Magnesium carbon brick is a non-burning carbon composite refractory material made of high-melting alkaline oxide magnesium oxide (melting point 2800℃) and high-melting carbon material (such as graphite) that is difficult to be wetted by slag as the main raw materials, various non-oxide additives are added, and the slag line of the ladle is combined with a carbon binder. Magnesium carbon brick is mainly used for the lining of converters, AC arc furnaces, DC arc furnaces, and slag lines of ladles.
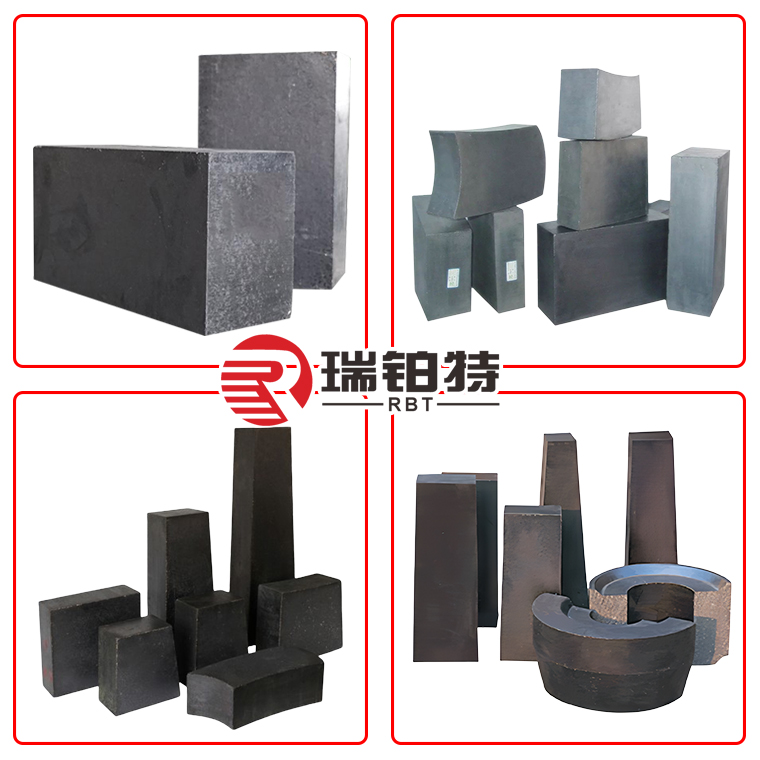
Features
High temperature resistance: Magnesium carbon bricks can remain stable in high temperature environments and have excellent high temperature resistance.
Anti-slag erosion performance: Carbon materials have excellent resistance to acid and alkali slag erosion, so that magnesium carbon bricks can better resist chemical erosion by molten steel and slag.
Thermal conductivity: Carbon materials have high thermal conductivity, can quickly conduct heat, and reduce the damage of thermal stress to the brick body.
Thermal shock resistance: The addition of graphite improves the thermal shock resistance of magnesium carbon bricks, which can withstand rapid temperature changes and reduce the risk of cracking.
Mechanical strength: The high strength of magnesia and the high toughness of graphite make magnesia carbon bricks have high mechanical strength and impact resistance.
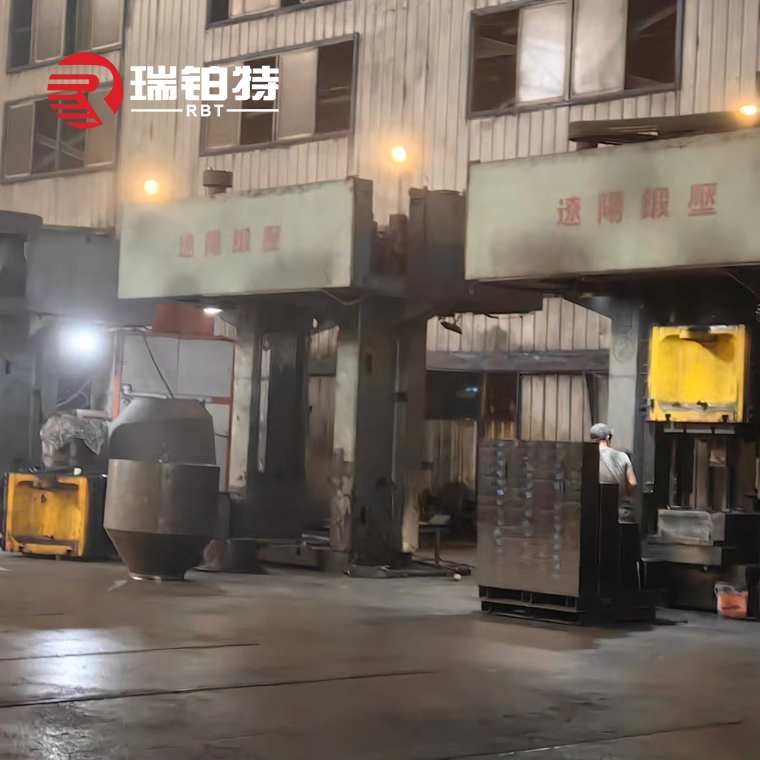
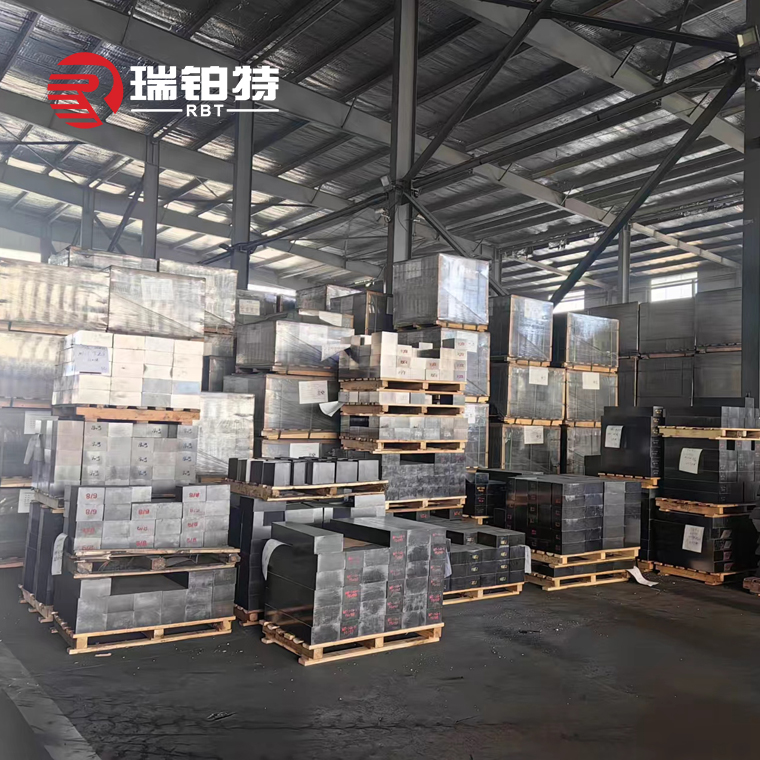
Application areas
Magnesium carbon bricks are mainly used in key refractory parts of high-temperature industries, especially in steel smelting:
Converter: Used in the lining, furnace mouth, and slag line area of the converter, which can withstand the erosion of molten steel and slag.
Electric arc furnace: Used in the furnace wall, furnace bottom and other parts of the electric arc furnace, which can withstand high temperature and scouring.
Ladle: Used in the lining and furnace cover of the ladle, resisting the chemical erosion of molten steel and extending the service life.
Refining furnace: Suitable for key parts of refining furnaces such as LF furnaces and RH furnaces, meeting the requirements of high-temperature refining processes.
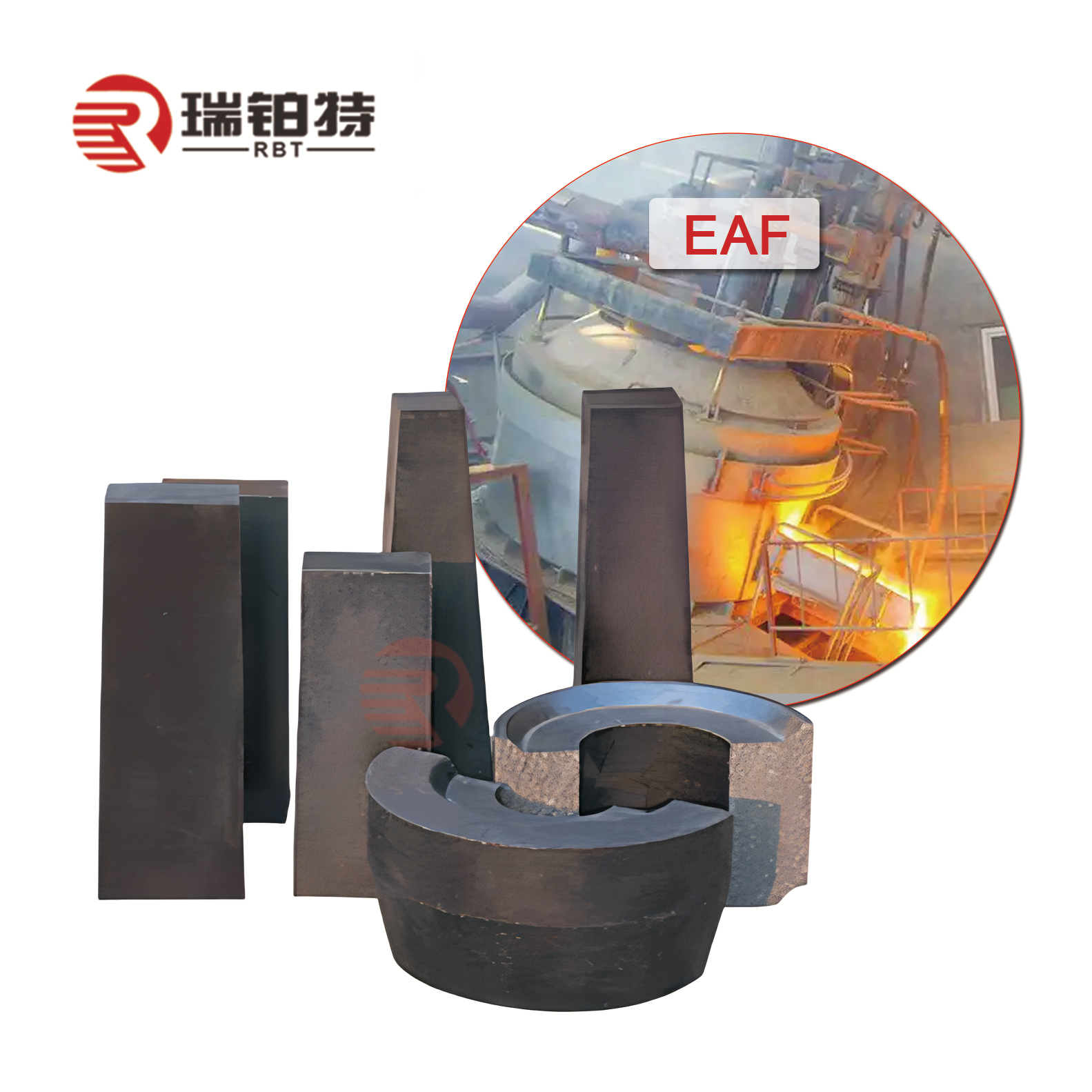
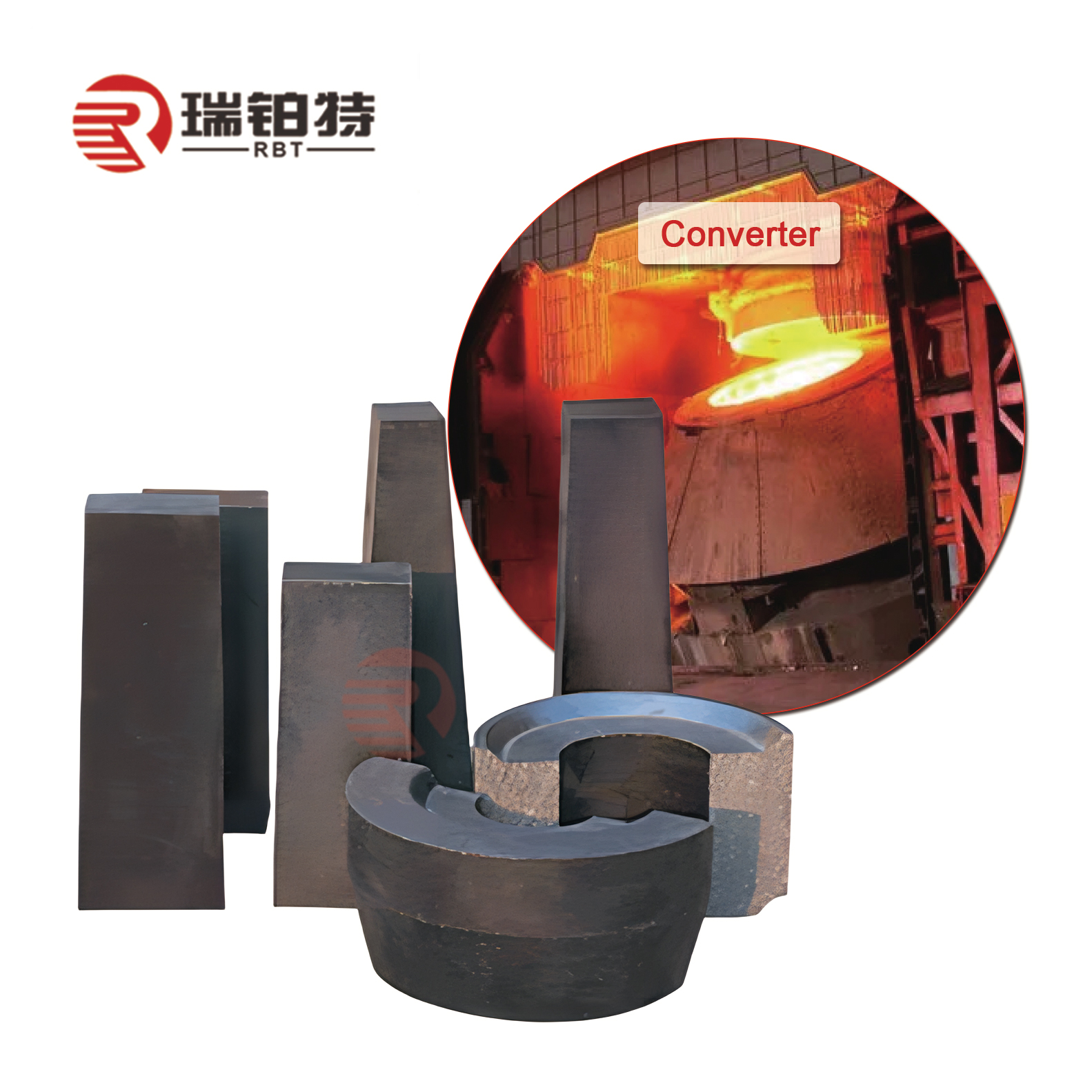
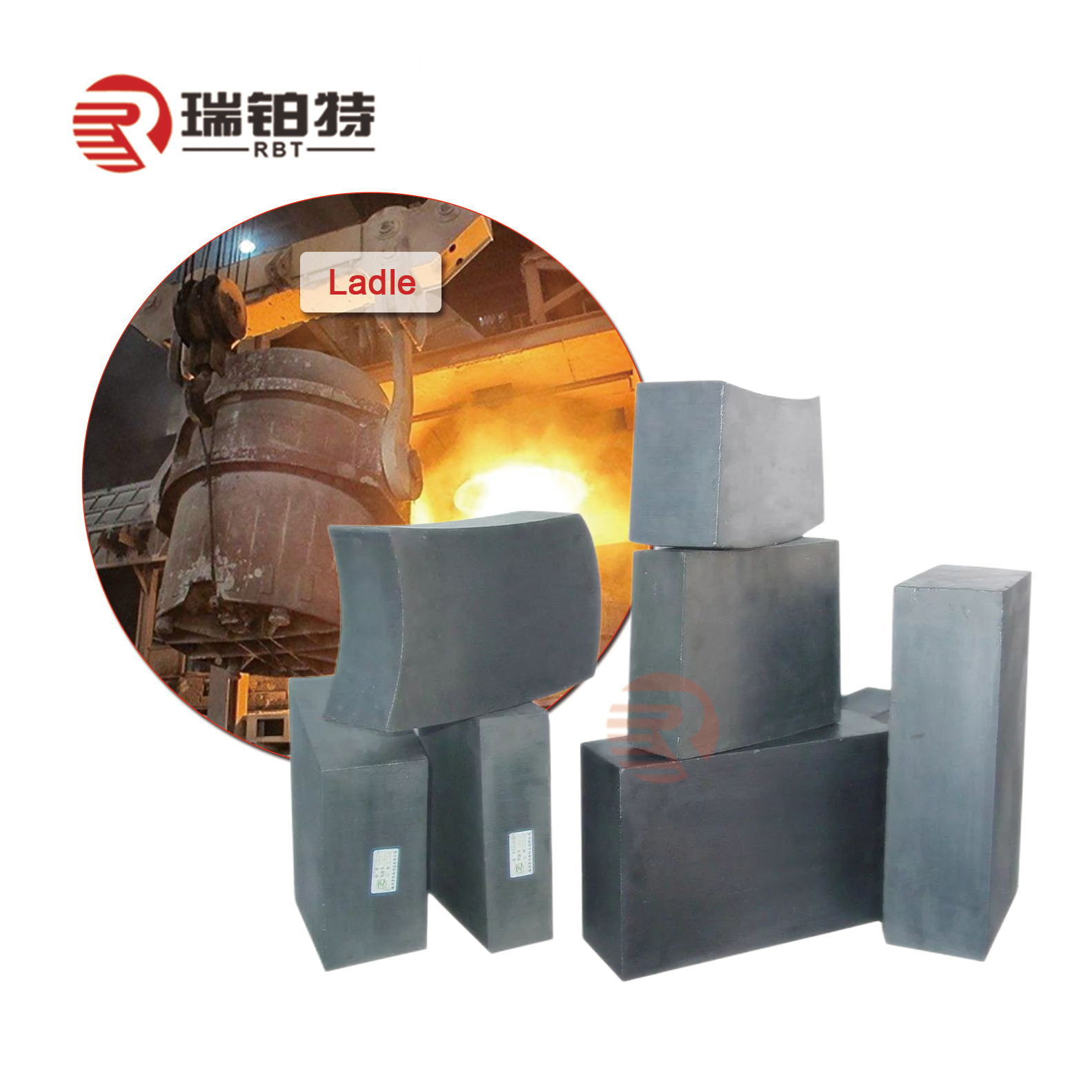
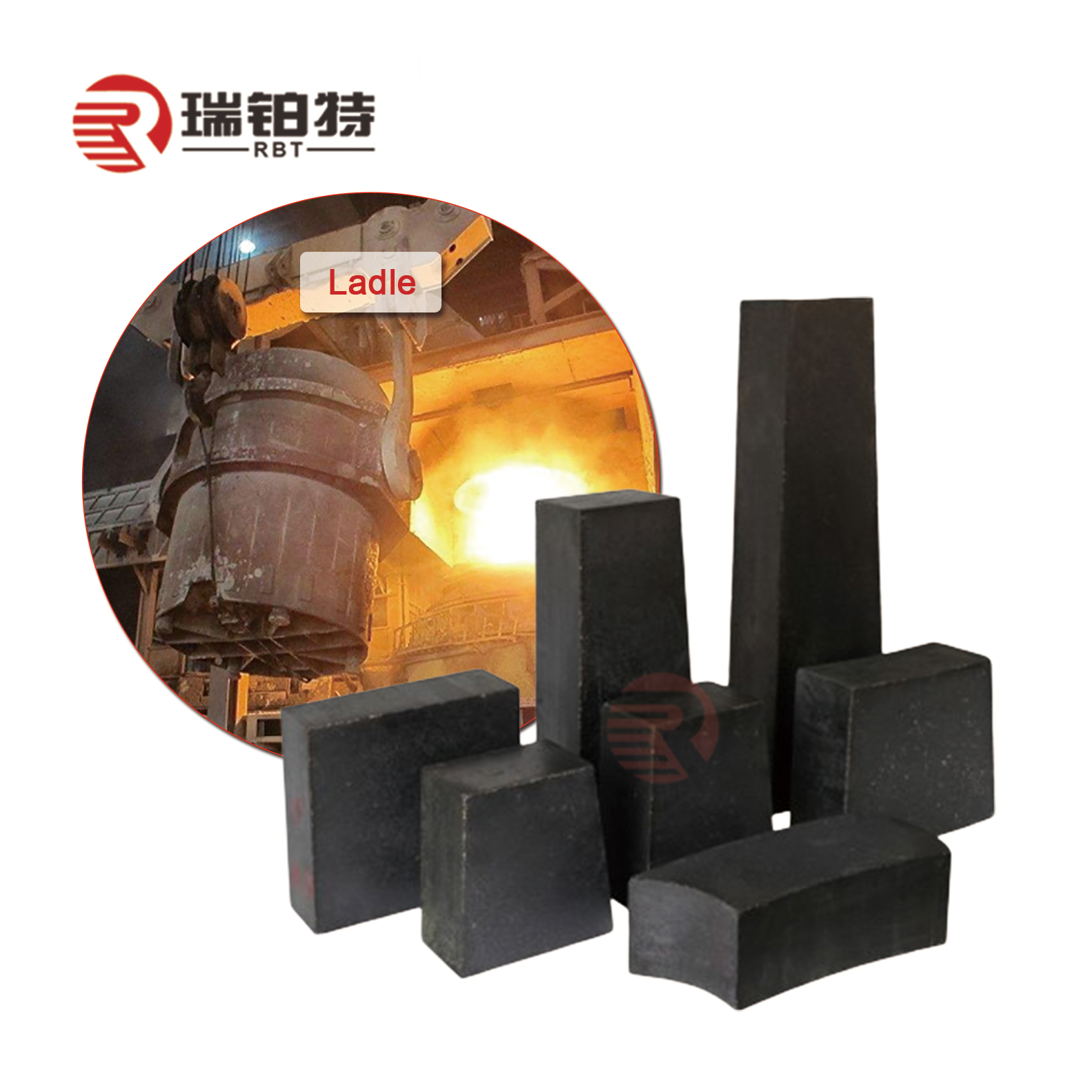
Post time: Jan-21-2025