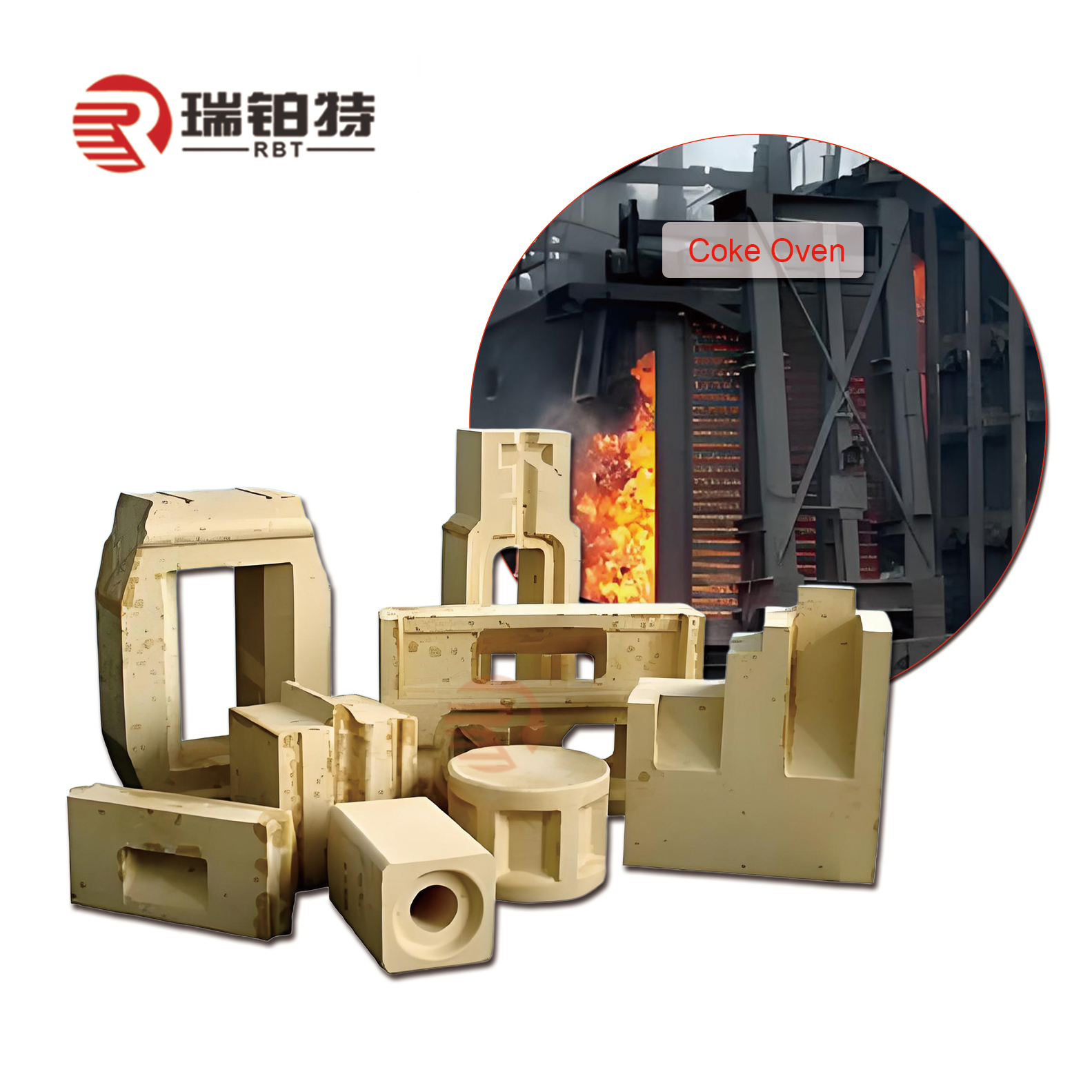
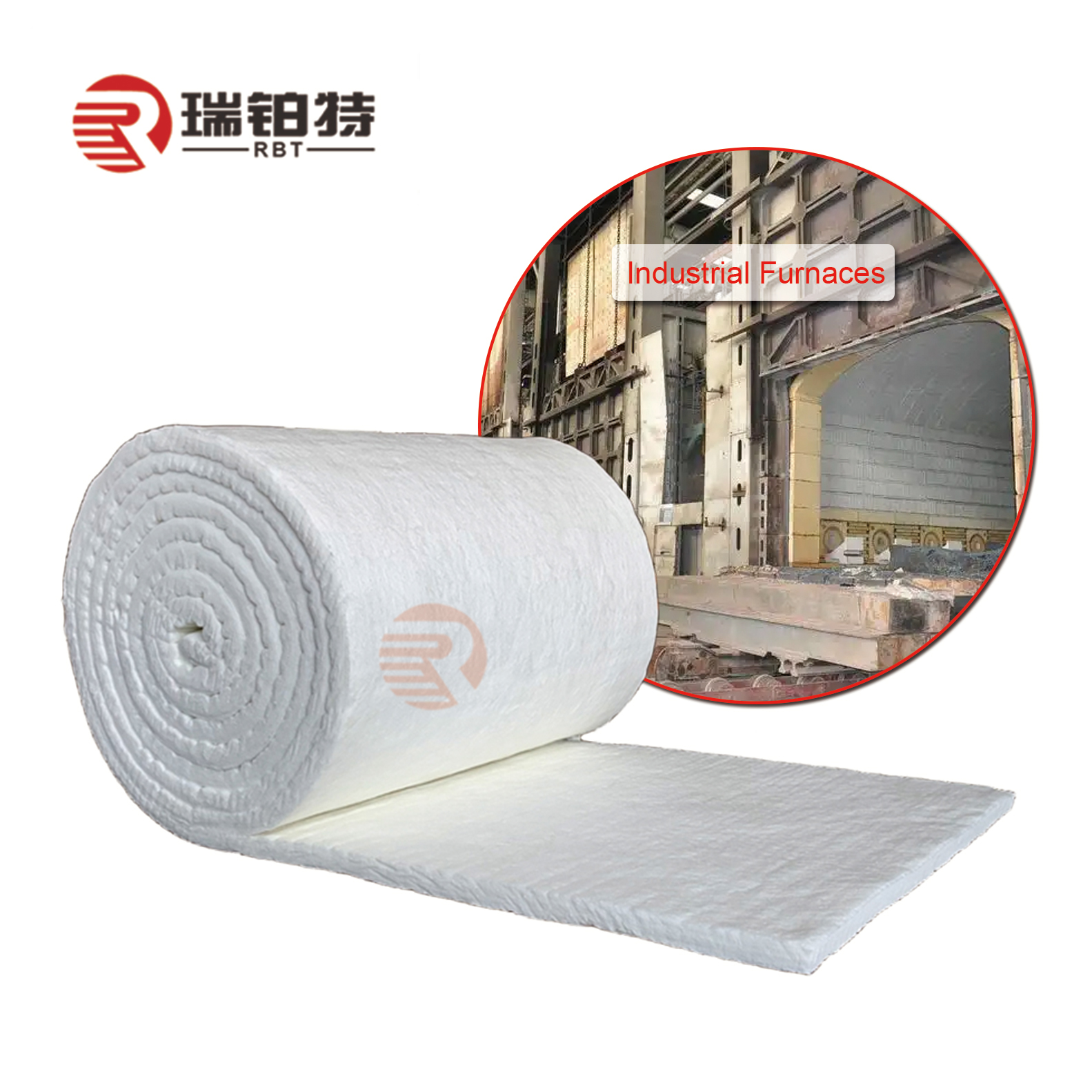
Post time: Mar-05-2025